Industrial networking is vital to today’s manufacturing landscape. From different types of networks to key components and best practices, this guide will help you navigate the intricacies of industrial Ethernet networking. See video.
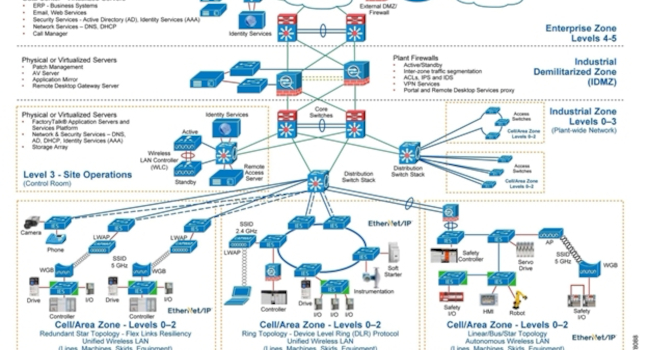
Learning Objectives
- Discover common technologies and protocols used in ICS plant floor networking.
- Learn about the benefits of proper industrial networking implementations.
- Explore best practices for industrial network design.
Industrial networking insights
-
Modern Industrial Ethernet networks are essential for driving efficiency and productivity within manufacturing facilities.
-
Common technologies and protocols used in ICS plant floor networking include:Ethernet/IP, PROFINET, Modbus TCP/IP, DeviceNet, CIP (Common Industrial Protocol), and PTP (Precision Time Protocol).
-
Three use-cases provide examples of best practices for industrial network design.
What is industrial networking?
Industrial networking refers to the interconnected infrastructure of devices and systems used for seamless data communication and control in industrial environments. It enables efficient automation, monitoring and optimization of industrial processes, alongside the sensitivity of protocols that are required to maintain consistent communication amongst devices without interruption. The majority of this communication is millisecond dependent, and some is even microsecond dependent.
See video for additional insights about industrial networking from Nick Roe.
Importance of industrial networking
Modern Industrial Ethernet networks are essential for driving efficiency and productivity within manufacturing facilities. It allows for real-time monitoring and control of equipment, enables predictive maintenance and facilitates data-driven decision-making. Having a reliable and stable industrial network is vital to any organization; it is the backbone or foundation to all operations, whether that entails implementing a thin client solution, engaging in data collection, operating an industrial software solution or even expanding an existing facility.
For example, one would not want to build a house without a solid and reliable foundation. The additional weight of the floors above would lead the home to before it was even completed.
Industrial control system networking
Industrial control system (ICS) networking refers to the Ethernet network infrastructure and protocols used specifically for connecting and supporting industrial control systems on the plant floor. These control systems are responsible for controlling and monitoring various processes and equipment in manufacturing plants.
The goal of ICS plant floor networking is to provide reliable and secure communication infrastructure that ensures smooth and efficient operation of industrial processes. It involves the use of specialized networking technologies and protocols designed to meet the unique requirements of industrial environments, such as high reliability, determinism and real-time communication.
Some common technologies and protocols used in ICS plant floor networking include:
-
Ethernet/IP
-
PROFINET
-
Modbus TCP/IP
-
DeviceNet
-
CIP (Common Industrial Protocol)
-
PTP (Precision Time Protocol).
By implementing robust and secure plant floor networking technologies, industrial organizations can optimize their operations, improve productivity and ensure the safety and reliability of their manufacturing processes.
Types of industrial networks
Ethernet/IP: Utilizes standard Ethernet technology for high-speed communication and seamless integration with devices.
PROFINET: A powerful, open Industrial Ethernet standard providing real-time communication and flexibility.
Modbus TCP/IP: A widely used protocol for connecting industrial devices over Ethernet.
DeviceNet: An industrial network protocol designed for connecting simple devices and sensors in a network.
Components of industrial networks
PLCs (programmable logic controllers): Powerful industrial computers that control and automate various processes in manufacturing.
HMI (human machine interface): Graphical interfaces that allow operators to monitor and interact with industrial machinery and systems.
SCADA (supervisory control and data acquisition): Control systems that gather and analyze real-time data from industrial processes for monitoring and control.
Industrial ethernet switches: Specialized switches for industrial environments that provide reliable and efficient network connectivity.
Industrial Ethernet cabling: Whether it is fiber or copper, the horizontal and structured network cabling, patch panels and patch cables provide that provide the passive network infrastructure for a reliable system.
Benefits of industrial networking
Improved productivity: Streamlined operations and efficient communication result in increased productivity and output.
Reduced downtime: Proactive monitoring and predictive maintenance minimize unplanned downtime.
Enhanced communication and data sharing: Real-time data sharing between devices and systems enables better collaboration and informed decision-making.
Best practices for industrial network design
Network segmentation: Dividing the network into logical segments ensures stability, security and proper traffic management.
Redundancy and fault tolerance: Implementing backup systems and redundant paths to minimize the impact of failures.
