Part 2: Model-less multivariable control (XMC) is designed to solve multivariable control challenges without using detailed models or embedded optimizers.
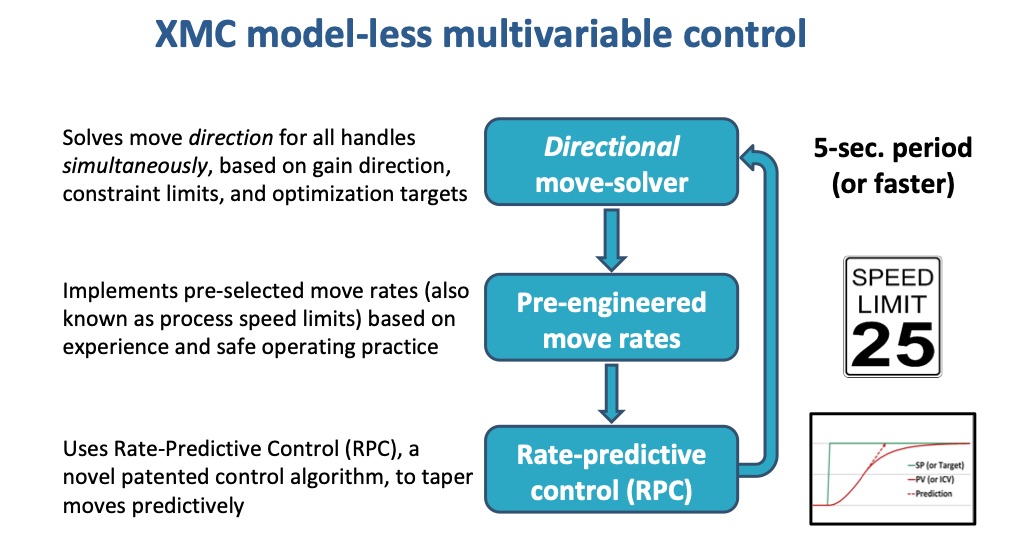
The term “model-based multivariable control” has been so ubiquitous for so long that many engineers don’t realize they can have multivariable control without all the work of models.
Rather than being the latest twist in multivariable control, model-less multivariable control (XMC) represents a return to basics. XMC solves the multivariable control problem in a simpler and more reliable way without using detailed models or online optimizers.
In conventional model-based multivariable control, model-related activities account for 90% or more of engineering and maintenance costs, yet nearly all reliability and performance issues continue to be attributed to poor model quality, with little reason to expect this to change (Control Engineering, September 2018, “The big story behind auto-tuning”).
Today, most advanced process control (APC) resources are consumed in support of existing applications, and not new applications. This leaves many APC needs unmet, opportunities uncaptured, and problems unsolved. XMC offers a path out of this unsustainable predicament.
How does XMC work?
XMC automates the way operating teams have managed process constraints and optimized operation manually without the need for detailed models or online optimizers. Important process constraints, the main handles, economic optimization drivers, and safe move sizes, are not secrets to be teased out of model details. They are basic knowledge among operating team members (Figure 1):
- Important constraints, relevant handles, optimization goals, and gain directions (not detailed models) are captured in an otherwise conventional multivariable control matrix; this is sufficient for XMC (or anyone) to determine the correct move direction for each handle
- XMC implements pre-engineered move rates for each handle based on established safe operating practices, also known as “process speed limits”
- XMC monitors the actual ongoing process response (not yesterday’s or last year’s response) and makes further move rate adjustments accordingly, using rate-predictive control (RPC), a new patented single-loop control algorithm, to taper moves predictively.
Historically, the quality of manual multivariable control has been dependent upon the time, initiative, and level of expertise of individual operators. These – timeliness and consistency – are the hallmarks of automation, which XMC captures.
XMC uses RPC internally
Part 1 of this series (“What is rate-predictive control?”) focused on RPC, which was developed in conjunction with XMC. It is based on the concept of automating traditional proven manual control methods, and incorporating (being careful not to leave behind) important process control principles and wisdom. RPC is the resulting single-loop solution, while XMC is the multivariable control solution, which uses RPC internally. All the advantages of RPC described in part 1 also apply to XMC multivariable control.
RPC has many notable advantages over traditional proportional-integral-derivative (PID), but perhaps its biggest advantage – because demand for a PID alternative is low, while demand for a multivariable control alternative is high – is in XMC’s multivariable control context, where it brings:
- Responsive, yet stable, performance
- Predictive tapering as variables approach targets to avoid unwanted overshoot or oscillation
- Pre-selected move rates (or “process speed limits”), which are especially important in multivariable control, where multiple critical handles may be moved simultaneously
- Robust feedback control nature, so it takes appropriate action regardless of the source of disturbances or “model mismatch.”
What does “model-less” mean?
Model-less control means feedback control. All process control is essentially either feedback or feedforward. Feedforward control requires models, which are used to make predictions and take pre-emptive action. Feedback responds to ongoing error and must have some sound method of doing so, such as PID or RPC.
So model-based is synonymous with feedforward; model-less is synonymous with feedback. Most control engineers appreciate the potential of feedforward (to reject disturbances seamlessly), but historical experience, as well as modern multivariable experience, indicates feedforward is best used very selectively, as XMC does, rather than wholesale, as MPC does.
Model-less also means adaptive, which means that as process responses change (as they normally do, on both short and long-term bases), the control algorithm automatically compensates. Adaptive control always has been the grail of process control. In the modern era, industry has tried to achieve single-loop adaptive control with auto-tuning, but has been largely unsuccessful (as noted above) and is now trying essentially the same thing on the much more complex multivariable basis, such as adaptive modeling. Notably, RPC holds the only patent, among countless process control patents, with the claim of being inherently adaptive.
And thirdly, model-less control means not model-based. So by using model-less control, model-related activities, including plant testing, model-identification and model maintenance, are all reduced or completely eliminated.
Advanced process control growth
The viability of XMC points the process industry to a new multivariable control paradigm that is more affordable, agile, scalable, and reliable, and better meets the flexible day-to-day operational needs of the modern process industry. It is based on qualitative models, without embedded optimizers, and incorporates traditional feedback and manual control principles. Figure 2 compares today’s model-based multivariable control paradigm with the emergent model-less paradigm.
In operating facilities, multivariable control applications come in all sizes — from a handful of variables to several dozens — so a smaller footprint solution can bring progress on two fronts. It can provide scalable tools for applications that have remained below the radar of the traditional large-footprint paradigm. It can also provide an alternative re-engineering strategy for many of industry’s high-maintenance legacy applications.
To the extent XMC has yet to fully emerge and pass industry muster, the process industry may benefit from pursuing it as a working vision. It should be viewed as a path with promise to overcome the high ownership burden and resource predicament of the existing paradigm, and unlock an agile and sustainable APC solution.
Allan Kern is owner and consultant with APC Performance LLC. Edited by Chris Vavra, production editor, Control Engineering, CFE Media, [email protected].
MORE ANSWERS
Keywords: Model-less multivariable control, XMC, advanced process control
Model-less multivariable control (XMC) is designed to solve advanced control problems without the need for detailed models or online optimizers.
Rate-predictive control (RPC) was designed in conjunction with XMC and shares the same benefits.
XMC’s simpler and scalable approach is better-suited for the modern process industry.
Consider this
Where could XMC help in your industry and what would the specific benefits be?