Effective data acquisition technology that can effectively provide data crunching and processing will be critical for future smart factories.
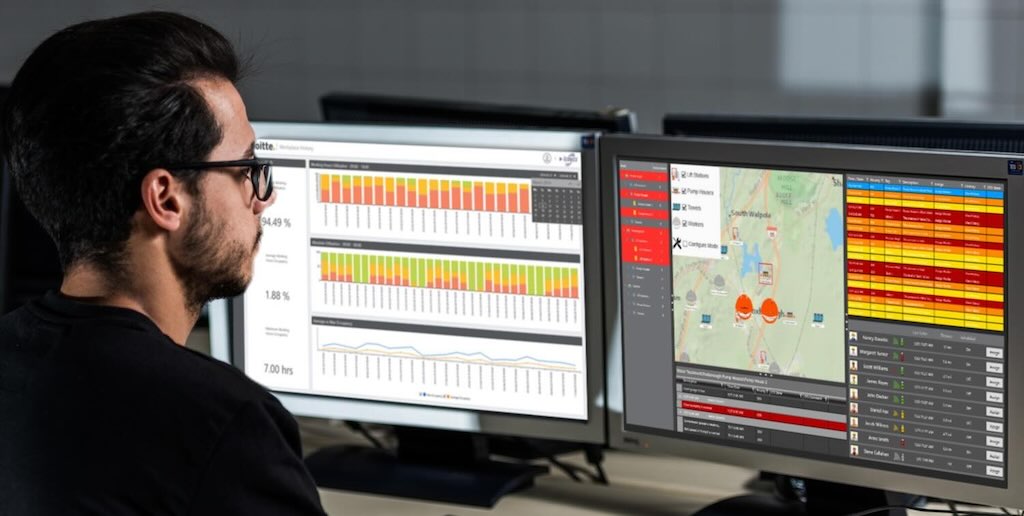
Learning Objectives
- Effective data acquisition is at the core of smart manufacturing applications.
- Understand the fundamental role of communications in supporting data acquisition strategies.
- Learn how the latest network technologies can advance data acquisition and digital manufacturing frameworks.
Data acquisition insights
- When it comes to offering value-adding industrial automation and control engineering solutions, staying ahead of the curve is a necessity for automation specialists, machine builders and system integrators.
- In line with smart manufacturing trends, one key aspect of this is enhancing and ensuring the data acquisition capabilities of systems.
Data acquisition, the process of collecting data from various sensors and devices to support analysis, visualization and storage, is a given in modern automation systems. This process has traditionally been focused on basic measurements and control, for example to run motion or safety applications.
Now, factories require the use and transmission of meaningful data to become smarter and interconnected, which makes strong data acquisition a must-have.
In particular, next-level data acquisition solutions can help companies to leverage a wealth of information and insights. With access to real-time data from a variety of sources, companies can generate an accurate, in-depth understanding of their operations and equipment. This has the potential to lead to ground-breaking human-machine collaborations that increase efficiency, reduce downtime and cost savings. This helps businesses make more informed decisions to optimize processes and address issues before they arise.
For example, it is possible to set up effective condition monitoring and predictive maintenance strategies. By continuously tracking the status of machines and their components, engineers can predict when servicing, repairs or other related activities are needed.
As a result, more effective maintenance schedules can be created and planned shutdowns can be mapped out, preventing costly breakdowns, minimizing downtime and cost while maximizing component and equipment service life.
Improvements in control/quality assurance and inspection also are within reach by applying the same principles, with analyzers and vision systems monitoring quality attributes and processing conditions. This makes it possible to reduce defects, waste and help streamline production times.
When looking at current supervisory control and data acquisition (SCADA) software offerings, these trends and opportunities are showcased by more powerful platforms and better interfaces. Intelligent alarms, intuitive and comprehensive visualizations covering various aspects within shop floors, automated feedback and feedforward control are among the most common functions now available.
Communications solutions for advanced data acquisition
It is critical to generate and share information, preferably in real-time, for companies to realize the potential of advanced data acquisition solutions. The combination of these factors makes it possible to support analytics and mining operations to interpret the data, generate knowledge and gain valuable insights.
Suitable communications solutions and network technologies are a must to gather data from every corner of industrial operations, establishing broad interconnectivity across devices, machines, production lines, shop floors and entire enterprises.
There also is a growing need for industrial Internet of Things (IIoT) frameworks, where sensors, actuators, machines and software platforms are all integrated into a single network. When it comes to industrial automation devices, SCADA platforms and network technologies, automation specialists, machine builders and system integrators should favor solutions that can support high-speed transfers of large volumes of data from different sources.
This means selecting technologies with a number of key features. It is important to specify automation products using protocols with large bandwidth, such as 1 Gbps. This capability accommodates the ever-increasing flow of data streams that characterize smart manufacturing applications.
Selecting systems and components compatible with a network technology that leverages time-sensitive networking (TSN) can be beneficial because they can help to support current needs while helping future-proof key applications.
TSN benefits for data convergence, performance
In effect, TSN extends the capabilities of standard industrial Ethernet to deliver deterministic performance and data convergence. It offers these two value-adding elements by elevating synchronization accuracy among all nodes on a network as well as enabling the transfer of different types of traffic on a single network.
Thanks to the IEEE 802.1 AS standard, TSN can address standard Ethernet legacy issues such as latency, jitter and fault tolerance. IEEE 802.1 Qbv ensures time-critical messages for control operations can be prioritized and transmitted seamlessly, without delays or congestion, alongside less transient information such as general-purpose transmission control protocol/internet protocol (TCP/IP) traffic. With this technology, it is possible to create convergent IIoT environments where any type of data can be shared, independent of their type or original domain, to generate valuable business knowledge.
Opening the doors to interoperability
Another aspect to consider is openness and vendor neutrality. Industrial automation devices and platforms using supplier-specific communications solutions are often limiting and misaligned with the needs of the smart, connected factories of the future. More interoperable alternatives such as using open network protocols can help give improve flexibility and scalability because they can interact with a wider range of devices and systems from multiple providers.
This helps empower system integrators and end users to use the products best suited to address their specific requirements and intended applications. They also enable industrial automation vendors to offer compatibility with a broader range of devices and, in some instances, establish synergistic collaborations with other industry players.
Data acquisition’s future role
Data acquisition is a must in the era of digital manufacturing, especially in North America, which is expected to account for the largest SCADA market worldwide. When setting up data-driven systems, effective network technologies are the backbone of ambitious and value-adding strategies, empowering manufacturers to harness the full potential of data-driven decision-making.
Going forward, embracing industrial automation hardware and software components that leverage a solution that combines gigabit bandwidth, TSN and openness will be crucial for staying competitive and efficient. Adopting this type of technology will help companies make their data acquisition strategies more effective and smart.
Thomas Burke is global strategic advisor for the CC-Link Partner Association (CLPA). Edited by Chris Vavra, web content manager, CFE Media and Technology, [email protected].
MORE ANSWERS
Keywords: data acquisition, smart factoryÂ
ONLINE
See additional data acquisition stories at https://www.controleng.com/process-instrumentation-sensors/data-acquisition-daq/
CONSIDER THIS
What are your considerations and priorities for choosing data acquisition tools for your facility?