Security measures: Robust cybersecurity protocols and strategies to protect networks and sensitive industrial data from threats. Use a defense-in-depth approach to align with industrial security standards such as IEC-62443 (formerly ISA99) Industrial Automation and Control Systems (IACS) Security and NIST 800-82 Industrial Control System (ICS) Security.
Cisco and Rockwell Automation CPwE model: Converged Plantwide Ethernet (CPwE) includes comprehensive network architectures developed by Cisco and Rockwell Automation. It provides a scalable and secure network infrastructure guide for industrial applications, integrating various automation and control systems. CPwE incorporates the best practices mentioned above, along with additional guidelines specific to Rockwell Automation products and technologies.
Examples of industrial network implementations
Here are a few examples of industrial networks the challenges and benefits they offer for industrial automation systems. From the oil and gas industry to pharmaceuticals, automotive, and food and beverage, these are real-life design scenarios that have been actualized. From streamlined network infrastructure to improved scalability and security, modern industrial network best practices are revolutionizing the way industries operate.
Automotive manufacturing: Industrial networks are widely used in automotive manufacturing plants to integrate different systems and devices, such as robots, conveyors and quality control systems. It ensures seamless communication and coordination between these components, improving overall efficiency and productivity.
Food and beverage industry: Industrial networks are implemented in food and beverage production facilities to connect various equipment, such as mixing machines, packaging lines and quality inspection systems. This enables real-time monitoring and control, enhancing product quality and safety.
Oil and gas sector: Industrial networks are utilized in oil and gas refineries and production facilities to integrate critical systems, including pumps, valves and safety devices. It enables efficient monitoring, control and optimization of these processes, ensuring safe and reliable operations.
Design example 1: Industrial ethernet network for the oil and gas industry
The challenge: Oil and gas operations require resilient and highly secure communication networks to ensure smooth production and safety.
The solution: Design a secure, scalable and reliable Ethernet network infrastructure using redundant devices and cabling paths that supports critical communication and control systems.
The benefits: Improved operational efficiency, enhanced safety,and reduced downtime contribute to increased profitability for oil and gas companies.
Design example 2: Industrial ethernet network for the pharmaceutical industry
The challenge: Pharmaceutical facilities struggle with network complexity and the need to comply with strict regulatory requirements.
The solution: Design a physically secure network architecture, with sophisticated monitoring capabilities, and verifiable change control to ensure compliance with industry regulations like FDA 21 CFR Part 11.
The benefits: Improved data integrity, simplified network management and enhanced regulatory compliance elevate pharmaceutical companies’ operational efficiency.
Design example 3: Industrial ethernet network for the automotive industry
Efficient production processes: Industrial Ethernet networks enable seamless integration of manufacturing systems, optimizing production efficiency and reducing costs.
Real-time operational insights: Industrial Ethernet networks empower automotive manufacturers to collect data from OEM equipment and production lines with valuable insights for better decision-making.
Scalability for future growth: Modern Industrial Ethernet networks accommodate the evolving needs of the automotive industry, allowing for easy integration of new technologies and systems.
Key takeaways from Industrial Ethernet network design examples
Unleash operational efficiency: Industrial Ethernet networks empower businesses to optimize their operations, reduce downtime and enhance productivity.
Enhance network security: Industrial Ethernet networks allow for robust cybersecurity measures to be put in place to protect critical industrial systems from potential threats.
Enable scalability and future-proofing: Industrial Ethernet networks allow for easy integration of new technologies and adaptability to evolving industry demands.
Differences between enterprise networking and industrial networking
Enterprise Networking refers to the networking infrastructure and systems used by businesses and organizations for their internal communication and data exchange. It typically involves connecting office devices, such as computers, printers and servers to provide access to shared resources and services.
On the other hand, industrial networking focuses on networking solutions specifically designed for industrial environments such as manufacturing plants, oil refineries and power generation facilities. Industrial networks are built to support the unique requirements of industrial automation and control systems, including real-time communication, reliability and cybersecurity.
While both enterprise networking and industrial networking share some common networking principles such as network segmentation and security measures, industrial networking places a greater emphasis on factors like determinism, robustness and compatibility with industrial protocols and standards.
Industrial networks often require specialized networking equipment and technologies that can handle the harsh conditions and stringent demands of industrial applications, such as high temperatures, electrical noise and mission-critical operations.
By adopting best practices for industrial network design, organizations can ensure the availability, integrity and security of their industrial networks, enabling smooth operation of critical industrial processes and systems.
Conclusion
Industrial networking is the backbone of modern manufacturing, enabling efficient operations, real-time monitoring and data-driven decision-making. By understanding these types, components and best practices, you can harness the power of industrial networking to optimize productivity and drive success in your organization.
Nick Roe, senior engineer, Matrix Technologies, a CFE Media and Technology content partner. He can be reached at [email protected]. Edited by David Miller, content manager, Control Engineering, CFE Media and Technology, [email protected].
CONSIDER THIS
How can you implement these industrial networking best practices in your facility?