Demands on system-integrated measurement technology continue to grow, which makes a strong case to integrate test tech and controls engineering in production.
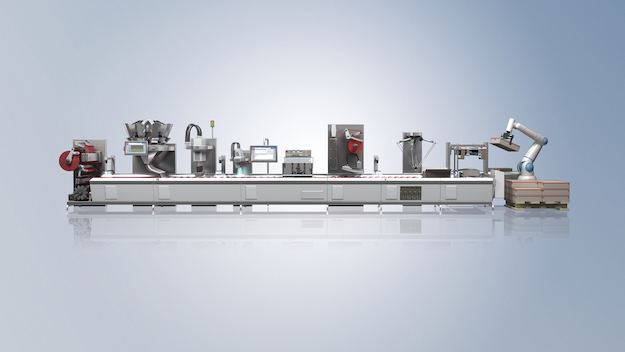
Learning Objectives
- Realize how advances in industrial automation fill the need for high-end data acquisition and testing tools.
- Understand the advantages of a consolidated engineering approach for production and test and measurement.
- Identify potential hurdles of this integrated approach and strategies to overcome them.
System integrated DAQ insights:
- Distributed data acquisition (DAQ) systems networked via EtherCAT simplify architectures and reduce costs by reducing latencies with local signal processing.
- Combining industrial automation with test and measurement technologies introduces flexible hardware selection for purpose-built remote panels.
- An integrated approach allows engineers to time synchronize system events for functional design, root-cause analysis and general troubleshooting by production technicians.
In an early project, there was a scene of man vs. machine that could have come straight from an old science fiction novel where a company was revamping its manufacturing and test systems, combining both onto an end-to-end software and hardware platform.
The idea was to simplify implementation, operation, maintenance and overall data acquisition (DAQ) capabilities on the test and measurement side. It was working beautifully. For the customer, however, it wasn’t enough to take our word for it. Even reviewing real performance data showing this was a better approach didn’t move the needle.
They pitted their best employee with the legacy equipment against the new production and test line. The two had to race to see which could manufacture the product and put it through the necessary tests as fast as possible and with the highest quality. The outcome was predictable. The machine far outperformed the hapless hero.
In this case, there was a better solution available for a combined production and test system and the data backed it up. However, it still took some spectacle to make the client accept the reality of the situation.
In some ways, this is the story of automation in general, which frees up operators to perform more valuable, rewarding work at the same time as it boosts machine performance. More specifically, it’s the story of combining siloed DAQ technologies with powerful, modular and standardized industrial automation solutions.
The tides of automation are always shifting. In recent years, there are more requirements for more powerful, flexible technologies as companies come to grips with various impactful global events. That’s on top of tech trends that have been building for a long time. For example, machines are becoming more sophisticated to adopt Industry 4.0 concepts. Overall production demands also have pushed companies to fundamentally rethink the approach to automated manufacturing.
Through this, hardware and software capabilities have risen to the new challenges, such as:
-
Larger sets of time-stamped measurement data
-
Insights into machine operation through advanced condition monitoring
-
In-line testing applications to aid in optimizations of automated solutions.
The case for consolidation is getting stronger. However, this begs the question: What tools and technologies enable engineers accomplish the goal of integrating “black box” DAQ and robust industrial automation solutions?
Speaking the same language and collaborating on code
The heightened adoption of open and flexible industrial protocols has helped redefine what’s possible for in-line test systems. Today’s engineers can tackle modern challenges that require multiple communication interfaces and subsystems, high determinism and synchronization over a variety of scaled applications. In these cases, the EtherCAT industrial Ethernet system has been a game changer.
Furthermore, the emerging interfaces for centralized and decentralized measurement interfaces coupled with devices for synchronization from local to external solve a broad spectrum of problems when test and production automation are disjointed. These advances fulfill almost all technical needs of any engineering team to settle on a common platform and harmonize efforts — from standalone test stands to fully integrated and automated testing.
Along with the expansion of the test engineer’s toolbox with familiar standards, there also is a need for additional software interfaces to existing tools. Engineers can pull in legacy code from various platforms such as MATLAB/Simulink, LabVIEW and VeriStand. As a result, hardware-in-the-loop (HiL), model-in-the-loop (MiL), and software-in-the-loop (SiL) simulations can accelerate system development.
Breaking down the automation and DAQ silos
With the need for integrated test and measurement solutions established and fulfilled, the challenge then becomes building a business case to justify this kind of engineering transformation. It’s important to consider the benefits and drawbacks of how this is achieved as well as how to overcome common challenges.
This combined approach excels in these ways:
-
Maximized existing plant space. Condense machines that may have similar functions into a single platform. This saves valuable floorspace at a time when industrial real estate costs remain sky-high.
-
Simplified workflows for sensor data. Move data through the signal and analysis tools, which are integrated into a comprehensive automation platform alongside other system functions.
-
Fast and flexible communication via EtherCAT. Remove additional latencies and temporal challenges in the system by harnessing real-time communication protocols and processing them on the same controls system.
-
Greatly reduced system complexity. Simplify cabling solutions by distributing DAQ systems closer to quantities of interest, and eliminate additional networking components, such as managed switches, through EtherCAT use of EtherCAT.
-
Increased test bench modularity. Piggyback on modular approaches used in industrial automation with all-encompassing control to create modular test bench system designs.
-
Streamlined test systems adjustments. Remove the difficulty of making system changes in separate production and test systems. Compartmentalized systems can make it difficult to perform system changes or service, especially when a single engineering group “owns” the system. A fully integrated approach eliminates those unnecessary delays to ensure requests are completed quickly.
-
Testing only high-quality products. Enable early detection of loss of product integrity through integrated test and measurement technologies. So the production line can eject product that’s not up to standards before further processing is performed. This not only cuts useless processing times, but it also can reduce waste material and other costs by giving insights into where manufacturing defects and inefficiencies may be occurring.
This approach does have some drawbacks, however, including:
-
Disagreement on programming standards. In a siloed test, controls and software engineers often use varying engineering principles. Bridging this gap may require settling on programming languages between multiple engineering groups. Generally, open interfaces should facilitate each group’s desired flavor of code implementation.
-
Inability (or unwillingness) to consolidate tools. This approach introduces the potential of each group adding more tools to satisfy all system requirements. To overcome this, try creating an internal standard framework that is modular and can be tested, and implement standard hardware interfaces to simplify integration.
-
Intensive planning among all stakeholders. To get to the technical benefits, you’ll need to undertake a strategic design effort to capture all requirements between the general manufacturing functions and test functions of machines and lines. Develop a rollout plan to approach the conversation between teams. Try starting with small, one-off applications, then grow into a combined effort.
In the end, the scale tips in favor of the joint engineering effort. The ability to utilize the strengths of both teams and distribute test automation throughout the production process far outweighs any downsides.
Pass the test with integrated automation
Demands on automated machines continue to pile on at a quickening pace. Beyond working faster, collecting more data, and flexibly adapting to new products or processes, industrial machinery must deliver even greater product quality with less waste. Now, these trends in automation technology have begun to flow into the test and measurement world.
An integrated approach to industrial automation and DAQ technologies gives companies the ability to further improve processes and remain competitive. Whether building complete production lines or standalone systems, leveraging industrial solutions that have evolved to incorporate core measurement and data functionality can help companies pass a rather difficult test.
Alec Abkemeier is software product manager – test & measurement, Beckhoff Automation LLC. Edited by Chris Vavra, senior editor, Control Engineering, WTWH Media LLC, [email protected].
MORE ANSWERS
Keywords: data acquisition
CONSIDER THIS
How do you use data acquisition to make the most out of your facility’s operations?