In a January 11, 2024 webcast, “Automation: Optimize next-level automation installations, 2024 and beyond,” Michael DeBoer, director of automation at Interstates, Eric Smith, President at APCO, and Scott Richards, senior project manager at Polytron discussed automation needs and opportunities, as well as providing best practice for implementation. Read part 4 of the transcript below.
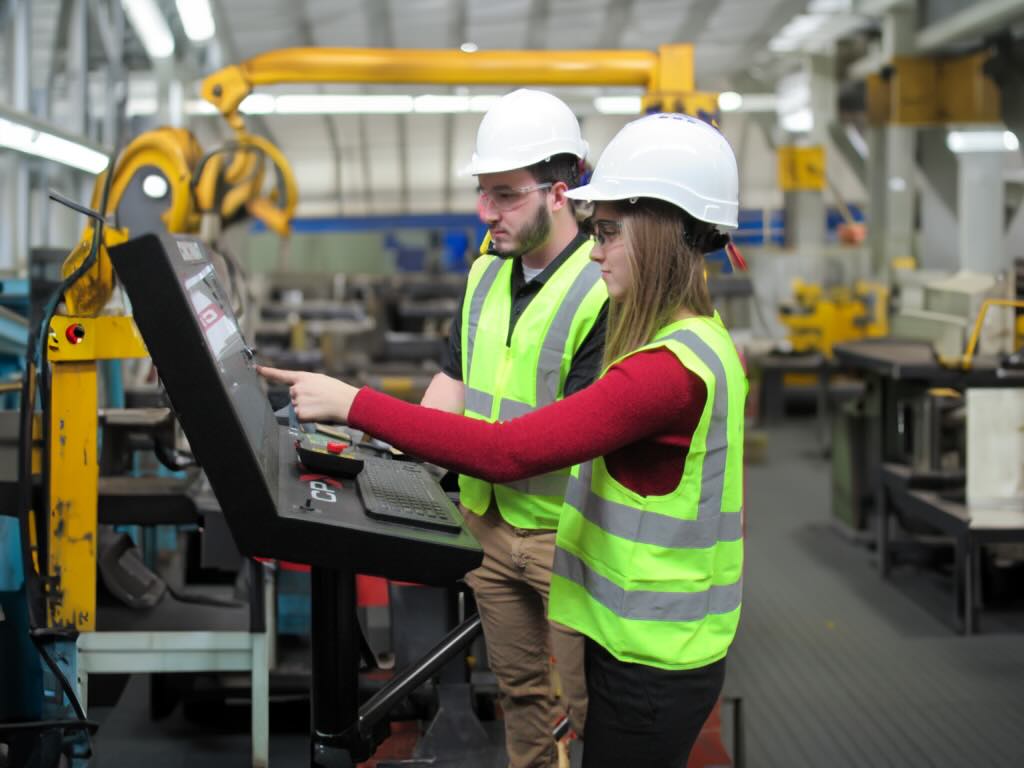
Automation insights
- In a January 11, 2024, webcast, “Automation: Optimize next-level automation installations, 2024 and beyond,” Michael DeBoer, director of automation at Interstates, Eric Smith, President at APCO, and Scott Richards, senior project manager at Polytron discussed automation needs and opportunities, as well as providing best practice for implementation.
- In Part 4, Richards discusses best practices for automation implementations.
In the pursuit of enhanced operational efficiency and productivity within industrial facilities, the push towards greater automation is increasingly evident. The question then arises: where does one commence this complex journey? The identification of bottlenecks presents a fundamental starting point, suggesting that the integration of advanced sensors, logic devices, actuators and analytics, coupled with enhanced visibility, could significantly aid in making more informed decisions. The dilemma extends to whether the focus should be on upgrading existing systems or the procurement of entirely new ones. Furthermore, it is crucial to remain cognizant of the latest standards and regulatory requirements that govern such technological advancements.
In a January 11 Control Engineering webcast, “Automation: Optimize next-level automation installations, 2024 and beyond,” award-winning system integration shared their advice on advancing to the next level of automation applications. The featured webcast instructors were:
-
Michael DeBoer, direction of automation at Interstates
-
Eric Smith, President at APCO
-
Scott Richards, senior product manager at Polytron.
The transcript of their presentation has been provided with minor edits and adaptations.
Capital allocation and equipment selection
Scott Richards: In most organizations, the competition for capital investment is intense, often evaluated based on metrics like net present value, internal rate of return, payback period, or discounted cash flow. System integrators, with their extensive experience in analyzing these metrics, can assist in building a compelling case for your project. In some instances, this may result in the project being reconsidered, but the expertise in navigating these numbers can prove invaluable in gaining approval from key decision-makers.
Regarding equipment selection, system integrators have established networks and relationships with a variety of vendors across multiple equipment categories, from processing to packaging and beyond. This extensive network and ongoing effort to stay informed of the latest market trends and innovations allow system integrators to provide substantial assistance in selecting the most suitable equipment for your project, especially useful during the concept stage if you prefer not to rely solely on turnkey OEM suppliers.
Budgeting and scheduling
System integrators frequently engage in budgeting and scheduling tasks, particularly during the definition phase of a project when aiming to refine cost estimates to procurement grade accuracy (e.g., plus or minus 10%) and develop a realistic project timeline. This experience in crafting detailed budgets and schedules can significantly benefit your project planning process, offering decision-makers a clearer picture of the project’s potential completion timeline.
