Manufacturers realize the benefits of digital transformation, but many are often ill-prepared to realize the benefits because of organizational and technical readiness.
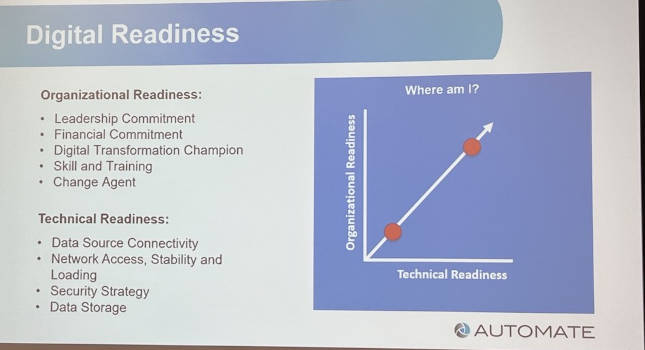
Digital transformation insights
- Manufacturers realize digital transformation’s potential, but many aren’t prepared or satisfied with the journey.
- Organizational readiness remains a key challenge because workers feel like they’re being replaced or challenged, and they often retain much of the valuable knowledge needed to improve operations.
Digital transformation for some companies has been like a tornado forecast with lack of preparedness for collaboration between information technology and operational technology (IT/OT) conflict. This has led to discontent with 8% of companies reporting satisfaction with their digital transformation project, said Mike Lashbrook, VP, digital solutions, JR Automation in his presentation, “Making Sense of the Madness: The Convergence of IT and OT Technologies on the Factory Floor,” at Automate 2023 in Detroit.
Why companies are dissatisfied with their digital transformation journey
Lashbrook said many problems stem from a company not being ready from an organizational, technical or financial sense. Even if they are, they lack the tools and the abilities to unlock the data and make it valuable as a commodity for operations. The data funnel also is hoarded by leadership and IT and OT can be shut out of the process, which has been a source of traditional resentments. Lashbrook said management team members often don’t realize how expensive it is integrating current and legacy equipment.
Many companies start with technology, which Lashbrook said is the wrong approach. “The best place to start with is understanding your digital readiness. And that can be broken down to organizational and technical readiness.”
Organizational readiness challenges
Lashbrook said companies are generally better along with the technical side of things because there have been more technology investments. The problem is getting OT to buy into the concept and helping OT teams understand that digital transformation is worthwhile.
“Manufacturing operations should be leading the charge rather than IT because they know the challenge and see the value on the factory floor,” Lashbrook said. He added IT does need to be working hand in hand with OT and needs to be a strong voice, but it should be complementary and helping OT rather than the other way around.
That is especially true, Lashbrook said, if operators feel like they’re being challenged or dehumanized in the data collection process. The hinderance to engaging operators is a social rather than technical challenge.
“Engage them from the beginning, make them part of the solution process and do it in a way so they understand the technology being used,” he said.
Once operators buy in, companies can accelerate learning through operator-generated data including:
-
4M (man, machine, method and material) information
-
Production fluctuations
-
Process time
-
Standardized work loading
-
Work scrolling/line balancing
-
Ergonomics
-
Error proofing
-
Traceability
-
Training
-
Continuous improvement.
Human resources is an underrated and underused resource, Lashbrook said. HR teams can help companies understand the talent and workforce gaps. Business and process knowledge is held by the experienced workers, whom Lashbrook referred to as “oak trees,” because of their sturdiness and their deep roots of knowledge.
“The oak trees retain the knowledge,” he said. “What needs to happen is companies need to get the knowledge out of their heads and over to the younger workers.”
Technical readiness challenges
Lashbrook said companies are often doing better with the technical side of things, but the challenge of turning data into actionable information remains an issue.
“What data is required? Identify the key performance indicators (KPIs). What do you want to improve and why? Those are all questions that need to be asked,” he said.
He said companies can get a head start by starting with an upcoming automation project where they can build data generation and access and start the process.
Understanding the network infrastructure and architecture is critical and needs to be looked at from top to bottom. Lashbrook said companies should ask questions such as:
-
Is it a greenfield or brownfield environment?
-
What technologies do companies already have?
-
What technologies do they want or need?
Companies also need to take cybersecurity seriously and ensure they have a strong data management strategy.
The digital transformation journey can be arduous, but recognizing organizational and technical challenges can help companies plan better to use human and technological resources more effectively.
Chris Vavra, web content manager, CFE Media and Technology, [email protected].