5G is appealing to industrial automation where distance concerns can be overcome easily with many cells and the performance can surpass that of traditional Wi-Fi.
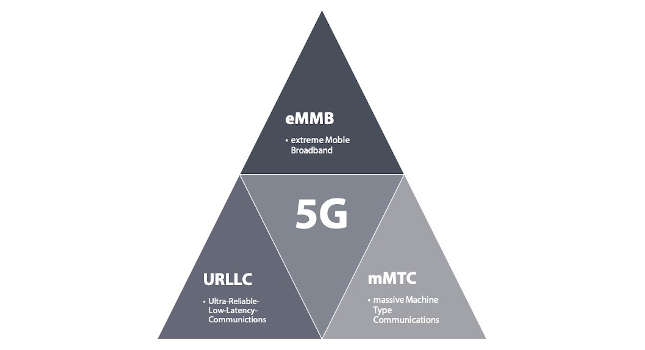
5G is a broad term describing a range of different technologies and implementations and can mean many different things to many different people. Even among the major consumer cellular providers, the 5G that each provides can be different from the next.
Generally these offerings span either: low-band, mid-band, or high-band. There are benefits and trade-offs for each. Low-band 5G yields better penetration and distances, but at lower speeds and bandwidths. High-band 5G provides more performance but at the expense of longer distances.
For these reasons, high-band 5G is appealing to industrial automation where distance concerns can be overcome easily with many cells and the performance can surpass that of traditional Wi-Fi.
Three potential applications for 5G
There are three main categories of use-cases for 5G. Of course there will be applications which span more than one category; hence the broad appeal of 5G.
- Extreme mobile broadband (eMMB). Use-cases here include those requiring very high bandwidth and data rates. Applications include high-definition video streaming.
- Massive mobile machine type communications (mMTC). Use-cases here include those requiring a large amount of devices, typically in dense proximity to one another. Applications include the Internet of Things (IoT) or smart cities.
- Ultra-reliable low-latency communication (URLLC). Use-cases here include those requiring high determinism and mission criticality. Applications include self-driving cars and industrial automation. It is here where 5G becomes applicable to industrial networks like Profinet.
5G benefits for industrial automation
The focus on 5G in Industry at the moment is on the ability to create private networks. A private 5G network does not rely upon the infrastructure of traditional telecommunication companies. Instead, it is installed and configured by the user locally.
In early 2020, a collaboration between Audi and Ericsson achieved 3ms cycle times with 1ms latency running Profinet and PROFIsafe over 5G. Such timescales also are a requirement for factory automation, and enable use-cases like automated guided vehicles (AGVs) or automated mobile robots (AMRs).
Because PROFIsafe uses the black channel principle, no special configuration is required to enable functionally safe communication between PROFIsafe devices and controllers over 5G.
This article originally appeared on PI North America’s website. Edited by Chris Vavra, web content manager, Control Engineering, CFE Media, [email protected].