Automation investment advice: Implement leading-edge automation technology, achieve a fast return on investment (ROI) and make it simple for the end user to support. These do not have to be mutually exclusive goals for automation technologies.
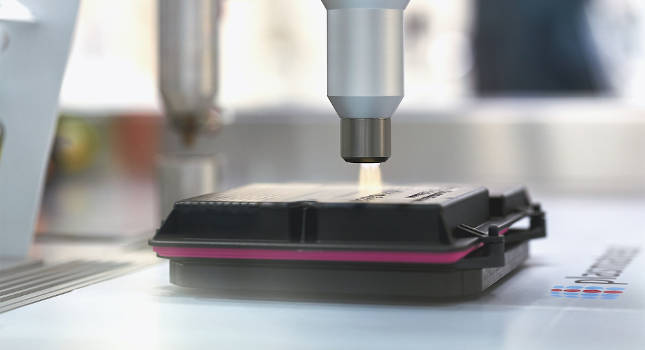
Learning Objectives
- Examine if current automation technologies can support the target application’s goals.
- Consider if the end-user community can support this technology.
- Calculate the automation return on investment (ROI).
Automation technology continues to grow more diverse and available. This is good news for the planet to meet the needs of a growing population sustainably and the engineers who create automated solutions. More applications and processes are becoming candidates for modernization. The question – to automate, or not to automate – can be tricky. Consider four variables on the path to greater automation success.
1. Do the current automation technologies support the target application’s goals?
This question is a little deeper than it seems. The automation platforms technology providers supply have caught up to the universities and integrated circuit (IC) builders. It is common for modern machines to connect to the web for operational inputs like global position, temperatures and energy prices to know when they should operate to maximize efficiency in production.
When automating uncommon processes, be sure to question everything about the application and available automation. For example, consider the assembly of a consumer good, such as an electric shaver. Perhaps doing so is unremarkable, unless the goal is to double throughput, create endless variants and reduce machine footprints; then there’s a need to know the latest technologies. Conveyors might get us there, linear motion closer, but planar motion will do the trick.
What is planar motion, “touchless” motion control?
Planar motion is a system with two parts – a “table” made of planar tiles and movers. The movers, travelling like a hovercraft, can be commanded freely around the table with a good payload. Path setups allow serial or parallel assembly, depending on the tact time and product features. These planar motion systems allow moving the workpiece to the operation instead of moving the operation to the workpiece.
In a fully-integrated architecture, the flying motion system can achieve more.
For example, machine learning (ML) and artificial intelligence (AI) often lead to better performance, machine stability and energy savings. These results can be achieved even faster and to a greater degree when ML is implemented in a standard machine controls environment.
Select an automation technology partner with packages ready to integrate ML into a machine. Knowing what the market provides helps in evaluating an application capabilities against application goals.
2. Can the end-user community support the technology selected?
If planar technology, for example, was selected as the best way to move an assembly application forward, will the technology integrated into the machine operate with minimal downtime and receive 24-hour support?
While application engineers may say, “Yes,” end users often insist on ladder logic programming code. Often the time and energy an applications team put into writing code for the machine and planar motion system cannot be understood by machine users or operators.
The remedy is not to program planar motion in Ladder code or put comments in the code, though both could help. The remedy is an operator interface (human-machine interface (HMI)) designed for a person assumed to have zero experience with the machine, like the boss (sorry, bosses).
Side note: When the office printer jams, the boss does not crack open ladder code to troubleshoot what’s wrong. Instead, those involved turn to the printer’s display, follow the instructions and remove the problem.
This approach to troubleshooting is even more important for complex mechatronic systems.
As industry moves toward the future and faces greater skilled labor shortages, it is clear companies are willing to pay more to partner with original equipment manufacturers (OEms) that can provide intuitive ways to keep production running. Plant floor operators and supervisors like keeping operations running without calling maintenance to open laptops and dig into code.
3. Where’s the automation return on investment (ROI)?
After setting goals and finding how to support a new automation concept, does the price justify the effort spent? This is a time-honored question. Looking at the planar system example, each tile that makes up the table of a planar system is essentially a drive, so the costs of building a table can get expensive, making the design cost intimidating. The same model applies to linear transport systems and robotics motion control. However, because planar movers have 6 degrees of freedom (DoF) and can be the size of the piece being assembled, the cost is offset in a big way.
How does a planar system integrate into machine design?
Planar systems use the mover to do the work of the robot, meaning you can replace the large working envelopes that robots require for assembly with simple, space-saving, single-axis devices. This increases capacity (or peripheral density) and adds options for new features in a very small footprint machine. It provides innovative ways to reduce changeover times, which are big value-adds to most end users.
As another example, consider replacing walking beam machines with linear motor systems. New advantages include flexible parallel operations, collation and control of tact time in a smaller-frame machine. There are cost tradeoffs. More than enough value justifies any cost differences.
4. Are there fewer handoffs in production or machine modules than previously?
Limiting handoffs between processes or machine modules with machine design make lives easier. Many production problems originate with jammed conveyors, worn or loose belts, or incorrect operation because a product is out of position. Imprecise or halted motion affects quality with reworks or scrap and takes a lot of personnel to troubleshoot, identify and remedy such breakdowns. Robotics can improve the handoffs between machine modules and adds cost, footprint and complexity.
Designing around a planar concept
By designing around linear motor and planar concepts, the goal is to accomplish all assembly operations while the workpiece remains on the system’s mover. This non-linear manufacturing technology doesn’t have to pass off the workpiece between modules. Instead, the movers carry the workpiece through multiple processes, eliminating handoffs that used to be necessary. This improves overall ROI and machine uptime since operators avoid tweaking conveyors, timers and working changeovers.
By using examples in linear and planar motion, understand how to better move the workpiece to the operation rather than move the operation to the workpiece. By embracing new automation technologies, OEMs and manufacturers can rethink what is possible, shatter conventional limitations in machine design and create a new class of machines designed to solve many new challenges.
Tom Jensen is assembly industry manager, Beckhoff Automation LLC. Edited by Mark T. Hoske, content manager, Control Engineering, CFE Media, [email protected].
KEYWORDS: Motion control, mechatronics, control design
CONSIDER THIS
What new levels of efficiency could automation designs achieve with new motion control technologies?
ONLINE extra
Touchless logistics: Beckhoff Automation provides more information on its XPlanar floating transport system at www.beckhoff.com/xplanar.