The next wave of industrial transformation depends on a handful of technologies.
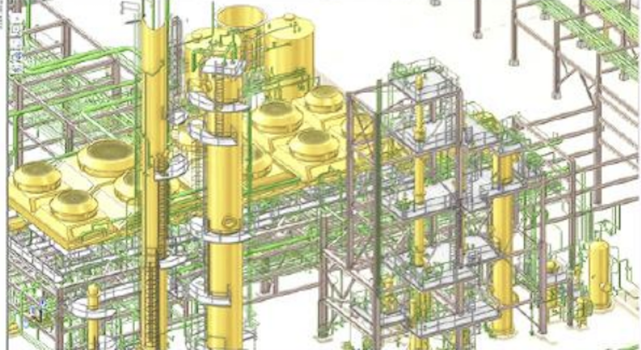
Learning Objectives
- Learn about the connected industrial ecosystem and how it can benefit enterprises through connecting disparate streams of data across their value chain.
- Discover how AI and ML are being used outside of the generative AI hype.
- Understand how cloud data ecosystems will lead to the next phase of innovation.
Industrial metaverse insights
- The industrial sector is experiencing a data explosion, with half of all industrial data created in the last two years and significant growth expected in cloud-based data storage and processing in 2024.
- Collaborative industrial cloud platforms, digital twins, and integrated data management are key to unlocking innovation and efficiency, as demonstrated by companies like HENN and Dominion Energy.
- AI analytics and the emerging industrial metaverse are set to revolutionize industrial operations by enhancing decision-making, optimizing processes and fostering real-time virtual collaboration.
The industrial world is facing a data explosion. From readouts on temperature furnaces and warehouse movements to smart meters tracking energy usage, industries have more data about a greater number of operational processes than ever before. Half of all industrial data has been created in the last two years. Estimates show that another 38% of new operational data will be stored and processed in the cloud in 2024.
Global technology spending is expected to hit $5 trillion this year. Going forward, how we collate, analyze and collectively leverage this wealth of data will shape future industrial value. And a more connected world can support responsible use of the world’s resources during an era of unprecedented disruption.
How industrial cloud platforms enhance collaboration
Businesses don’t work in isolation. The act of creating value requires connecting and collaborating with other entities.
So why don’t we connect our data streams? All too often, industrial data remains siloed within organizations. Sometimes, it even rests unsorted and unanalyzed at the point of collection.
But knowledge is power. It is only when industrial units securely share their data internally and with external partners that they can truly unlock the actionable insights needed to spark innovation and growth.
Many industrial businesses now use digital twins — interactive virtual representations of physical objects and processes — to simulate real outcomes and preview new ventures to address flaws and enhance decision making.
Companies democratize access to information, improving productivity and enhancing collaboration when access is shared to the digital twin via the cloud.
This kind of industrial-intelligence-as-a-service (IIaaS) is key to unleashing the next wave of industrial transformation.
Automotive manufacturer HENN is in the fast lane to efficiency. Using an integrated data collection application together with a scalable cloud-based data management program, the car parts manufacturer can monitor and dashboard products across dispersed assembly lines — all within a single window, anywhere. Authorized stakeholders within the company, including those at headquarters and remotely at branch offices, now have real-time insight into production lines. Issues are swiftly identified and managed, with overall efficiency gains of 10%.
Why data ecosystems are essential to growing value
What happens if we extend cloud data-sharing to external partners?
Dominion Energy in the U.S. is taking an innovative approach to stand out in the increasingly crowded renewable power sector. Dominion collates and shares real-time data from across its North American grid network with utility customers over the cloud. This enables them to provide investors, regulators and auditors with proof of their sustainable conduct. This integrated digital data highway is bringing new business to Dominion as demand for transparent and measurable reporting increases.
Dominion is an example of a new kind of connected industrial ecosystem.
In the new connected ecosystem, each entity across an industrial value chain shares a single digital source of truth. A single-window dashboard brings together data from disparate streams, such as industrial assets, suppliers and other value chain partners. When each entity can see system-wide data in context and according to its needs, it can understand the impact of its actions for its own business, on the business of every other value chain player, as well as on the ecosystem.
A centralized, scalable data infrastructure creates closer understanding and real-time collaboration. Within a connected industrial ecosystem, everyone can make better decisions, business operations become more efficient, resource use is optimized and waste minimized.
How AI analytics improve human insight
Artificial intelligence (AI) has shown that it can improve our work in very real terms. It also helps get the most from industrial data by surfacing actionable insights to maximize operational performance.
As the hype around generative AI dies down, we expect to see a broader uptake of different, more industrial AI tools over the coming months. Machine learning (ML) could become more widespread, but other types of AI will be used more prolifically. Industries are onboarding many different AI technologies, including advanced analytics and predictive asset optimization.
Advanced analytics programs can effortlessly construct and run no-code AI-driven models, simplifying how industrial workers optimize production efficiency. For example, consider that even minor process variations can greatly impact production outcomes. By crunching hundreds of variations with detailed recommendations, AI models enable operators to make confident decisions — while improving profitability and sustainability. Think ‘planet and profit’ as opposed to ‘planet vs profit.’
In the short-term, efficiency gains help reduce energy consumption and slash greenhouse gas emissions. Over the medium term, AI tools function as an engine of innovation, leading to industrial process improvements and even new value chains — by speeding the development of hydrogen as a fuel, for example.
Hill’s Pet Nutrition uses intelligent analytics to determine how variations in the manufacturing process could positively or negatively change the product. By modeling the impact of changes such as higher temperatures or water use, Hill’s can adjust manufacturing processes in real time to keep quality on track. The result? Process-to-product output is up 30% while waste is down.
Likewise, predictive asset optimization combines predictive, prescriptive, and prognostic analytics with process optimization to create a hybrid digital twin — blending both physical and simulated data to inform decisions.
With such a 360-degree view of asset health and performance, operators can identify problems earlier, establish their causes more accurately, and forecast the best possible timing to implement a solution. Operational uptime and availability are maximized, leading to better profitability and sustainability. Feeding these insights back into the design of future assets kicks off a cycle of continuous improvement.
Next, the industrial metaverse will solve real challenges
When access to real-time data and intelligent insights are democratized across the ecosystem value chain, the stage is set for the next step in industrial transformation: the industrial metaverse.
This game-changing technology is simply a way of bringing teams together virtually so they can do their jobs better. In the industrial metaverse, people collaborate virtually around a real-time representation of physical assets, with live data and analytics available on command.
The industrial metaverse will be a layer of collaboration on top of a digital twin — with industrial AI in the complementary role of assistant, bringing sharper and more accurate insights to human decision makers.
The industrial metaverse is simply a logical extension of industrial companies’ existing technology investments. Clearly, it’s one that offers closer interactions and uses industrial data to spark innovation and drive new value. Think of it as the smartest way to turn those growing volumes of data into sustainable returns.
It is only when industrial entities share their data with internal and external partners that they can truly capitalize on the competitive insights required to drive the next wave of sustainable growth — even in disruptive times.
Rob McGreevy is the chief product officer at AVEVA. Edited by Tyler Wall, associate editor, Control Engineering, WTWH Media, [email protected].
KEYWORDS: Industrial metaverse, industrial data, artificial intelligenceÂ
CONSIDER THIS
How is the metaverse changing how you approach manufacturing?