Profinet enables reliable communication and rises to the challenges of Industry 4.0 and the factory's digital transformation.
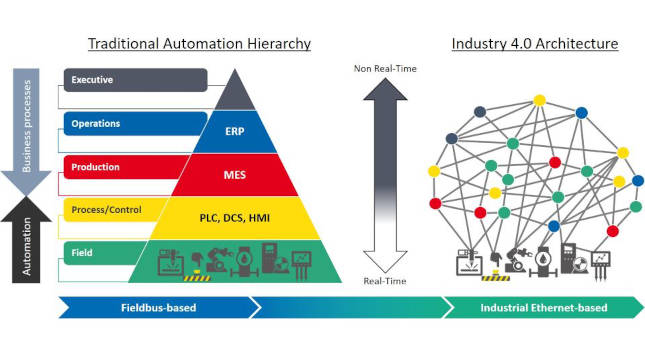
Digital transformation insights
- Industry 4.0 aims to leverage cyber-physical systems to enable new production capabilities, create value, and augment real-time operation, by turning data into information and then into some type of action.
- Profinet is an OT protocol that overcomes the challenges of Industry 4.0 by ensuring speed and determinism, providing alarms and diagnostics to keep automation equipment running, and supporting topologies for reliable communication.
Industry 4.0 is a lot of things to a lot of people. Ask someone what the vision of Industry 4.0 is and you will probably get as many answers as the people asked. When we think of Industry 4.0 in the context of the digital transformation of the factory, one could argue the big picture vision is to leverage cyber-physical systems to enable new production capabilities, create value, and augment real-time operation. This vision isn’t going to happen overnight, though. It’s going to happen slowly and methodically.
In practical terms, Industry 4.0 is the digital transformation of manufacturing so we can turn data into information and turn that information into some type of action, improve a process, or improve product quality. We look at the manufacturing environment as a connected environment of people, processes, data, and services regardless of the type of automation we are using. With this view, we can turn data into actions like managing assets, tracking downtime, or changing production schedules based on predictive maintenance information. We can also use data to keep processes in control, optimize machine efficiency, or minimize energy consumption. Really, the possibilities are endless, but they all drive us towards the vision of Industry 4.0.
Digital transformation in factory networks
Nowhere is the impact of this digital transformation greater than on factory networks. There has been an explosion in the number of devices in manufacturing facilities. It’s not uncommon for car manufacturers to have over 50,000 Ethernet nodes in just one of their factories. Large production cells can have 1,000 Ethernet nodes in them. And all of these nodes increase the traffic automation devices must handle. It’s not unrealistic for a device to deal with 2,000 different messages while it’s operating. Emerging technologies like automated guided vehicles (AGVs) add a level of dynamics to the network architecture because they enter and leave various production cells located in different manufacturing areas. And as factories become more flexible, networks must support adding and removing devices while the factory is operating.
So in response to this digital transformation, Figure 2 below shows how we have gone from rigid, hierarchal systems using fieldbuses, to Industrial Ethernet-based networks where any device can be connected to any other device. Industrial IoT devices at the field level can be connected to Industrial IoT devices at the process/control level, the production level, even the operations level and above. However, this doesn’t mean the requirements for determinism, redundancy, safety, and security are any less on a converged network; it means you need to have a network technology that supports these requirements. This is where Profinet comes in.
Profinet as an industrial solution
So what is Profinet, and what challenges is it trying to overcome? The most obvious challenge is environmental. We need to operate in a wide range of harsh environments. We obviously need to be deterministic, meaning, we need to guarantee data delivery. But this has to be done in the presence of IT traffic or non real-time applications like web services. We also can’t operate in a vacuum – we need to operate in a local area network and support getting data to wide area networks and up into the cloud.
To overcome these challenges, Profinet uses communication channels to ensure speed and determinism. It uses standard unmodified Ethernet so multiple protocols can co-exist on the same wire. Most importantly, Profinet is an OT protocol that runs at the Application Layer to maintain real-time data exchange, provide alarms and diagnostic to keep automation equipment running, and support topologies for reliable communication. And this is why Profinet rises to the challenges of Industry 4.0 and the factory’s digital transformation.
– PI North America is a CFE Media and Technology content partner.