Visual inspections have always been an integral part of the industrial engineering workflow. Now, advances in computer vision and frameworks like edge computing are making the inspection process even more efficient and precise.
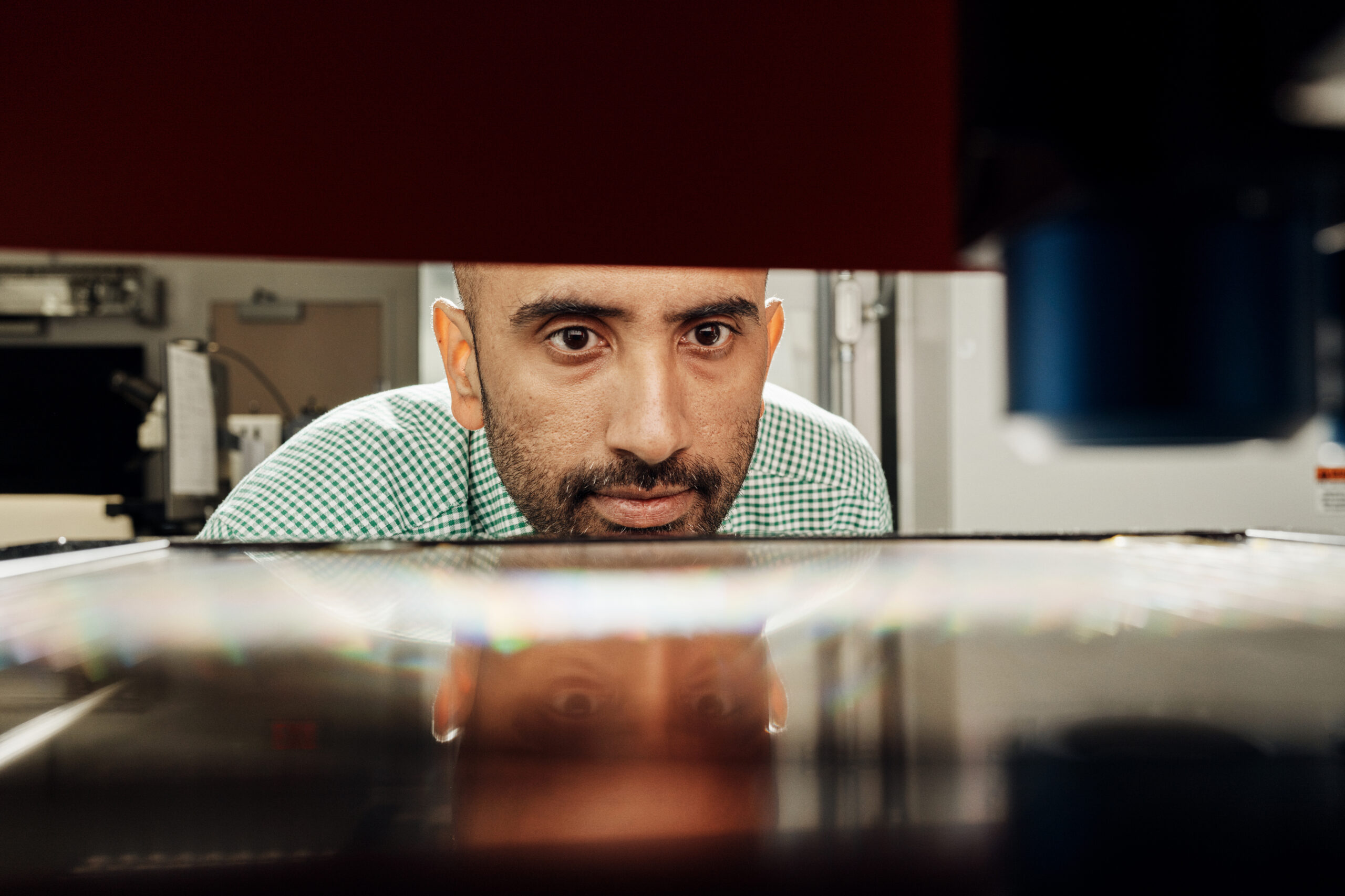
Edge computing insights
- AI and computer vision can enhance defect detection, improve quality control and make inspections more efficient.
