Industrial organizations rank legacy assets, upfront costs and cultural barriers as the biggest impediments to successfully implementing corporate sustainability initiatives.
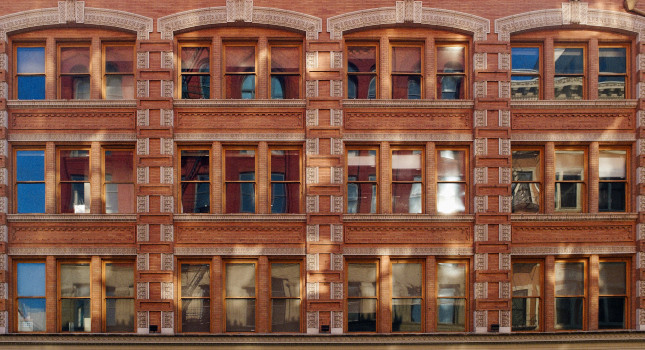
Learning Objectives
- Learn how strategic retrofits can allow manufacturers to sidestep the high upfront costs of ripping and replacing legacy assets and infrastructure.
- Understand how incrementalism can make retrofitting large numbers of assets manageable.
- See about strategies for effectively persuading an organization’s finance department to invest in sustainability retrofits.
Sustainability insights
- 29% of manufacturing leaders consider legacy assets and infrastructure to be a major challenge to meeting their sustainability goals.
- 27% of industrial companies claim that upfront cost or budget is a roadblock to becoming more sustainable.
- One in five organizations ranks culture change as a major challenge to sustainability initiatives, and nearly 80% say C-level individuals should be responsible for driving sustainability efforts.
Nearly six in ten of the world’s top industrial organizations have set carbon-neutrality targets to offset their greenhouse gas (GHG) emissions. Almost half (47%) have embraced RE100 pledges to draw 100% of their energy from renewable sources, while more than one-third (36%) have established science-backed targets to help limit global warming to 1.5-2°C above pre-industrial temperatures.
Goal setting is a worthy first step toward decarbonization. However, implementing programs that deliver upon established goals will be the needed catalyst for change. Unfortunately, research shows that barriers including from infrastructure and culture, stand in the way of deployment and success for industrial companies’ environmental sustainability projects. How organizations navigate those roadblocks will determine if the sector can help protect our planet.
Firms must digitally retrofit legacy assets, infrastructure to optimize energy efficiency
29% of manufacturing leaders consider legacy assets and infrastructure to be a major challenge. This is unsurprising given many buildings, power supplies and processes are decades old and predate the latest sustainability technology and climate science.
Industrial companies often measure infrastructure replacement rates in decades. The IEA considers investment cycles in 25-year spans. The primary reasons for lengthy replacement cycles are cost, inherent asset longevity and the fact that replacing assets is disruptive to operations. While installed systems may not be well-suited to achieving sustainability goals and can be strategically upgraded, ripping and replacing them with new infrastructure will likely cost more, be operationally implausible and leave an even greater carbon footprint than retrofitting.
Consider a more-than-60-year-old manufacturing plant in Lexington, Ky. The plant’s 1960s-era energy infrastructure was wildly inefficient relative to modern standards. However, replacing the plant would have been expensive, required vast volumes of new raw materials and would have required operations to altogether stop. Digitally retrofitting the plant with connected products and predictive analytics to optimize energy costs instead carried the building into the 21st century with less disruption, lower costs and a smaller carbon footprint. Digitizing the older building has led to a 26% energy reduction (GWh), 30% net CO2 reduction, 20% water use reduction and certification by the U.S. Department of Energy as Platinum Superior Energy Performance 50001. This effort has led the World Economic Forum to award this factory its Lighthouse status for efficiency and sustainability.
Other industrial organizations can follow the Lexington plant owner’s lead and digitally retrofit their operations to maximize efficiency while minimizing impact. As the example demonstrates, one way to digitize industrial operations is through implementing intelligent energy management systems (EMS) to monitor and manage energy use. EMS offer real-time insights into energy performance while tracking variables like weather reports and building and site occupancy to automatically regulate the required levels of consumption. In this manner, digital retrofitting ensures organizations only ever use the energy they need.
