5G technologies are in three parts; even in the first, it’s possible to communicate with industrial communications protocols. A fieldbus protocol can be used for industrial 5G, over the 5G R15 enhanced mobile broadband (eMBB).
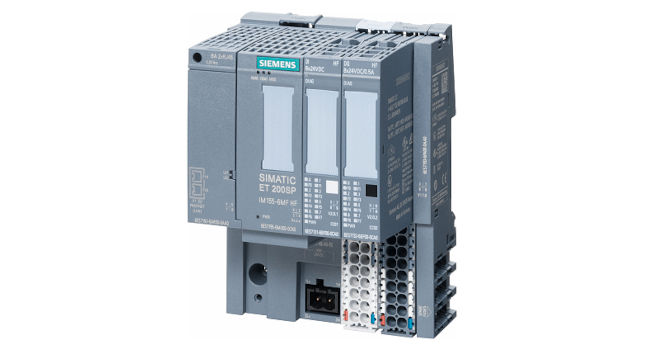
Learning Objectives
- Learn how first of the three parts of 5G can transmit layer 2 fieldbus information.
- Understand limits of 5G for industrial using R15.
- See advantages of embedding 5G layer 2 communications in layer 3 packets.
Industrial 5G deployments, such as 5G for smart factories and 5G for steelmaking, have used commercial 5G, which is very different from industrial 5G technologies. Three 5G applications are enhanced mobile broadband (eMBB), ultra-reliable low-latency communication (URLLC) and massive machine communication (mMTC). Each 5G protocol serves a different domain. eMBB is bandwidth-oriented such as HD video. URLLC supports the requirements of Industrial Internet of Things (IIoT) applications. mMTC is used for applications that require low power consumption and have a large number of connected devices.
One wireless network cannot fully support the three application scenarios at the same time, and the development of 5G wireless technology is evolving. The 5G standard adopted a step-by-step development. The first complete set of 5G standards, version R15, was frozen in 2018, which mainly provides for eMBB and aims to increase bandwidth.
The 5G base stations and 5G cell phones deployed by major operators are now based on this version. The R16 version, frozen in July 2020, specified URLLC and mMTC.
Limits to 5G for industrial using R15
For industrial wireless networks, eMBB does not fit the bill because industrial real-time protocols (such as Profinet IO) rely on the low latency and high reliability in the URLLC part of the 5G standard, available in version R16. Available 5G technologies, at present, use the R15 version. Can industrial real-time protocols be transmitted through the R15 version of 5G to achieve low latency and high reliability?
The R15 version of the infrastructure cannot transmit Layer 2 communications based on the OSI model and only supports the layer above, Layer 3 with packets (TCP and UDP), which allows R15 5G to transmit OPC UA or message queuing telemetry transport (MQTT) protocols. Widely-used industrial fieldbuses cannot be transmitted via 5G R15, because they require a Layer 2 connection, only supported by the R16 version of the 5G standard.
Embedding 5G layer 2 communications in layer 3 packets
Siemens Profinet IO can be used in the R15 version of 5G networks by using a transport technology. The VXLAN (virtual extensible local area network) is a protocol that embeds logical Layer 2 communication in Layer 3 packets. Doing so enables transparent transmissions of Layer 2 protocols across network boundaries, enabling real-time 5G Profinet communication among controllers and distributed I/O devices.
The approach expands applications for 5G. For example, multiple automated guided vehicles (AGVs) can be controlled with one Siemens S7-1500 controller. Profinet I/O is used as the protocol between the S7-1500 and the Siemens ET 200SP distributed I/O devices on the AGVs. The core of the communication is a dedicated R15 5G infrastructure connected to Siemens’ MUM856-1 5G router. By using a central controller and Profinet I/O communication, distributed I/O devices can be used on the AGV without a local controller, saving space and cost.
Prior to 5G R16 commercialization, use of 5G over R15 makes full use of the high-speed, high-bandwidth and high-reliability features of 5G. Ensuring real-time communications meets industrial communication network requirements.
Stone Shi is executive editor-in-chief, Control Engineering China. Edited by Mark T. Hoske, content manager, Control Engineering, CFE Media and Technology, [email protected].
KEYWORDS: Industrial 5G, wireless 5G fieldbus
CONSIDER THIS
Are you gaining industrial 5G wireless advantages?