- Edge computing enables flexible, mobile and remote inspections while improving safety and reducing latency.
- AI and edge computing streamline inspections, reduce downtime and drive smarter, faster processes in industrial applications.
Inspection has always played an outsized role in industrial engineers’ workflow. It is the critical stage that reveals whether the systems, machines and processes an engineer has been wrangling will come together to produce a high-quality output — or, alternatively, if an upstream problem is causing defects at the end of the line. The inspection stage is integral across industries, whether it is a manufacturing plant floor or public infrastructure like bridges and roads.
Visual inspection technology has evolved significantly in the digital era. It has transformed inspections from time-consuming, manual ordeals into automated processes that can “see” and report anomalies or product defects in under a second. The upshot is a better experience for businesses and consumers alike: fewer defects, less downtime and safer, higher-quality goods. Gone is the era of hand-written reports and the associated tedium and errors.
But modern inspection is not a simple binary. It is not as if processes are either manual or automated, with nothing in between. Visual inspection technology is always evolving, and what was considered innovative just one decade ago — like certain Internet of Things (IoT) tools — can quickly become dated. These days, industrial engineers who want the best-in-class inspection processes need to harness two key emerging technologies: artificial intelligence (AI) and edge computing.
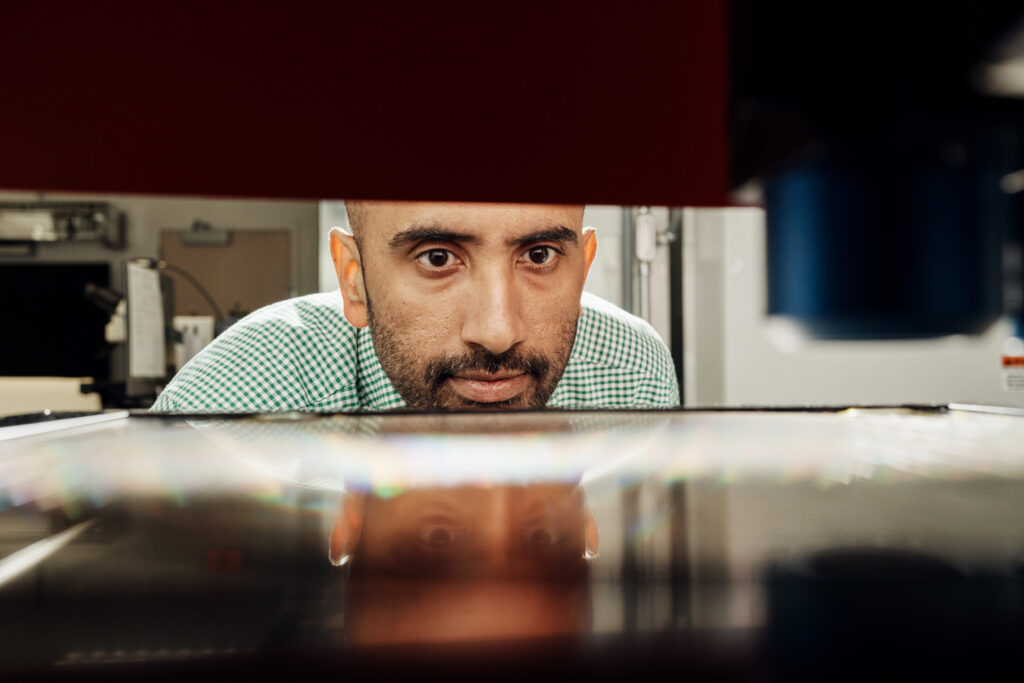
Layering AI into the inspection process
AI has been a boon for further automating and improving inspections, enabling accelerated defect detection and worker safety at scale.
