Industrial energy efficiency is important for machine design as measurements for motor and drive efficiencies show.
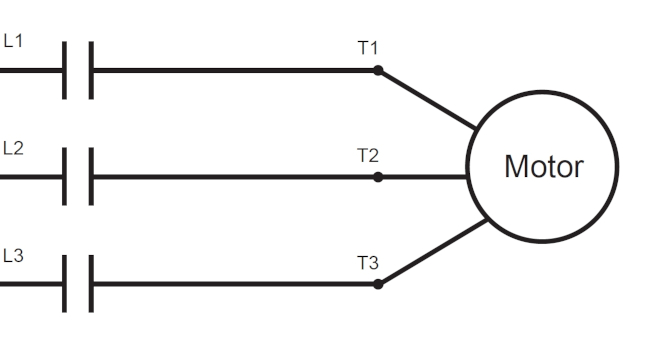
Learning Objectives
- Understand the benefits of energy efficiency systems and resources for motors and drives.
- Examine theoretical and technological methodologies to determine energy efficiency for motors and drives.
- Quantify and analyze results of motor system energy efficiency, including drives.
Energy efficiency insights
- Energy efficiency systems provide considerable benefits for motors and drives and connected machines.
- Examples demonstrate theoretical and technological methodologies to determine energy efficiency for motors and drives.
- Quantifying and analyzing motor system energy efficiency, including drives, provides greater understanding of what machine design changes can provide what benefits. In some designs, energy use may be reduced by half.
Energy efficiency in motors and drives is a crucial component of modern industrial and technological progressions, contributing to a systems sustainability and cost-effectiveness future. For industrial sustainability, cost effectiveness and other benefits, it’s important to use energy-efficient motors and drives. It’s also useful to understand measurements and methods used to determine energy efficiencies and know that energy-sponsored programs offer supportive measures and financial incentives for businesses looking to transition to more efficient systems. For a better understanding of motor and drive efficiency, examine the following three topics.
Topic one: Why industrial energy efficiency is important
Industrial energy efficiency is important for energy program savings, machine efficiency and other useful improvements.
With respect to machine design, using energy efficient motors and drives offers advantages extending beyond energy consumption. These benefits encompass:
-
Cost-effective: Energy-efficient motors and drives maintain optimal performance while consuming less electrical energy (kilowatt-hours, kWh). This leads to substantial savings on energy invoices and decreasing return time frame.
-
Equipment life span: With less energy loss in the form of heat, this allows machines to run cooler and with more longevity. All the while using less energy or lower kilowatt-hours.
-
Enhanced precision and control: In addition, less heat is generated and mechanical wear is reduced. This leads to an overall design that minimizes electrical noise, as well as improves precision, responsiveness and control.
To support businesses, energy sponsored programs offer cost-saving opportunities and consultation for eligible applications. Energy efficiency programs vary from state to state and also may differ based on a company’s operating region.
One program example, located in the New England area, is operated by Eversource Energy, Electric Services Co. For that program, “Variable Speed Drives & Motors,” a website offers information on how to participate and be eligible for new and existing drives and motor applications. Programs like this help companies save on energy efficient retrofits with a rebate based on kilowatt-hour savings per year or percentage of the retrofit’s incremental cost. States and local energy providers can provide details that apply to specific areas.
Topic two: Measurements, calculations for motor and drive efficiencies
For motor and drive efficiency calculations, the next example looks at a 480 V calculation and how to obtain values theoretically and mechanically with a dynamometer. Below:
-
See how to measure energy usage using an energy analyzer
-
Examine a Fluke readout of power monitoring over a one-week
As an integral part of preventive maintenance, calculating the energy efficiencies of a motor and drive is a valuable practice in assessing performance and optimizing operations. The fundamental approach involves calculating the theoretical energy efficiency (η).
η = Output power (Po) / Input power (Pi)
For a motor, where Po represents the mechanical power delivered by the motor and Pi represents electrical power supplied to the motor. Likewise, the energy efficiency of an amplifier is determined by the ratio of delivered power (Po) to consumed power (Pi). The efficiency accuracy of a system overall will depend on the evaluation of potential power losses for both servo drive: Conduction, switching, logic processing, standby power, etc., and motor: Copper losses, iron losses, mechanical losses, etc.
Some users may prefer to use the latest technologies and methods that are more reliant and accurate for energy studies to take place over days at a time. In these cases, using the information generated from the studies can be very useful to assess and make energy decisions. In the example measurement for an across-the-line motor starter circuit operating system, the finalized report has provided the standard cost of energy of $346.34 for the active energy 1.385 MWh, the total energy consumed by the system over the specific period of time.
By using an energy study software of choice, create and track energy use and other information over time to find trends. Measurements of interest may include a system’s power factor, which is a measure of how effectively the electrical power is converted into useful work. The ratio is between the active power (kW) and apparent power (kVA). A power factor close to 1 indicates an efficient operation.
Available technologies like a dynamometer also may be used to obtain a comprehensive understanding of testing, measuring and plotting the energy efficiency of motors over various loads. Use the measured torque and rotational speed (RPM) of a system to determine the power output:
Power(Watts)=Torque*RPM*2π/60
… and to determine power input consumed by the motor:
Power(Watts)=Voltage*Current(A)*PowerFactor.
With both theoretical and mechanical methodologies available for use, use an approach and adopt tools to ensure systems continue operating at peak efficiency and receive proper maintenance.
Topic three: Measuring motor and drive efficiency results
One way to quantify energy saving results is to measure the actual energy usage, in kilowatt-hours, before and after a machine is upgraded. This can be done using a power analyzer device and will give an exact comparison of energy usage. It is important to keep in mind that the machine’s performance profile, the actual work done by the machine during measurement, should be matched in the before and after measurement phases. Doing so will ensure an even comparison of energy efficiency.
The energy analysis shown was taken using an across-the-line motor starter. This type of circuit becomes energized as soon as the panel does and remains on as long as power is present. This draws a steady supply of current regardless of the actual energy demand from the machine.
When the contactor coil is energized, the L1-3 contacts close and line voltage and starting current are connected directly to the stator windings.
The across-the-line motor starter circuit could be replaced in favor of servomotors, which are designed to be energy efficient providing on-demand torque. This differs from air pumps and hydraulic sources, as well as across-the-line motor starters, which need to remain running all the time in case there is a demand from the machine. Servomotors, however, also can drop down to zero torque when there is no demand. This increases energy efficiency and has been shown to cut machine energy usage in half compared to other types of sources.
Servomotors use servopacks, or servo-amplifiers, to achieve efficient operation. Servo-amplifier components comprising bipolar junction transistors (BJTs), diodes, capacitors and other electrical components, allow servomotors to reduce energy consumption. Servomotors have a much lower current draw when the demand from the machine is low, leading to increased energy efficiency. Efficiency improvements are derived from:
-
Switching to servomotors to reduce energy use in half in machine
-
Eliminating air pumps, hydraulic sources, etc.
Dulce Maria Varela is a regional motion engineer, and Matthew Hardenbergh is the northeast regional motion engineer, both with Yaskawa America Inc. Edited by Mark T. Hoske, content manager, Control Engineering, CFE Media and Technology, [email protected].
CONSIDER THIS
Motor and drive systems can drive energy efficiency, save month, add life to equipment and enhance precision and control.