Well-engineered design, which takes into account the physical environment, safety and security can help make wireless control the new normal in factories and plants around the globe.
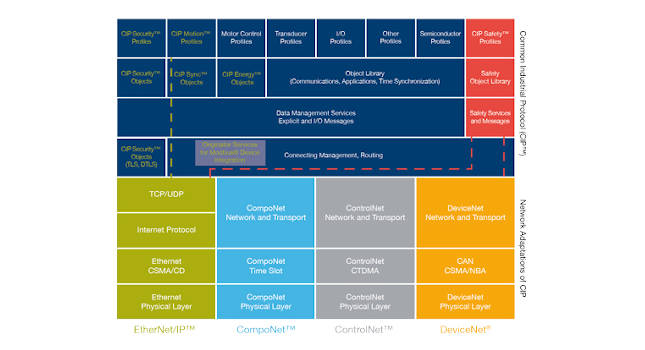
Advances in wireless network speed and reductions in latency over the past couple of decades have fundamentally altered communication globally. Wireless cellular technology has moved from 3G at 20 Mbit/sec speed in the 2000s to 5G at up to 20 Gbit/sec speed today, with generational advances taking place approximately every decade. The past three Wi-Fi specifications have been released about five years apart, with Wi-Fi 4 allowing download speeds of 600 Mbit/s and Wi-Fi 6 enabling speeds of up to 9.6 Gbit/sec.
While the generation advancements for both of these technologies have taken place at a constant linear rate, the speed has increased at an exponential rate. This dramatic decrease in communication time has enabled remote connectivity of machines such as palletizers in packaging facilities and isolated instrumentation in oil and gas fields to allow remote monitoring for maintenance support as well as plant wide networks in automotive for advanced diagnostic analysis.
Wireless communication initially enabled voice for business, then grew in capability to transport data for business and automation, including video, and finally is poised to be a viable solution for control in automation, especially with private and hybrid network option availability for 5G. The next frontier in the continued progression of wireless networks is widespread control in both discrete and process environments, which will get a significant jumpstart from the new 5G and Wi-Fi 6 technologies.
Automation considerations for wireless
Wireless communication in an automation environment brings a host of additional opportunities and challenges. Some of the benefits include potential savings in installation cost due to not having to install physical cable, increased connectivity of devices and instrumentation, and decreased challenges in routing cables in environments with a high degree of movement.
However, challenges such as safety, security, and physical location must be addressed in order for wireless to be truly viable in automation control applications. Security is a critical concern since a new exploitation opportunity can open up from outside the walls of a factory or gates of a plant with wireless. Stray signals can be mitigated with radiating cable and smart placement of the antennae. However, it is important to authenticate transmitting nodes, to encrypt traffic, and to ensure that configurations cannot be changed without a password or key. As a part of a defense-in-depth solution, device and edge control level automation traffic can be further protected via solutions such as the common industrial protocol (CIP) security network extension for EtherNet/IP.
Safety is another critical aspect for wireless, especially for mobile vehicles, machinery with motion, and locations where workers can come into contact with potentially dangerous movement. Safety design for electronics is guided by IEC 61508 and IEC 62061, which specify how to apply failure mode analysis, continuous diagnostics, and other robust design practices for electronic system safety. Additionally, IEC 13849 covers the same design safety approach for electromechanical systems.
To meet these standards, many industrial safety systems leverage the black channel approach. This concept requires safety devices to have enough compute, intelligence, and diagnostic capability that the entire communication network has zero impact on the ability of the safety devices to detect communication errors. This means that the physical transmission medium is just another part of the black channel.
Application layer safety solutions, such as the CIP safety network extension for EtherNet/IP, can provide fail-safe communication between nodes such as safety I/O blocks, safety interlock switches, safety light curtains and safety controllers in machine and process automation safety applications up to safety integrity level (SIL) 3 according to IEC 61508.
Distance, obstacles and interference also must be considered for wireless control applications. It is important to ensure that distance is minimized, that line of sight is maintained, and that interference from high voltage and other sources of high frequency signals are minimized. Interference can result in wireless networks having higher packet error rates and reconfiguring themselves more frequently than wired networks, which can create delayed and lost packets as well as connection timeouts. These transitions can potentially disrupt automation applications, depending on the speed that is required. Wireless repeaters are an option to help increase signal strength and overcome potential interference.
Wireless application examples
A clear example of the value of wireless control is for automated guided vehicles (AGVs) that transport materials around a factory or warehouse. It is costly to create a physical track on the floor for an AGV to travel on and this cost multiplies when process changes require new layouts. Welding cells within automotive have also adopted wireless control in order to remove some of the challenges or running cables in tight spaces with a high degree of movement.
Process automation has long leveraged wireless control for connectivity between remotely located and spread-out instrumentation that are a part of wind farms or oil and gas fields. Additional possibilities include using less cable for hygienic design in food and beverage applications, modular and flexible plant design to prepare for Industry 4.0, and adding data collection sensors to legacy devices for IIoT analysis.
EtherNet/IP over wireless
The EtherNet/IP industrial communication network communicates data between devices and instruments at the application layer of the ISO/OSI model, using the CIP protocol. CIP information is then encapsulated in the transport layer, which uses either TCP for larger data packets such as diagnostics or UDP for smaller, more time sensitive data packets such as I/O for EtherNet/IP. At the network layer, logical addressing IP information is added to make the packet ready for network access.
In the datalink layer and the physical layer, the packets are converted to the transmission media. This approach of communicating data via CIP, independent of the transport, network, datalink or physical layers, makes use of different transmission media possible. EtherNet/IP can be used across copper, fiber and wireless to provide users with a high flexibility for use across numerous industrial applications.
The path forward
The industrial space has already been experiencing the advantages of diagnostic information via wireless for some time and is now set to engage in a significant shift to using wireless for control. Technologies such as 5G and Wi-Fi 6, among others, will help to drive the increased speed and reduced latency that industrial applications demand. EtherNet/IP will be one of the key industrial communication protocols that will enable this change due to its media independence enabled by CIP communication.
This article originally appeared on Control Engineering Europe’s website. Edited by Chris Vavra, web content manager, Control Engineering, CFE Media, [email protected].