One branch of AI in particular has had an outsized impact on visual inspections: computer vision, a type of machine learning that enables computers to identify and analyze objects. Computer vision does not replace human vision in the inspection process — it augments it, providing acceleration and scale. All comprehensive inspections must have a human subject matter expert “in the loop.” Computer vision makes those humans even more capable.
More manufacturers are relying on computer vision to continuously improve quality control. Software and hardware powered by computer vision allows technicians to ensure parts are in the right location; that individual components are the correct shape, color, size and texture; and that modules are not scratched, dented or otherwise damaged. These AI vision models allow meticulous inspection to occur in real time and across the production line, alerting engineers to defects immediately and enabling them to confront the problem with minimal downtime, thus saving considerable time and resources. Beyond real-time defect detection, AI tools also empower manufacturers to analyze captured defect data and uncover the root causes of recurring issues. This actionable insight enables targeted process improvements, preventing repeated defects and driving sustained enhancements in product quality.
Computer vision is also becoming easier for technicians to wield, bridging the technical skills gap. “No-code” models allow technicians to train and deploy computer vision models without having a background in computer or data science. Users can simply upload training images that inform the model without having to roll up their sleeves and wrestle with lines of code and complex algorithms.
Emerging capabilities are making this no-code training process even more seamless. IBM Research is helping equip Maximo Visual Inspection with “anomaly models,” which allow the AI to learn exclusively from images without defects, thus lowering the barrier for building models for products where defects are rare. Visual prompting allows users to build computer vision models in a matter of minutes by providing visual cues within a few example images. Once all this is done, cameras can be pointed at the production line and begin analysis.
But it is not just manufacturers who are benefiting from no-code computer vision tools. Energy and utility companies use the technology to identify metal corrosion and leaks, public works rely on it to detect cracked concrete on infrastructure and it is even being used to track and protect elephants.
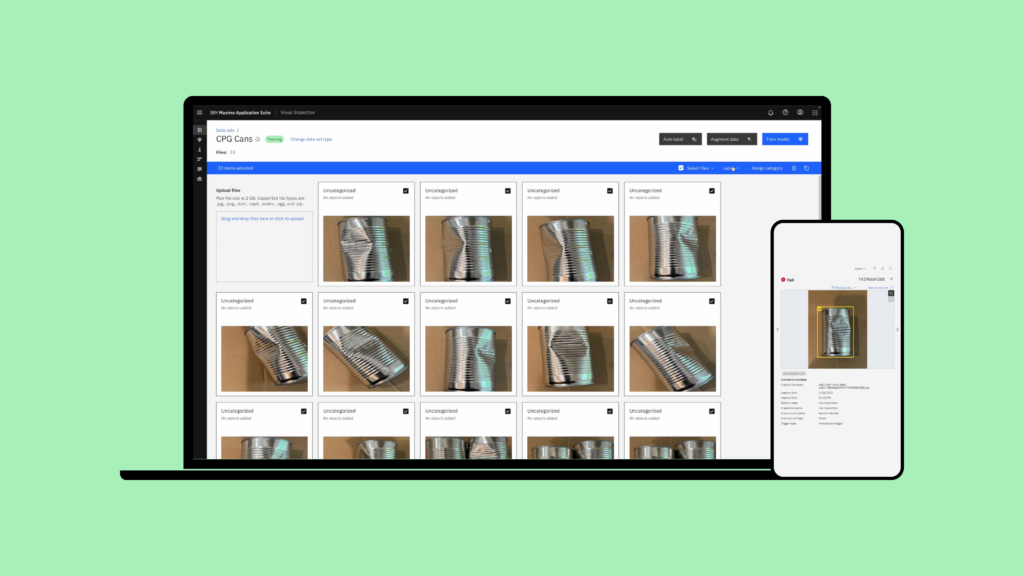
Leveraging cloud and edge computing
A high-tech inspection process is only useful if engineers can easily deploy it. Fortunately, even when computer vision requires significant processing and training data, these systems can still be used across a range of devices and locations, like smartphones on a factory floor. This is enabled by edge computing frameworks.
