Digital twins enable components and machines to be rapidly developed virtually, before any hardware is produced, enabling earlier integration.
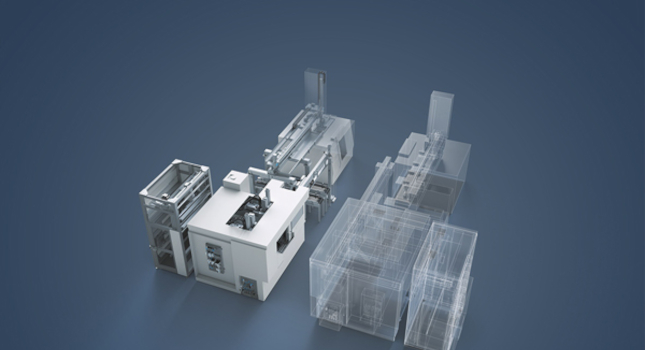
Digital twin insights
-
Digital twins are increasingly being used to precisely replicate the capabilities of their components: if necessary, down to their physical behavior. This allows project development timelines to be drastically shortened.
-
Digital twins represent a massive reduction in the need to search for information in catalogues or on support portals and in the time needed for preparing machine documentation.
-
Condition monitoring can also be used in conjunction with the simulation models of the digital twins to create predictive maintenance plans.
To increase productivity, machine builders need to achieve faster machine builds as well as more efficient engineering processes with fewer mistakes or unforeseen issues in the later stages of the build. One way to achieve this is to employ a digital first strategy.
To shorten machinery development times, more simultaneous engineering is needed. Digital twins are increasingly being used to precisely replicate the capabilities of their components: if necessary, down to their physical behavior. This significantly shortens project timelines and increases productivity. Critically it means machine developers can simulate, evaluate and make adjustments to their software before any metal has been cut or assembly started. They can, for example, design and optimize programs for more efficient handling systems using virtual models. Errors can be detected and corrected at an early stage, contributing to more efficient and stable operations later.
Digital twins of automation components are much more than just 3D models. They are digital representations that provide all kinds of information, including a clear description of their capabilities, their documentation and behavior, such as the simulation of their kinematics and kinetics and the communication with them, including the role they play in the machine. They are constructed within a standardized template using sub-models such as digital name plate, contact information, technical data, CAD models etc.
Lifecycle data
Industry 4.0 machine architecture is based entirely on digital twins. Thanks to their standardized communication interfaces, they make life easier throughout the entire lifecycle of a machine – from virtual commissioning and control of the machine to data acquisition and value-added services such as maintenance or diagnostics.
In the past there has been a multitude of data sources for each automation part in different formats, from CAD and PDF drawings to paper manuals and operating instructions. Data management was often cumbersome and difficult to access throughout the entire lifecycle of an automation product. Different functional roles within a project team would require different perspectives on the data. The information has often been gathered independently by the different functions and rarely carried across without re-entering the data. This is repetitive, error inducing and is a time-consuming task. This lack of digital continuity also made it difficult to fully network all objects.
Digital twins represent a massive reduction in the need to search for information in catalogues or on support portals and in the time needed for preparing machine documentation. Their administration shell is used as a central source of information, enabling them to be used throughout a component’s service life.
Of course, the quality and depth of information may still vary between suppliers. However, the use of standardized formats enables far more rapid identification, assimilation and transfer of information. The standardized Asset Administration Shell digital format enables it to be fully machine readable. This is an extension way beyond catalogue information: it enables ‘intelligent algorithms’ to be used to configure and optimize designs.
Digital twins can also be a factor in the drive for increased sustainability by enabling the simulation and optimization of designs for energy-efficiency components; both in terms of the manufacturing environmental footprint and their energy consumption within the specific application. It is superficial to think in terms of one drive technology being less or more energy efficient than another. Instead, the application needs to be considered, including cycle rates, holding times, so the best option can be selected based on the calculated outcomes.
Even before machinery manufacturers fully implement their use of digital twins they can benefit in many smaller ways from the technology. For example, traditional printed product labels can only have limited information on them, particularly as products become more compact. Standards and Directives specify information that must be included and for products being sold globally there are many conformity marks that need to be applied onto extremely small labels. This makes it difficult to find and read all the necessary information. The solution is the digital name plate. It supplies all the relevant information including certificates, documentation and operating instructions, as well as comprehensive catalogue information, in digital format. Digital name plates can therefore save time and can supply the latest and updated information, which is available globally, 24/7, in the local language.
Simulation and emulation
A virtual model also allows the developer to test – for example, a handling system – and view the operating data from the motor displacement encoder or the signals from end position sensors. The developer can then create the machine control sequences using the components’ functions such as extend, rotate, or grip.
Other value-added services based on digital twins include the condition monitoring function, which can generate messages predicting when running components are approaching the end of their design service life. The machine’s digital twin could then automatically trigger the requirement to order spare parts. If there are newer models for the components being replaced, the customer can use the virtual environment to first test how the new components interact before ordering them.
Condition monitoring can also be used in conjunction with the simulation models of the digital twins to create predictive maintenance plans. Standard operating performance data can be read from the components and anomalies detected using AI systems. However, rather than just being a difficult to interpret trigger it can be related to the component and what corrective actions may be needed. For example, a simple cleaning of an optical lens, the service of a bearing or the complete swap out of a part predicted to fail within a defined time. Customers can also use their digital twins to develop and evaluate subsequent changes, optimizations, or reconfigurations on the virtual model before these are implemented on the machine, which speeds up the process.
Digital twin technology has a bright future. It’s inevitable widespread use by machine builders, alongside an increasing technology toolkit stack, will help increase productivity and the value of products.
– This originally appeared on Control Engineering Europe.