An enterprise operations platform evolved from the control system unlocks a more effective, efficient and future-proofed automation stack.
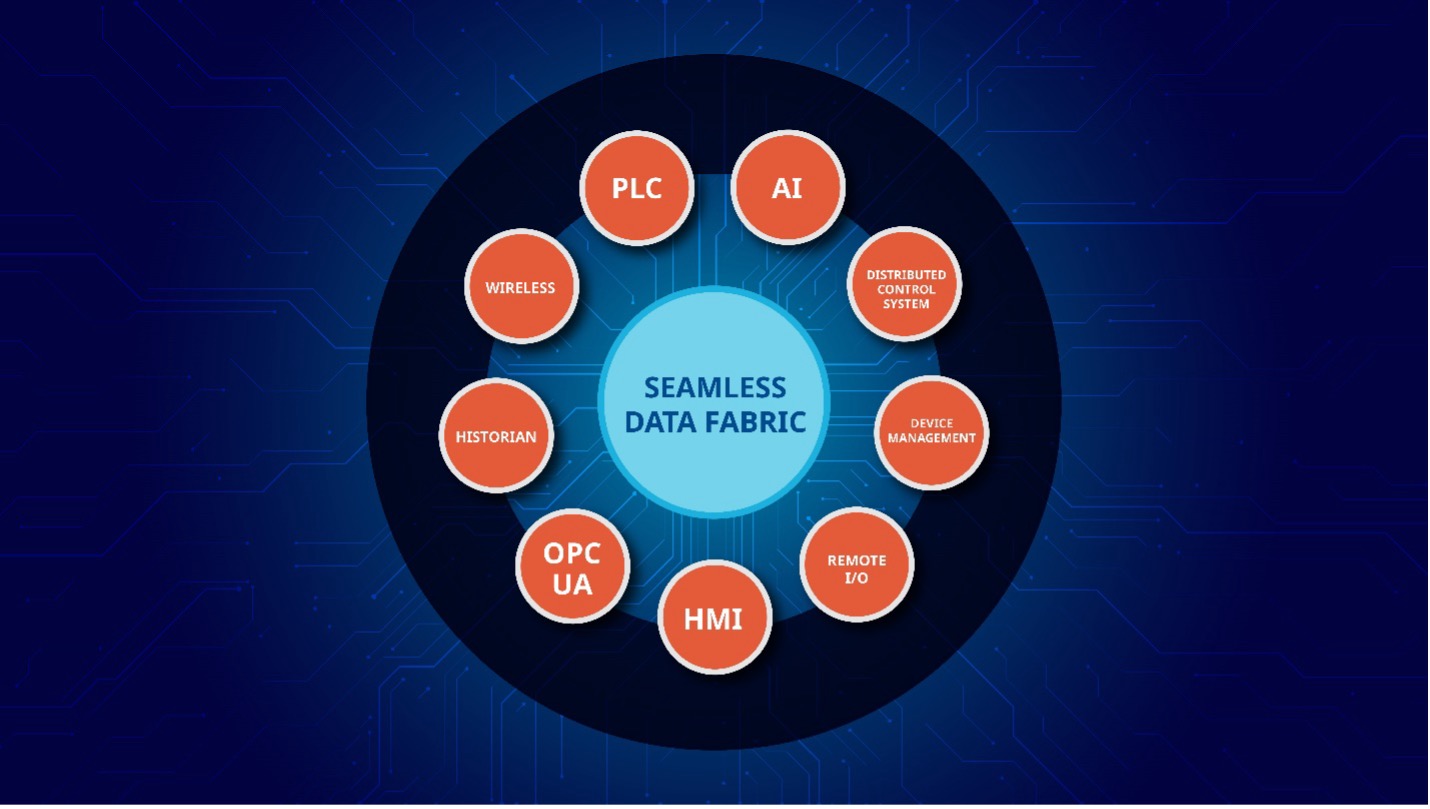
Control system insights
- Automation solution providers and process manufacturers need to develop enterprise operations platforms that enable data handling across a wide array of applications.
- A system-of-systems approach is incredibly difficult to scale.
- An enterprise operations platform is an ideal path to a futureproofed automation stack, especially if it is developed as an evolution of the distributed control system.
Most process manufacturers have approached automation in the same way for decades. Following the Purdue Model, implementation teams have isolated the control system on its own layers. The control layers were built, updated and maintained for purpose, with little to no interaction with other layers of operations.
In isolation, the distributed control system (DCS) performed its role reliably, but if it could be elevated to a platform that brings together all functionality required to automate industrial operations, it could become the key component of a future-proofed operation.
As industrial process operations have evolved — particularly in the last decade — many organizations have seen their current strategy stall their ability to digitally transform operations. When isolated, the DCS does not scale well, nor does it pair as well as it could with other critical automation solutions.
Moving beyond distributed control systems (DCS)
Implementing new technologies and strategies requires either breaking into the control layer or finding a way to push data out of that layer to other systems and solutions. It can be done, but it takes lots of time and money, as well as a deep bench of dedicated, expert personnel to engineer and maintain the automation system.
This increasing complexity has brought the DCS to an inflection point. As new automation innovations continue to emerge, with an increasing need to consume data from across the automation stack, automation solution providers and process manufacturers alike have discovered a need to develop enterprise operations platforms that enable data handling across a wide array of applications.
Ultimately, there are two primary ways to implement such a platform: as a system of systems with each component connected to each other in a web of interfaces and protocols or by evolving the DCS itself into the enterprise operations platform.
