Arla Foods achieved energy transparency during cottage cheese production at a factory in Sweden. A flow sensor monitors temperature and flow rate.
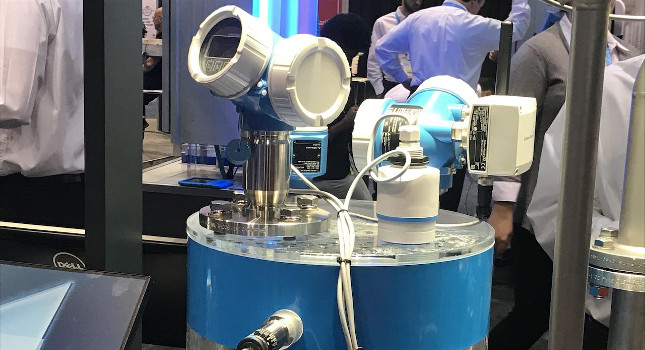
Learning Objectives
- Food manufacturer wanted to monitor and improve process energy use.
- Sensors that measure temperature and flow rate were installed in key locations.
- Measurements are helping the food maker reach a carbon-neutral goal for 2050.
Using flow and temperature sensor measurements helps a food processor monitor energy consumption.
At its Falkenberg factory in Sweden, dairy cooperative Arla Foods produces 20,000 tons of cottage cheese annually. Production volumes of this magnitude call for a resource-efficient manufacturing process, and Arla Foods is working toward making its products CO2-neutral by 2050.
Energy: You cannot control what you do not measure
A key element of this journey is energy efficiency. Mattias Abrahamsson, production system manager at Arla Falkenberg, explained: “In recent years, we have placed an increasingly strong focus on monitoring the energy consumption of our plants. In certain areas, however, we simply didn’t know where exactly the energy was being used.”
A calorimetric flow sensor helped the company achieve a breakthrough. Arla installed these sensors at the neuralgic points in the cooling and heating system and used the measurement results to obtain a clear image of energy consumption which allows the company to put in place measures for reducing energy consumption.
Outside temperatures help with process cooling
The food manufacturer had already made a great effort to reduce the energy balance when the plant was designed. For example, it uses the low external temperatures of the Swedish climate to achieve a cooling temperature of 0.5°C for the cooling circuit, which cools the produced cheese from 60 to 30°C. Yet energy losses which Arla had been unable to localize for some time occurred here as well. The sensors solved the problem of monitoring energy consumption because they could be integrated into the existing plant and can measure flow and temperature.
Arla has already installed 15 of the flow sensors in the cooling circuit and heating system. The plan is to integrate these sensors into the clean-in-place (CIP) return line to monitor and also optimize the energy consumption there.
Abrahamsson said about the project, “This has proven to be a cost-efficient solution. And because the sensors installed so far are reliably returning the results we need, we will now install more.”
This Baumer UK article originally appeared on Control Engineering Europe’s website; Edited by Mark T. Hoske, content manager, Control Engineering, CFE Media and Technology, [email protected].
MORE ANSWERS
KEYWORDS: Temperature measurement, flow rate
Food manufacturer wanted to monitor and improve process energy use.
Sensors that measure temperature and flow rate were installed in key locations.
Measurements are helping the food maker reach a carbon-neutral goal for 2050.
CONSIDER THIS
What metrics where can help your processes use energy more efficiently?
ONLINE
If reading from the digital edition, click on the headline for more resources.