5G can help transform smart manufacturing and help improve their information and data flow and connect many devices easily. Five ways 5G enhances smart manufacturing are highlighted.
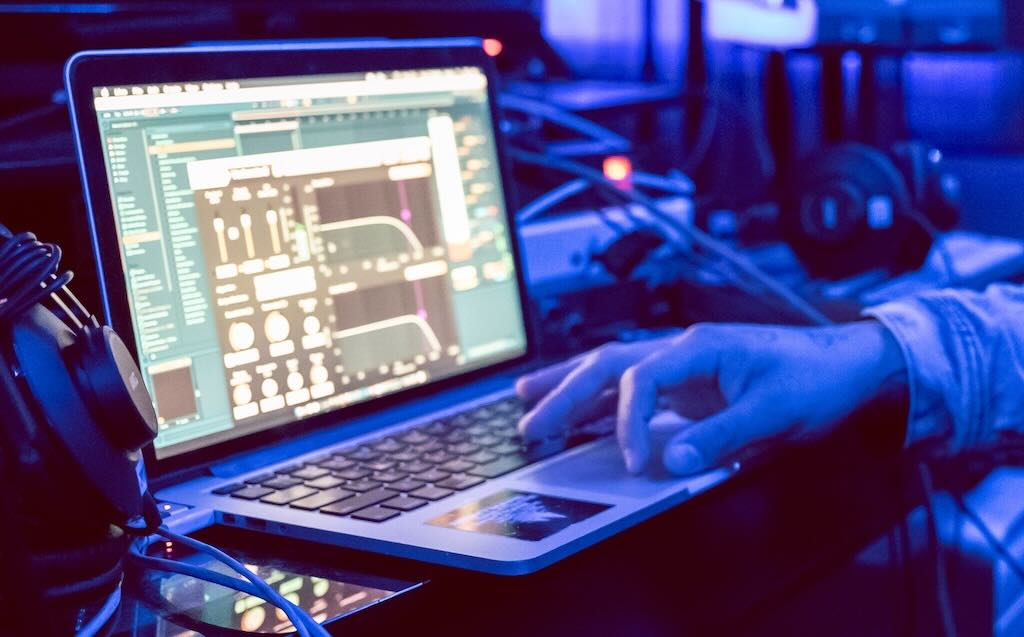
Learning Objectives
- Understanding how smart manufacturing and 5G are becoming more important in manufacturing.
- Learn about 5G’s benefits for manufacturers and how it improves data and information flow.
- See five benefits manufacturers gain from incorporating 5G into their smart manufacturing processes.
5G and smart manufacturing insights
- Integrating 5G in manufacturing enables real-time data analysis, improving decision-making and operational efficiency by enhancing connectivity and reducing latency across devices.
- 5G technology supports predictive maintenance and smarter automation, leading to increased productivity and quality control in manufacturing through advanced, high-speed data transfers.
Data production has exploded over the past few years in the manufacturing industry. According to the McKinsey Global Institute, the manufacturing industry generates 1.9 petabytes of data per year, outpacing several other data-rich fields.
Data’s value hinges on an organization’s ability to unlock and execute actionable insights. This requires the swift transfer of data between devices and locations. Manufacturing is no different. Its reliance on accurate and immediate data is critical to the industry’s operational success.
Manufacturers report their greatest challenge in facility analytics include the ease of integrating data from multiple sources and the volume of data collected across systems and equipment. Industry experts recognize managing the disconnect and volume of information generated in the industry is dependent on network infrastructure. Current legacy systems of wired communications and previous iterations of cellular networks are unable to handle the current bandwidth of devices, leading to increased latency which affects agility and productivity across operations.
The ability to quickly integrate data, assess outcomes and leverage advanced technology is critical to the field of manufacturing. Without stability across systems and devices, overcoming latency and connectivity issues, organizations fail to capitalize on sensitive data affecting productivity and subsequent business outcomes.
5G networks enhance connectivity
The need for actionable and accessible data has led manufacturers to increasingly rely on the fifth generation of wireless network technology, also known as 5G. Providing broader access to data, previously harbored in silos or disparate systems across the plant floor, 5G improves connectivity and productivity while enabling the use of predictive, prescriptive and adaptive technologies.
There is a growing need for quick, reliable information transfer is crucial to support the growing use of Internet of Things (IoT) and non-IoT devices. 5G provides these diverse sources with the infrastructure required to facilitate communication between hundreds to thousands of devices used throughout the factory.