Project execution and partnership with a system integrator
Throughout project execution, a proficient system integrator serves as your advocate, bringing to the table a wealth of resources and years of experience in managing projects similar to yours. From project management to the intricacies of programming, system integrators ensure that their success is inherently linked to yours, aiming for a mutually beneficial win-win relationship.
The value of partnering with a system integrator
Having outlined the various contributions a system integrator can make, it’s crucial to understand why partnering with one is advantageous. The insights shared thus far underscore the broad spectrum of support system integrators can offer, from preliminary planning and equipment selection to detailed budgeting, scheduling, and hands-on project execution. This partnership not only leverages their extensive industry experience and networks but also aligns their commitment to the project’s success with your objectives, ensuring a collaborative path to achieving project goals.
Leveraging project experience in system integration
Project experience stands as the foremost asset of system integrators like us, who are deeply engaged in the field every day. With a routine of handling numerous projects on a monthly and yearly basis, our breadth of experience is vast. It’s likely that whatever project you’re contemplating, your system integrator has undertaken something similar, if not identical. This prior experience means we’ve likely addressed many of the challenges your project will face, bringing invaluable insights from the outset. Whether the task involves an automation upgrade or the implementation of smart manufacturing or Manufacturing Execution Systems (MES) software, capital projects are our area of expertise. Unlike many manufacturing companies today, which lack the personnel for major capital projects—a notable shift from practices 50 years ago—we offer the specialized resources needed for such endeavors.
Staying abreast with technological advancements
In a rapidly evolving technological landscape, staying current is non-negotiable for system integrators. The introduction of new tools, such as artificial intelligence (AI), demands that we remain at the forefront of industry developments to offer the most effective solutions. This commitment extends to smart manufacturing and digitization, requiring us to continually refine our knowledge and skills. Our role is to navigate these technological advances on behalf of our clients, ensuring the deployment of optimal solutions within their facilities.
Resource depth and confidentiality
A significant challenge for system integrators is maintaining the right balance of resources. It’s crucial to have a sufficiently robust team to meet client needs without surplus capacity that leads to idle staff. Our success hinges on the quality and efficiency of our team, consisting of both seasoned professionals and emerging talent. Moreover, the aspect of confidentiality is paramount. Being a trusted partner means safeguarding all information related to a client’s facility with the utmost discretion. This includes physical measures to ensure confidentiality, especially when handling projects for competing clients. Our aim is to be a trusted advocate for our clients, embodying the role of a dependable partner in every aspect of our engagement.
Current project trends and client demands
Shifting focus to the current trends observed among our client base, there’s a notable demand for upgrades and automation, particularly in batch processing. The need for enhanced track and trace capabilities and sustainability measures is also prominent, underscored by the increasing recalls of food products. The importance of having reliable digital records to swiftly identify potential contamination in the product mix cannot be overstated. As we continue to monitor and respond to these trends, our goal remains to serve as a trusted partner and advocate for our clients, ensuring their projects not only meet current demands but are also poised for future challenges.
Trends in automation and cybersecurity
The demand for incorporating batch processes with advanced process control is on the rise, particularly with a focus on track and trace capabilities. The trend towards digitization across various workflows has led to an explosive growth in the need for robust industrial networks, integrating more touchpoints through the Internet of Things (IoT). This interconnectedness has elevated cybersecurity to a critical component of industrial networks, reflecting the ongoing demand for expertise in this area. While not a new concept, the growth in cybersecurity and network infrastructure needs shows no signs of abating.
Engaging with automation project trends: Poll insights
In an effort to gauge responses to increasing automation projects, a poll was conducted, presenting several options related to the aforementioned topics. The results indicate a strong interest in network infrastructure and assessments, highlighting a widespread recognition of the importance of robust network and automation project planning. This feedback aligns with the observed demand, confirming the industry-wide focus on enhancing network capabilities to support automation.
Exploring automation and controls projects
Projects within automation and controls, including the implementation of smart sensors for predictive maintenance in processing and packaging, offer significant opportunities for immediate returns on investment through downtime reduction. Additionally, device obsolescence and the need for updates to keep pace with technological innovation represent a substantial area of demand. Customers frequently request upgrades to existing systems, such as replacing older PLCs with newer models, rather than complete system overhauls.
Custom packaging and robotics
The adoption of robotics in custom packaging solutions, including case packing and palletizing, has become more appealing due to the efficiency and flexibility they offer. Suppliers face increasing demands from major retailers, which in turn drives the need for innovative packaging solutions, including the use of robotics and collaborative robots (cobots) that safely work alongside human operators.
Second poll: Identifying key automation trends
A follow-up poll sought to identify the most prevalent automation trends observed by participants. The responses highlighted automated predictive maintenance and obsolescence as the leading areas of focus, underscoring the importance of these aspects in current market conditions. This insight provides valuable confirmation of the ongoing priorities within the field of automation and controls.
Safety standards and simulation technologies
Safety continues to be a paramount concern, with a focus on adhering to the latest machinery and equipment standards. The complexity of navigating and interpreting various national and international standards necessitates expertise in conducting thorough risk assessments and implementing safety mitigations. Furthermore, the demand for emulation, simulation, and 3D point cloud technologies persists, facilitating more efficient planning and layout for new lines or extensions. The availability of more affordable and faster tools for creating 3D point clouds significantly aids in this process.
Conclusion and contact information
In closing, the presentation has highlighted significant trends and demands within the field of automation, from cybersecurity and network infrastructure to predictive maintenance and safety standards. Participants are encouraged to reach out with any further inquiries or interest in collaboration. With that, the session concludes, and the platform is handed back to David. Thank you for your participation and engagement.