Why organizations implement a system-of-systems approach
Today, many organizations follow the system-of-systems approach to developing an enterprise operations platform. These teams select efficient and cost-effective solutions for each automation function and integrate them after the fact. Modern protocols such as Open Platform Communication Unified Architecture (OPC UA), Message Queuing Telemetry Transport (MQTT) and more have made this easier to accomplish in recent years.
This solution, although feasible, comes with several drawbacks. Such systems can be tremendously difficult to scale. When an engineer makes a change to the DCS — adding a new sensor, replacing or upgrading equipment, implementing new alarms and alerts, etc. — those changes have cascading effects across the system of systems. The engineer may need to reconfigure OPC UA, adjust alarm management, reconfigure a connection to the historian, update asset models to account for new parameters and perform other time-consuming tasks.
In many cases, engineering teams don’t feel the changes are worth the additional work, so unless organizations are highly motivated to continuously digitally transform their operations, system-of-system solutions often stagnate for years or decades. Moreover, even if teams stay on top of their changes, the data coming out of the DCS for use in other systems is often low- or no-context data. Therefore, teams need to do even more manual work in the individual systems to rebuild context and make the data useful.
Moving beyond a system-of-systems approach
In contrast to the system-of-systems approach, an emerging strategy for building an enterprise operations platform is evolving the already natively integrated DCS itself to create a more efficient solution. When the control system evolves into a seamlessly integrated operations platform, its functionality shifts. Process control is simply a single function of the overall platform, as are advanced control, data historization, alarm and event management, reliability, data analytics, safety, compressor controls and more. Instead of being focused entirely on process control, the center of the enterprise operations platform is data integrity, availability and security (see Figure 1).
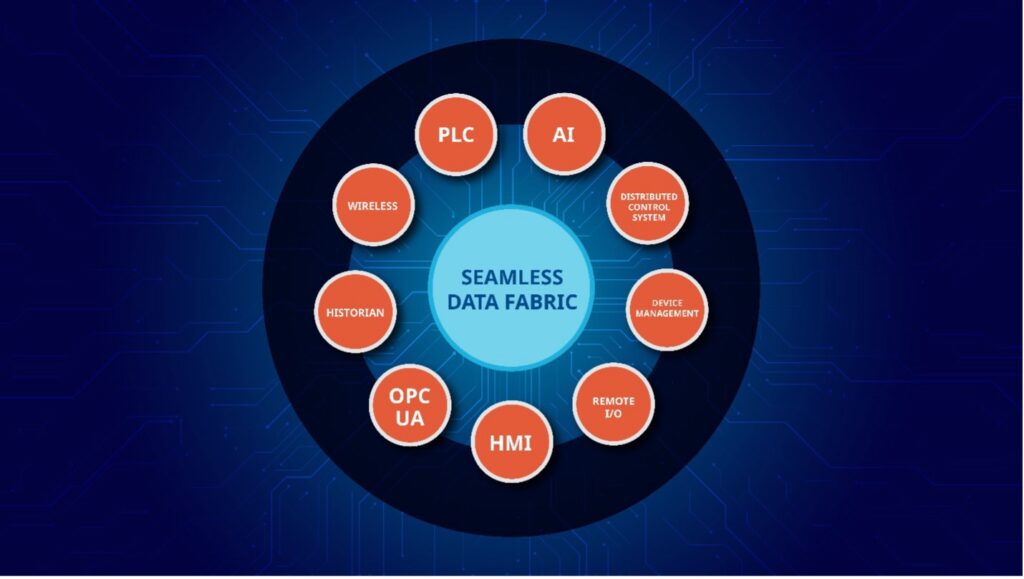
Such a system offers more seamless integration and easier management. The DCS — the largest container of data in the automation platform — is positioned to be seamlessly integrated with all other automation solutions as they are added. New solutions will connect out of the box, with data moving efficiently and effortlessly between them. With a built-for-purpose enterprise operations platform evolved from the DCS, context is preserved as data moves from one system to another. Critical information can be consumed at every level and then used to generate actionable insights for innovation, maintenance, efficiency and sustainability improvements and more.
The benefits of an integrated automation approach
Moreover, because the systems are seamlessly integrated, a single change anywhere in the operations platform does not require hours of engineering effort to maintain integration. Solutions designed as part of the platform are integrated out of the box and changes will seamlessly cascade across the environment as part of its core functionality.
This new approach will also need to account for connecting legacy automation to the new enterprise operations platform to protect existing investments. This integration will likely still require some custom engineering, potentially aided by AI agents, as such solutions were not designed with seamless automation integration in mind.
However, once that process is complete, replacing old technologies (and adding new ones) with modern technology will no longer require replacement of the core automation infrastructure. Instead, new technologies will simply be add-ons and seamlessly integrated into the enterprise operations platform stack.
An enterprise operations platform as a futureproof solution
As organizations modernize their automation stack to pave the way for new technologies like artificial intelligence (AI), Ethernet-Advanced Physical Layer (APL) and more, they are looking at ways to future-proof their investments. Ideally, these efforts would capture the benefits of the newest technologies, while eliminating the need to rip and replace infrastructure as new, critical solutions emerge. The enterprise operations platform is an ideal path to that futureproofed automation stack, especially if it is developed as an evolution of the DCS.
While the traditional system-of-systems approach to platform design will continue to work, it will increasingly show its limitations as new technologies become critical enablers of competitive advantage. A platform evolved from the DCS will continue to evolve, providing teams with more integration and efficiency and, most importantly, increased operational excellence, all with far less engineering effort.
Claudio Fayad is the vice president of technology of Emerson’s Process Systems and Solutions business. Edited by Sheri Kasprzak, managing editor of Automation & Controls, WTWH Media, [email protected].