Besides improved communications across devices, 5G also increases speed and volume of data transmission. 5G’s ability to provide high-speed, low-latency and reliable communications is an essential factor in successful manufacturing operations. Not only the speed of communication, but the size of communication transfer is paramount to 5G’s benefits.
This is especially true in the manufacturing industry, providing rapid and dependable large-scale data transfers is essential to fostering agility and productivity. With 5G’s near-zero latency and cloud capabilities, manufacturing organizations are providing real-time information that improves data analysis and decision-making.
Furthermore, 5G alleviates the need for wired connectivity, increasing flexibility and productivity. It enables remote monitoring and access to various devices and allows smart manufacturing practices to reach even remote locations, fostering wider adoption and innovation.
Five ways 5G enhances smart manufacturing
The use of IoT devices has expanded rapidly over the past few years, though their existence in the industry spans the past several decades. The manufacturing industry, already heavily reliant upon these devices, is primed for increased data generation and transmission. In fact, forecasts predict there will be about 56 billion IoT devices globally, capable of generating almost 90 zettabytes of data by 2025.
As IoT adoption rate increases, the manufacturing industry has the challenge of integrating vast amounts of technology and information. Without the proper network layer, providing the connectivity and agility needed to communicate across these devices, their potential is quickly rendered useless.
With 5G, manufacturers are capable of transmitting this data, collected across devices, at a rate 100x faster than its predecessor. By coupling the speed and size of data transmission through 5G networks with IoT devices, organizations can improve decision-making and performance. For example, 5G improves the productivity of smart manufacturing processes through the following capabilities:
-
Predictive maintenance: 5G’s data transfer speeds allow manufacturers to analyze sensor data in real-time, enabling them to predict equipment failures and schedule maintenance proactively. This remote monitoring also provides a clear picture of machine health and production output.
-
Predictive and prescriptive quality: 5G empowers remote factory oversight with high-efficiency monitoring. This allows for improved quality control by tracking production lines and performing remote inspections seamlessly by leveraging sensor data. Resulting in prescriptive insights based on real-time data sourced from environmental, product, process and people-oriented data.
-
Smarter automation: Building a smart factory requires digitizing all processes and enabling greater automation with adaptive capabilities within the facility. 5G serves as the communication backbone that unlocks these automation possibilities.
-
Real-time robotics control: By enabling automation with ultra-low latency, 5G empowers manufacturers to achieve increased flexibility and precision in managing their operations from any location.
-
Precision tracking and monitoring: 5G’s high-speed data transfers significantly enhance track-and-trace capabilities and remote monitoring. This allows for better visibility into production processes and real-time data for informed decision-making.
5G is a communication method that catalyzes a fundamental shift in the industry’s approach to manufacturing. This network enables increased visibility over key production processes, allowing manufacturers to capitalize on access to real-time information. Increasing the flow of information between devices improves flexibility across the factory floor and leads to improved productivity and quality.
Business outcomes and external benefits
Increased agility and productivity as a result of this implementation provides faster time to market and greater efficiency regarding end-product output. Manufacturers recognize the value of 5G as an enabler of improved, accessible data insights and increasingly understand the business value this network offers. For example, a recent report indicated manufacturers see 5G as one of the top technologies that has provided the biggest return on investment (ROI) over the past 12 months. Another survey indicates 90% of manufacturers report 5G connectivity will be important to the overall future of their business.
Beyond manufacturing operations, 5G carries the potential to increase efficiency and connectivity across the supply chain. 5G’s ability to seamlessly share data enables applications like track and trace to communicate live location updates and reliable tracking information to stakeholders across the supply chain. Providing real-time updates that increase visibility and resiliency offers another layer of support to the wider supply chain ecosystem.
5G serves as a catalyst for fundamental transformation in the manufacturing industry. It provides a network that enables smart manufacturing solutions to maximize performance via ultra-low latency, high speed data transfer and large data capacity. Combining 5G with smart manufacturing operations transforms manufacturing facilities into an intelligent ecosystem capable of ingesting, analyzing and applying large amounts of data that provides valuable and actionable insights.
Anthony Murphy is vice president and head of product management for Plex. Edited by Chris Vavra, senior editor, Control Engineering, WTWH Media, [email protected].