There are challenges facing engineers, especially when it comes to ensuring consistent performance and reliability of industrial ethernet connectivity in harsh industrial environments.
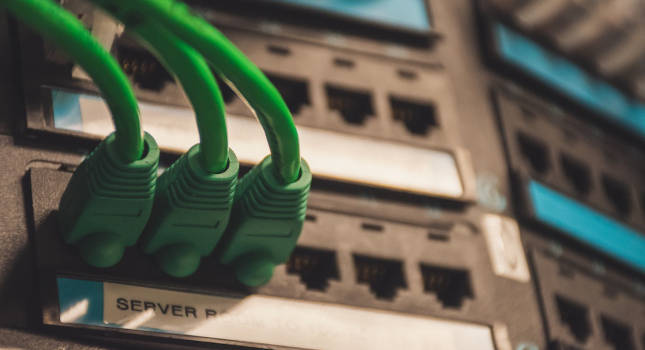
Ethernet insights
- Industrial environments require best practices like using shielded cabling, proper grounding and maintaining line of sight to mitigate issues from EMI and RFI when deploying Ethernet, wireless, and 5G technologies.
- Ensuring network reliability and performance involves using industrial-grade components with high IP ratings, and EtherCAT technology offers advantages like short cycle times, reduced bandwidth requirements and superior diagnostics for consistent performance.
- Beyond physical infrastructure, protocols like OPC UA provide resilience against cyber threats and enable cross-vendor interoperability, essential for high network reliability and performance in industrial settings.
Industrial environments can present a variety of challenges when it comes to maintaining the reliability and performance of networks. However, there are best practices to ensure a facility can take advantage of industrial ethernet, wireless and 5G technologies, while mitigating any issues related to electromagnetic interference (EMI) and radio frequency interference (RFI).
Plants today are full of EMI — emanating from technology such as servo and variable frequency drives, power supplies and welding robots. Plant and process startups can also lead to power surges that can disrupt normal device operations. There is also often a fair amount of metal in manufacturing environments — both structurally and from material inputs — which can make wireless communications difficult.
“The EtherNet/IP industrial ethernet network supports wireless communications, including 5G, as a media independent network since it relies on the common industrial protocol (CIP) at the application layer,” explained Steven Fales, Director of Marketing at ODVA, the international standards organization that manages Ethernet/IP and CIP technology. “However, RFI from Wi-Fi, 5G and other wireless communications in plants can be a concern. The first mitigation tactic that can help is to specify and install cabling that is shielded to limit the effects of EMI/RFI and which utilizes twisted pairs to reduce cross talk, interference from nearby wires and cut down on EMI/RFI interference.” Steven went on to explain that properly grounding and bonding, through the use of low impedance pathways like braided straps to connect to grounding (earthing) points, is a good way to make sure that stray current does not interfere with the communication or operation of a device. “Ensuring that line of sight is maintained for wireless communications to avoid interference is another best practice,” he added. “Additionally, having repeaters available for wireless networks can help maintain proper network performance if there is too much EMI and/or RFI in the area.”
Another common issue that needs to be dealt with in industrial environments is liquid from the environment, equipment and production processes. Washdown procedures using caustic liquids to maintain hygienic cleanliness are common in food and beverage facilities, for example. “Dust build-up over time can also hinder the proper operation of electronic devices. Specifying cabling and devices with Ingress Protection (IP) ratings of IP65 or higher can help to make sure that dust and liquid exposure doesn’t result in critical issues,” Fales said. IP69K ratings are recommended in cases where electronic devices are regularly exposed to high temperature and high pressure washdowns.
EtherNet/IP supports IP65 and higher connectors, shielded cabling and devices. It is important to note that cabinets can offer good protection for electronics. However, the high cost of stainless-steel cabinets makes locating devices closer to equipment with higher IP ratings a good alternative. “Specifying electronic devices with IP65 or higher ratings in industrial environments is also recommended, even when liquid ingression isn’t anticipated, in case of spills such as hydraulic fluid or roof leaks,” continued Steven
Another problem area in industrial environments can arise from wires being accidentally unplugged or settings being inadvertently changed on devices. The use of threaded M8 and M12 connectors can help ensure that cables don’t become disconnected from vibration or accidents.
EtherCAT
When it comes to the challenges ensuring consistent performance and reliability of industrial ethernet systems in harsh environments, the first thing that comes to mind is physical stability, according to Martin Rostan, Executive Director at EtherCAT Technology Group.
