Automation and controls company and Chinese petrochemical firm integrate technologies for smart factory benchmarking. One plant reduced manual operation more than 50% and increased propylene yield by more than 0.1%.
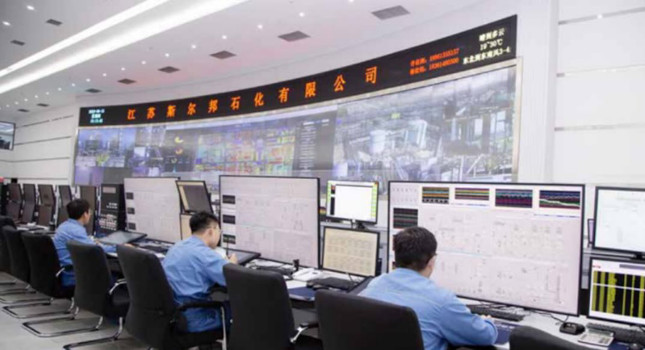
Learning Objectives
- Understand how Shenghong Petrochemical and Honeywell collaborate on integrating digitalization and plant optimization control technologies to decrease manual operation and increase output.
- Consider how smart factory optimization includes digital construction and transformation of the plant lifecycle from the vertical application layers and using results in the design phase at other plants, dynamic iteration of connected factories.
Digitalization, process control insights
- Shenghong Petrochemical and Honeywell collaborate on integrating digitalization and plant optimization control technologies, reducing manual operation more than 50% and increasing propylene yield more than 0.1%.
- Smart factory optimization includes digital design construction and transformation of the plant lifecycle from the vertical application layers and using results for dynamic iteration of connected factories.
With new technological advancements and rapid changes in new concepts, the construction of intelligent factories in the petrochemical industry has become more complex and diverse. How can petrochemical enterprises realize digital transformation more effectively?
Honeywell and Shenghong Petrochemical jointly released the June 28 white paper, “Dual Technology Integration, Operational Excellence: Honeywell-Shenghong Petrochemical Smart Factory Practices” during the 14th Summer Davos Forum. Plant benefits include reduced manual operation of more than 50% and increased propylene yield by more than 0.1%.
The core secret of dual-technology integration
For many years, Honeywell and Shenghong Petrochemical have maintained a close strategic partnership. For two years both discussed how to promote digital and intelligent transformation of Chinese petrochemical enterprises. Starting in 2021, they conducted comprehensive cooperation in intelligent factories and advanced control around the Propane Dehydrogenation (PDH) device of the second phase project in Sierbang. Shenghong is promoting the process of digital transformation through digital operation and intelligent production.
Bai Wei, president of Shenghong Petrochemical Industry Group, said, “Honeywell is not only a supplier of process control systems and a provider of process technology.” Empowered with Honeywell digital intelligence technology, Shenghong connected the process of procurement, production, sales, logistics, human resources and finance, building a strong innovation empowerment platform for the digital transformation of the industrial chain.
The project included Honeywell’s in-depth integration of its UOP refining process technology and expert insights.
Talking about project integration, Liu Maoshu, vice president and general manager of Honeywell Performance Materials and Technologies Group in Asia-Pacific, said: “Honeywell can fully and closely integrate UOP’s century-old process technology with mature digital intelligence technology, and provide the process industry with the most effective and efficient way to optimize operations and make decisions by focusing on the safety of the enterprise’s production, operation optimization and decision-making, providing innovative ideas for technological change in the process industry and helping to build a new digital ecosystem in China.”
Explore more digital technology application possibilities
As early as 2019 in the refining industry, Honeywell presented a forward-looking “future refinery” concept. To build a smart factory for the process industry, it is necessary to realize the digital construction and transformation of the whole lifecycle from the vertical application layers (including the perception and control layer, the production and operation layer and the enterprise management layer), as well as the horizontal implementation process, such as making full use of the digital delivery results in the design phase.
Based on empowerment and focusing on the construction goals of ensuring process safety, optimizing plant efficiency, improving production management, reducing operating costs and creating a benchmark for intelligent plants in the propane dehydrogenation industry, Honeywell implemented seven sub-systems in the Sierpong plant using integrated operating windows, advanced control and optimization, intelligent operation management and digital twin and interconnected applications. Doing so delivered considerable digital benefits.
Through the deployment, implementation and efficient operation of seven major subsystems, Honeywell helped Shenghong solidify its device performance, production costs and key carbon emission indicators. The PDH device in Sierbang has become the first production device in China that combines process technology and intelligent technology applications to achieve comprehensive intelligent production and digital operation.
In the modern central control room of the Sierbang factory, operators can use the large screen of the Honeywell Experience PKS Orion Console to clearly view the trend monitoring and real-time key-performance indicators (KPIs) of multiple sets of operating data. Led by the successful practice of this smart factory, Sierbang reconsidered the application of digital intelligence technologies, expects to continue to deepen and promote digital technology in the future and continues to explore and unlock the wider application of new technology in more installations.
Implement dynamic iteration of connected factories
As one of the important pillar industries of the national economy, in recent years, the petrochemical industry has faced the opportunities of the commissioning boom with more severe market uncertainty, operational safety, green dual-carbon, human resources and other challenges.
Bai Wei said: “Petrochemical companies with heavy resource inputs and continuous operations will face more difficult challenges in the face of market volatility and uncertainty. But the more difficult the context, the more meaningful the digital and intelligent transformation of the industry.”
Through the digital transformation journey, Shenghong has benefited. Taking the most intuitive level of plant automation for example, Bai Wei said: “the original operator daily flow, temperature, pressure of the operating habits, through the application of Honeywell’s automation, intelligent technology, to achieve the manual operation of more than 50% reduction in the frequency and improve the device self-control rate of more than 95%.” In addition, the solution “improves the device self-control rate to more than 95%, increases the propylene yield by more than 0.1%, and successfully creates a model of intelligent plant in the PDH industry.”
Enterprises can start with intelligent pilots of individual devices (such as PDH, etc.), gradually expand to enterprise-level applications and related organizational support and explore the potential of the application of technologies such as artificial intelligence and process digital twins, to increase digital capabilities. Liu Maoshu said that Honeywell has rich experience in digital transformation, one-stop totalization and automation solutions and strong local research and development team. These can tailor the operation system according to the enterprise’s characteristics, help the industry to solve the challenges faced in the process of digital transformation and ensure the smooth project delivery.
Stone Shi is executive editor-in-chief, Control Engineering China. Edited by Mark T. Hoske, content manager, Control Engineering, CFE Media and Technology, [email protected].
KEYWORDS: Digitalization, process optimization
CONSIDER THIS
Is digitalization helping design, integration and implementation of controls technologies?