Industrial communications networks and control engineering are evolving to improve operations and industrial Ethernet is playing a key role.
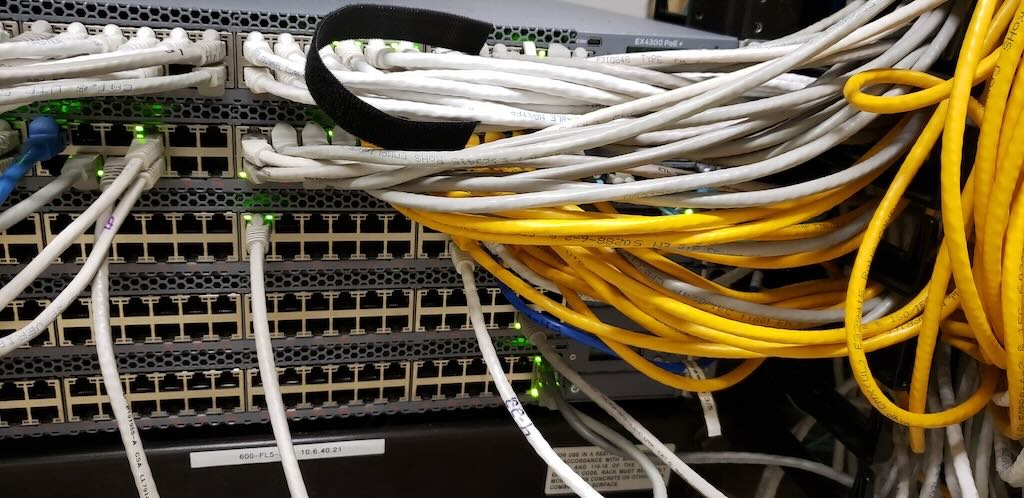
Learning Objectives
- Understand how industrial networking and control engineering have been shaping each other’s evolution since the beginning.
- Learn how industrial Ethernet has grown and is often used in supporting smart manufacturing applications.
- Learn how industrial Ethernet’s capabilities are being advanced to address current needs, particularly with digital transformation.
Industrial Ethernet insights
- From RS-232 to time-sensitive networking (TSN), Ethernet has evolved for higher speed, accuracy and vendor neutrality and enabling complex and interoperable industrial Internet of Things (IIoT) setups.
- Trends such as wireless communication, single-pair Ethernet (SPE) and power over Ethernet (PoE) hint at further evolution and adapting to unforeseen user requirements and applications.
Network technologies and their application in industrial automation have been evolving and adapting since their inception. As a result, they have helped address the ambitious control engineering needs with value-adding standards, protocols and innovations. They have expanded the scope of what is possible with innovative opportunities in control engineering manifesting after the adoption of new solutions from the industrial networking industry.
How industrial communications have evolved
At the dawn of the third industrial revolution, more than 50 years ago, the transition from analog to digital electronic technology was supported by the first communication standards. For example, the RS-232 serial communication standard provided point-to-point data transmission between two devices. As forward-thinking industrial players embraced this transition, they began grappling with the pressing issue of enabling shop floor devices to send signals over distance and communicate with each other.
Answering these demands, less than three decades later, a significant transformation occurred with the introduction of controller area network (CAN) systems and fieldbus. These technologies ushered in an era of more complex and interconnected communications, which led to the rise of industrial Ethernet.
Thanks to its ubiquitous nature, industrial Ethernet enabled a greater number of sensors, control devices and network nodes to share large volumes of data at high speeds. It also offered potential gains in terms of efficiency, flexibility, remote access, diagnostics and faster networking. Thanks to these key opportunities, industrial Ethernet emerged as the foundational transport technology in almost every industrial application. In 2018, it overtook traditional fieldbuses in terms of the number of newly installed nodes in factory automation
Industrial Ethernet, communications pushing forward
The evolution of industrial communication technologies and industrial Ethernet did not stop there. As companies had been empowered to create more digital and ambitious automated setups through industrial Ethernet, they continued to advance their shop floors, leading to the rise of new demands. These included the ability to accommodate an ever-growing number of devices on a network, handle increasing data traffic at higher speed, improved accuracy and precision and facilitate data sharing among different vendors.
To meet these growing demands, industrial Ethernet has evolved, improving its performance and incorporating innovative functionalities. While 10 Mbps used to be sufficient to satisfy network speed and bandwidth needs, it quickly became obsolete for most applications, with automation vendors, specialists and users adopting 100 Mbps and even reaching 1 Gbps. This increased bandwidth was fundamental in supporting the development of more competitive products for evermore data-driven operations.
Another significant trend has been the shift towards open, vendor-neutral network technologies. Proprietary solutions had historically been the norm. Users who adopted these found themselves locked into a single vendor’s ecosystem, making it challenging to integrate devices from different manufacturers and limiting their capabilities.
More interoperable alternatives that give system integrators and end-users the flexibility to select automation products that suit specific requirements and intended applications have grown in popularity as a result. Equipment vendors also benefited from this transition because they can support compatibility with a broader range of devices and establish synergistic collaborations.
As the needs of control engineering and industrial automation continue to evolve, so does Ethernet technology, with a clear trajectory towards greater speed, accuracy, interoperability, and adaptability for successful industrial Internet of Things (IIoT) frameworks. As companies strive to implement smarter digital manufacturing practices, further adaptations and advances in network technologies for control engineering have become necessary.
This vision of highly-interconnected IIoT setups is achievable through time-sensitive networking (TSN), the latest extension to Ethernet’s capabilities, as defined by IEEE 802.1 specifications. It provides accurate, distributed time synchronization, as per IEEE 802.1 AS standards, as well as data traffic prioritization, scheduling, and queuing functionalities according to IEEE 802.1 Qbv.
These capabilities enable network infrastructures to support even the most demanding, high-speed applications, ensuring deterministic communications while offering a solid, reliable platform for broad interconnectivity. These features facilitate the creation of unified IIoT environments where any type of data can be shared, irrespective of their original domain, to support automation and effective, data-driven decision making.
Recent developments such as the establishment of the TSN Industrial Automation Conformance Collaboration (TIACC), have been promoting vendor-neutral, industry-wide conformance. This, along with other initiatives, are addressing the market’s demand for the coexistence of different protocols within the same network, fostering collaboration among vendors to validate their TSN-compatible solutions for greater interoperability.
The road towards complete interconnectivity
While industrial Ethernet and industrial networking, in general, have come a long way, it would be naïve to assume they have reached the end of their evolutionary journey. The next generation of ambitions and innovations is already emerging, with trends such as wireless communications connecting shop floors, enterprises, and entire supply chains. Other trends point towards simplified networking requirements, as advocated by single-pair Ethernet (SPE) and Power over Ethernet (PoE) proponents.
There is always room for unexpected developments, though. New user requirements and applications may not manifest until after the digital transformation of businesses matures.
This will benefit automation specialists, machine builders and end-users alike. It will drive the further development of control engineering and industrial networking. The future of industrial networking promises to be even more exciting as it adapts to new challenges and innovations.
Thomas Burke is global strategic advisor for the CC-Link Partner Association (CLPA), a CFE Media and Technology content partner. Edited by Chris Vavra, web content manager, CFE Media and Technology, [email protected].
MORE ANSWERS
Keywords: industrial Ethernet, industrial communications
ONLINE
See additional Ethernet stories at https://www.controleng.com/industrial-networking/ethernet/
CONSIDER THIS
How has industrial Ethernet evolved communications at your facility?