Workers can run visual inspection tools on their mobile devices and other lightweight hardware, unlocking flexibility and agility so that quality control can happen just about anywhere, both on-site and remotely, with limited latency. An edge approach allows AI models to run on everything from drones to high-resolution cameras to on-vehicle cameras (which are especially useful for physical infrastructure inspections). It also allows staff to easily capture images on their phones, which can then be used to further train the algorithms. Edge computing capabilities have proven invaluable to manufacturers like Ford Motor Company, who work with IBM to leverage the combination of computer vision-powered insights and edge-enabled portability for vehicle inspections.
Another benefit of edge computing is worker safety and compliance. Traditionally, humans had to physically insert themselves in the production process to carry out inspections, exposing them to dangerous machinery, chemicals and other hazardous conditions. Edge computing enables devices like drones and stand-alone cameras to serve as a proxy, allowing workers to inspect and analyze from afar — and with increased insights, not fewer.
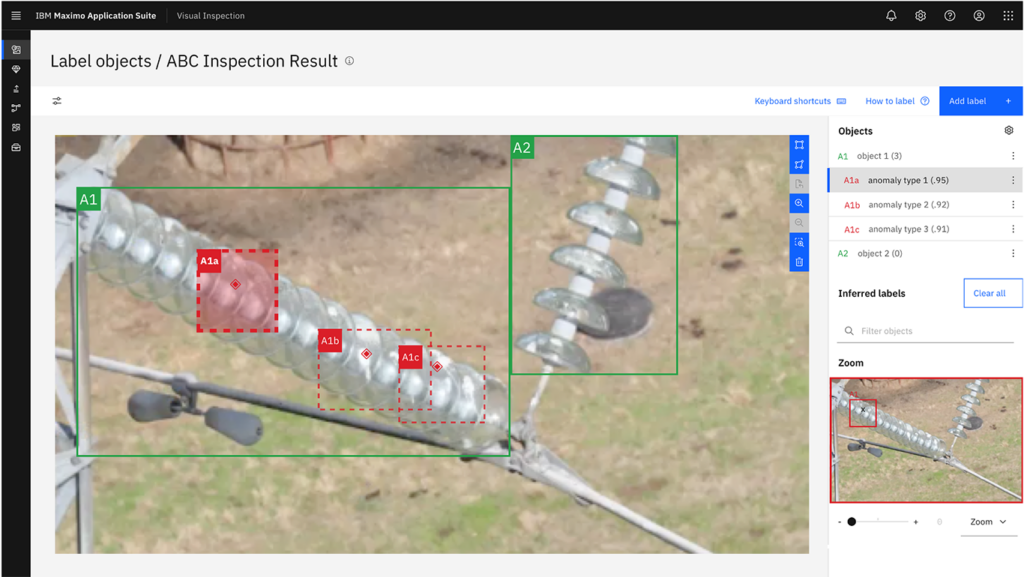
Smarter, faster inspections
Inspections are a critical part of the industrial engineering workflow, catching costly and potentially dangerous defects while also providing insight into the myriad machines, processes and systems upstream. Given their importance, inspections should always be imbued with the latest technology. Ford’s work with IBM provides a clear example. Producing millions of vehicles annually opens the potential for a range of defects and downtime, but computer-vision and edge computing provide a powerful solution. The technologies’ flexibility and low- or no-code interfaces mean inspection systems can be trained and deployed in weeks, not months.
As AI and edge computing are significantly enhancing the visual inspection process, engineers across industries should be leveraging these advancements for smarter, faster and more flexible inspections.
Kendra DeKeyrel is vice president ESG and asset management product leader, IBM; edited by Gary Cohen, senior editor, Control Engineering, WTWH Media, [email protected].
CONSIDER THIS
How can integrating AI and edge computing into inspection processes improve efficiency, quality and safety in my industry or workflow?