Given the efficacy and lower-cost footprint of digital energy management and renewable energy systems, it is no wonder that more than half of industrial organizations are predicted to harness these tools within the next three years.
Upfront cost of retrofits can still strain budgets
Though retrofitting existing assets is more cost effective than replacing them, upgrading installed systems doesn’t come cheaply. In fact, 27% of industrial companies claim that upfront cost or budget is a key roadblock to becoming more sustainable.
One way to make the retrofit argument to the finance department is by telling them that sustainability investments may be the most important outlays an organization can make. 60% of consumers now rate sustainability as a key criterion when choosing whom to shop with. Even a majority of investors have turned down agreements on ESG grounds and are likely to scrutinize a business’ sustainability efforts as closely as its financial health.
Fortunately, funding is available to support businesses in their energy transitions. The U.S.’ EPA awards more than $4 billion in grants each year to help organizations achieve their environmental goals. So, rather than ask finance to divert funds away from business-as-usual activities, ask them to invest directly in the company’s bottom line and its future prospects.
Competing priorities and poor data accessibility hamper sustainability initiatives
Nearly one-quarter (23%) and 21% of managers cite competing priorities and lack of access to the right data, respectively, as barriers to sustainability efforts. The best approach given financial roadblocks of this nature may be to start small and expand after a successful pilot project.
The Lexington factory illustrates how incrementalism can still yield sought-after results. Plant owners identified a low-hanging fruit in factory-floor sensors. By digitizing just one set of processes or assets, the owners could measure success and establish a baseline for future projects. This step-based process is easier to manage and, with the data it yields, easier to leverage for additional approvals.
As smaller projects proliferate, manufacturing leaders can then look to bigger-picture centralized, cloud-based optimization and project management technologies to support organization-wide decision-making around environmental action. These investments can directly benefit the bottom line through reductions in energy consumption, particularly during the current global energy crisis, or improvements in process efficiency. In fact, 49% of manufacturing companies expect improved performance and cost savings when investing in sustainability. An incremental approach offers manufacturers a valuable multi-tool against sustainability challenges, many of which stem from up-front costs or lack of proof-point data.
Sustainable operations require sustainable culture
One in five organizations ranks culture change as a major challenge to sustainability initiatives, and nearly 80% say C-level individuals should be responsible for driving sustainability efforts. In large companies, inertia is difficult to overcome, especially if the results are positive. But leadership must shoulder the burden of driving culture change and seek buy-in across the business.
Many companies are addressing culture requirements by appointing a chief sustainability officer (CSO). Demand for CSOs has grown 228% in corporate America over the last decade, highlighting the emphasis on keeping businesses accountable for their environmental impacts.
To successfully lead sustainability-forward culture change, executives in CSO or similar roles must consider sustainability to be ingrained in day-to-day operational decisions and long-term strategy, rather than just another metric to report. Then, the success of initiatives will depend on how well cultures warm up to the idea of implementing the technologies and solutions to achieve those aims. Here, it’s often worth hiring a team of expert sustainability consultants to help the organization break down silos, comply with net-zero regulations and craft a long-term strategy.
Focus on the benefits of sustainability practices to drive positive change
Just 10% of businesses cite a lack of identified benefits as a major challenge to becoming more sustainable. This finding suggests that most organizational leaders can articulate the advantages of sustainability projects internally. Despite this fact, industrial businesses must use data to incrementally review, rather than expect an instant impact on, existing processes, equipment, organizational culture and technology to identify and tackle inefficiencies and waste. Focusing on the return on value (ROV) of initiatives rather than just the return on investment (ROI) can further hammer home the idea that an incremental approach can be successful.
The manufacturing sector is still at the start of its sustainability journey. But a long-term commitment to sustainability is essential if we are going to secure the future of our manufacturing, and our planet.
Gregory Tink, digital transformation consulting director, Schneider Electric. Edited by David Miller, content manager, Control Engineering, CFE Media and Technology, [email protected].
MORE ANSWERS
Keywords: Sustainability, retrofit
CONSIDER THIS
What incremental changes can you make at your organization to begin moving it in a more sustainable direction?