Use software digital twins for smarter automation designs, simulation, integration, implementation and upgrades, as shown in short video.
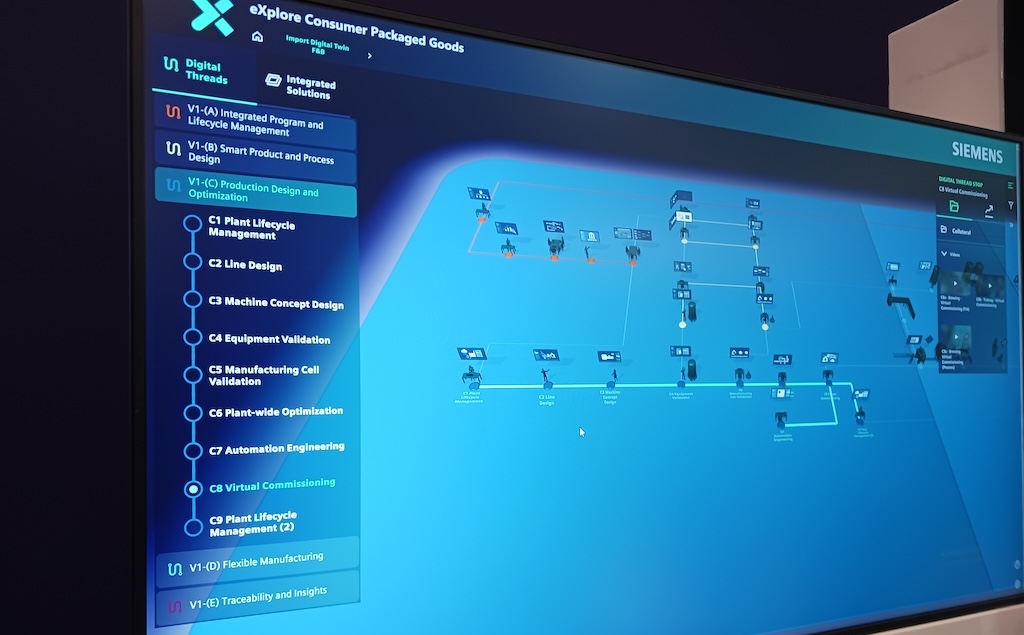
Learning Objectives
- Explore benefits of digital twin software for industry.
- Understand use of digital twins for design, simulation and commissioning to enable smarter automation.
- See related video of industrial digital twin abilities for machines, robotic cells and manufacturing lines.
Industrial digital twin insights
- Digital twin software enables seamless integration of new products, ensuring manufacturing changes occur without disruption or delays.
- Simulation software improves plant-wide optimization, cycle times, and efficiencies, allowing for validation before purchase and integration.
Digital twin simulation software helps for machine builders, robotic cell designers and line builders move more quickly from conception to sale to integration and implementation, explained Colm Gavin, portfolio developer manager with Siemens Digital Industry Software at Pack Expo Las Vegas 2023.
Benefits of digital twin software for industry
Customers and original equipment manufacturers (OEMs) benefit from seeing how to lay out manufacturing lines, design machines and look at manufacturing cell configurations. Manufacturers, by using digital twins, can better prepare lines, cells and workflows for new or modified products to ensure changes can be implemented seamlessly, without disruption.
Software simulations of machine, robotic cells and full lines help with plant-wide optimization, cycle times, efficiencies, utilization analysis and other key metrics. Virtual commissioning helps prove out the automation logic against the machine. Mapping signals from the automation to mechanical worlds to test automation beforehand helps ensure machines will produce the expected output for validation before purchase and integration.
A short video shows Gavin’s overview of benefits from Siemens Tecnomatix Plant Simulation software for throughput analysis, machine simulation and robotic simulation and improve integration. Siemens NX Line Designer MCD is used for plant, cell and line design. Siemens MCD Simit is for machine simulation.
Digital twins for design, simulation and commissioning enable smarter automation
According to Siemens information provided, the exhibit intended to show “A comprehensive approach to virtual production design, simulation and commissioning of production assets to reduce time and risk in new facilities, expansions, and retrofits and a product driven execution with adaptable automation to drive flexibility in the manufacturing operations.” This is achieved through agile manufacturing engineering, flexible and predictable manufacturing as well as with optimized, sustainable operations.
For related information, please see “How modern simulation software addresses intralogistics challenges.”
Mark T. Hoske is content manager, Control Engineering, CFE Media and Technology, [email protected].
KEYWORDS: Digital twins, industrial digital transformation
CONSIDER THIS
Are you using digital twin software to accelerate design and production?