Demonstration models show enormous motor energy savings without magnets, using 90% less copper for the C-Motive ultra-high-efficiency, electrostatic motor, as shown at Automation Fair event by Rockwell Automation. See short video.
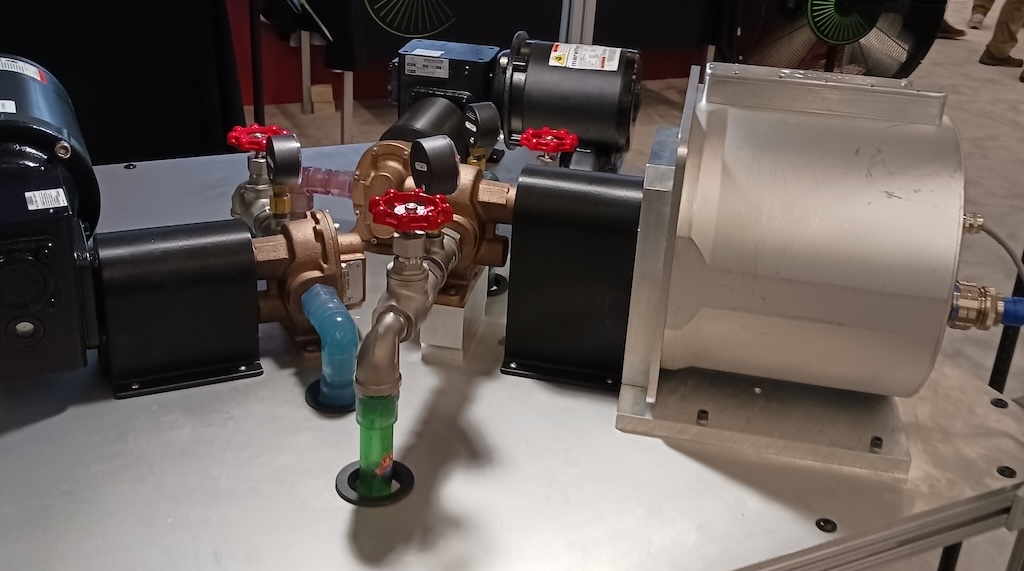
Learning Objectives
- Understand differences and energy savings in an electrostatic motor design comparted to traditional motors.
- Learn how electrostatic motors use 90% less copper and tout 98% efficiency in most applications, compared to 84% for standard efficiency motor designs.
Electrostatic motor insights
- Design differences and energy savings in a C-Motive electrostatic motors have significant advantages over traditional motors.
- Electrostatic motors use 90% less copper and tout 98% efficiency in most applications, compared to 84% for standard efficiency motor designs.
Most motors use magnets and a lot of copper; the C-Motive motor uses electrostatic principles instead in a motor design that uses 90% less copper promises 20 to 50 Nm torque at 0 to 300 RPM without permanent magnets, gearbox or pulleys, as demonstrated at the Automation Fair 2023 event by Rockwell Automation.
The low-speed, high-torque electrostatic motor design is said to have efficiency of greater than 98% in most applications, the company said; each 1 hp electrostatic motor saves approximately 2 metric tons of CO2 annually. [For comparison, a standard efficiency motor may be around 84% efficiency; an advanced design premium efficiency motor design can exceed 90% efficiency.] In a short video, Matt Maroon, chief executive officer, C-Motive, explains more about electrostatic motor design and benefits.
Electrostatic motor design elements, benefits
The C-Motive motor uses voltage, printed circuit board plates and a proprietary dielectric fluid to create motive force, whereas a traditional motor uses more voltage, permanent magnets and a lot of copper or copper-wire windings to create rotating or linear force. In addition, electrostatic motors operate in audible silence, have extremely low torque ripple and run comparatively cool under load, requiring no active cooling and have much lower power draw (<0.2% full power) for zero speed holds, compared to traditional motor designs.
The electrostatic motor design may provide sustainability and supply chain benefits with copper demand expected to double by 2035 along with widely variable copper prices in world markets. A large region in Asia is responsible for a majority of copper, electrical steel and permanent magnets, used for traditional motor designs.
Electrostatic motor design demonstration at Automation Fair
In the Automation Fair demonstration, three motors pumped fluid at the same speed and flow rate to compare heat generated by the electrostatic design to permanent magnet motor and induction motor. The thermal imaging shows little heat generated by the electrostatic design and considerable heat (and efficiency losses) from the other motion system designs operating at 60 to 65% efficiency. C-Motive information said, “Electrostatic motors are significantly more efficient, require no added gearbox and generate less heat than motors that use magnetism.” Electrostatic motors run cooler and are said to perform especially well in “direct-drive, low-speed, high-torque applications.” It can operate fully submerged and is said to be able to scale to multi-megawatt size using the same design principles.
C-Motive, headquartered in Middleton, Wisconsin (near Madison), derived from research at University of Wisconsin-Madison about 10 years ago, now includes a team of 20 experts with experience that includes power electronics, chemistry and mechanical design. C-Motive, a venture-backed startup company, owns around 50 patents and applications, U.S. and international and is said to use a fully U.S.-based materials supply chain.
The company seeks partners for demonstration opportunities and for industrial integration.
Mark T. Hoske is content manager, Control Engineering, CFE Media and Technology, [email protected].
KEYWORDS: High-efficiency motor design
CONSIDER THIS
How would you apply a more efficient direct-drive motor?