Martin argued that, while electromagnetic interference can impair data connections, there is no difference between real-time industrial ethernet technologies in this respect. “They all rely on fast-ethernet (100BASE-TX) as the physical layer — and therefore the same basic rules for industrial data cabling apply to all of them,” he said. “Use shielded cables with appropriate cross-sections for the cable length, use decent connectors that reliably connect the shield to the devices, ensure proper earthing and so on. The same installation basics also apply to gigabit ethernet, although even more care must be taken here because the signal-to-noise ratio is significantly better with 100 Mbit/sec ethernet than with gigabit.”
Rostan went on to explain that consistent performance and reliability depends not only on the cabling, but also on the protocol and its implementation, and this is where the various industrial ethernet solutions differ considerably.
“Anyone who uses switch-based technology knows the challenges of using switches,” he said. “Switches are not made for deterministic real-time communication, but instead follow the ‘best effort’ approach. With careful configuration and appropriate IT know-how — in small systems even with switches — certain real-time properties can be realized, but only up to certain limits in terms of cycle time. And these limits are easily overcome by the CPU performance of modern PLCs, such as PC-based controls. Gone are the days when controllers operated with a cycle time of 5-10 ms.
“EtherCAT requires no switches and guarantees short cycle times even in large networks, thanks to its functional principle. Instead of using individual Ethernet frames for each node, which have to pass through switches, etherCAT sends a single frame through the network, from which all nodes take their output data and into which they insert their input data.”
This “processing on-the-fly” takes place in special etherCAT chips, which are available from many manufacturers. This, argues Martin means that etherCAT is not a ‘best effort’ approach, but instead is a reliable hardware-based data exchange. Neither switches nor the CPU performance of the distributed devices or the efficiency of the protocol software implementation affect performance. The etherCAT chips also have diagnostic properties that are said to be superior to those of conventional Ethernet devices. “Bit errors are not only detected but also precisely localised, and even loose connectors or beginning cable breakages in moving cables can be localized,” Rostan said.
Because etherCAT requires less bandwidth than other industrial ethernet technologies, the probability of disturbance due to noise is said to be lower for the same cycle time. “And those who use etherCAT performance for shorter cycle times benefit from significantly faster recovery times if a disturbance does occur,“ Rostan said.
Looking past the physical infrastructure
High levels of network reliability and performance are required in most industrial applications in order to prevent production downtime and safety hazards.
The physical basis for this is formed by an industrial ethernet infrastructure with networking components designed and rated specifically for use in a particular industrial environment — including harsh and hazardous conditions.
Active and passive network components need to be able to withstand a wide variety of environmental factors, such as high temperatures, humidity, dust, vibration, and electromagnetic interference. In addition, all network components need to be dimensioned in a way that sufficient network performance is available to prevent network congestion, packet loss or unacceptable latencies or jitter.
However, Peter Lutz, Director Field Level Communications at the OPC Foundation, warned that exclusive focus on the physical infrastructure would be short-sighted because the respectively used industrial ethernet protocols have a significant impact on the overall performance and reliability of the network. “These protocols need to provide resilience against cyber threats such as malware, hacking, and unauthorized access. And not least, standardized protocols are a prerequisite to ensure cross-vendor interoperability across the diverse industrial devices and systems,” he said.
The OPC UA (IEC 62541) framework offers a complete, open, standardized and interoperable solution which is scalable from the field to the cloud. OPC UA is fundamentally transport-agnostic so can be combined with different underlying transport protocols and physical media depending on the application-specific requirements and use cases, including the ethernet advanced physical layer (ethernet-APL), ethernet time-sensitive networking (TSN) and industrial 5G for field-level communications. At the same time, OPC UA can be mapped to MQTT with either JSON or binary encoding to achieve cloud connectivity.
“However, OPC UA is more than just a standard for data exchange,” Lutz said. “The architecture not only has the ability to transport machine data, but also to describe it semantically in a machine-readable way and combine both with a multilayer security concept including authentication, authorization as well as encryption. Safety-related data can be exchanged via OPC UA Safety which specifies a safety communication layer (SCL) and fulfills the requirements of the international specifications IEC 61508 and IEC 61784-3.
“Cross-vendor interoperability between controllers and field-devices is enabled by the OPC UA (Field eXchange) specification extensions that standardize the information models for different application areas in factory automation and the process industry, such as motion control, instrumentation and I/O,“ Lutz said.