Programmable logic controllers (PLCs) and distributed control systems (DCSs) play an important role in industrial automation facilities, serving different purposes and offering distinct advantages.
Data collection and distribution insights
- Programmable logic controllers (PLCs) and distributed control systems (DCSs) play an important role in industrial automation facilities, serving different purposes and offering distinct advantages.
- Accessing data collected and historized from various systems adds value and improves operational efficiencies across the enterprise.
- Logistics benefit from improved efficiency through optimized process flow and better inventory management, driven by precise operational data.
The term big data was coined several decades ago, but its impact is still felt in manufacturing facilities today. Data provides valuable operational feedback that helps decision makers determine changes or adjustments they must make to confirm processes run at peak performance, all while delivering the desired business outcomes. They use this data to gain insight into various areas of a facility, such as:
- Logistics to control inventory of raw materials, finished goods and utility usage
- Predictive and preventive maintenance scheduling
- Managing the effects on quality, safety and the environment
Data comes from many sources as manufacturing equipment is outfitted with various types of sensors and devices. As data-collection systems mature and more processes receive controllers, the amount and types of data increase (see Table 1).
Specifically, process and production data has increased greatly over the last 20 years. Due to technological advances, inline instrumentation has improved over time to the point of unprecedented reliability and accuracy.
Table 1. A sample list of data types.
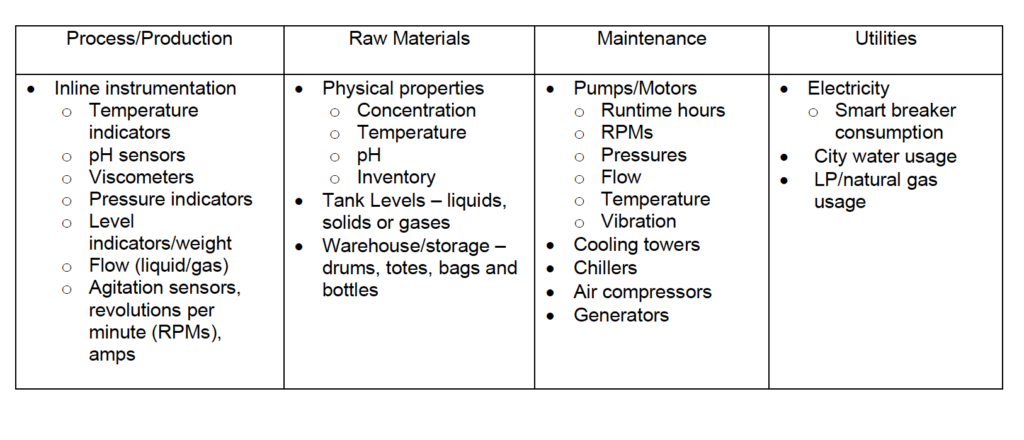
Current data sources, however, are no longer bound to one source, which makes data collection challenging. While some data-collection processes are more complicated than others, they still deliver the required data. Transferring process automation data from numerous control system sources and writing it to data historians requires connectivity via data communication interfaces.
Data communication through a system’s network infrastructure – wired (Ethernet) and wireless (Wi-Fi or cellular) – helps with data transfer using numerous communication protocol interfaces. Object linking and embedding (OLE) for Process Control (OPC), Modbus, PROFIBUS and Message Queuing Telemetry Transport (MQTT) can achieve reliable and standardized data transfer between devices and systems.
How to achieve real-time data access with PLCs and DCSs
The distributed control system (DCS), programmable logic controller (PLC) and supervisory control and data acquisition (SCADA) system help capture and share data in real time from the various processes across the system network. The mission-critical data extracted from these systems is stored in a process data historian, such as Rockwell Automation’s FactoryTalk software.
Data historians enhance the different areas of manufacturing operations. As a specialized software, historians are designed to store and manage vast amounts of time-series data. Using a unified platform with various tools to help capture, collect, visualize and analyze the stored data helps manufacturing workers overcome many data-collection processing challenges.
The PLCs and DCSs are critical in industrial automation facilities, but they serve different purposes and offer distinct advantages. While PLCs are highly effective for discrete control tasks and smaller applications, the DCS excels in large-scale, complex and continuous process environments and is a common platform to use for data collection and distribution.
A DCS can run on the same platform as power, variable frequency drives and motor control centers. Batch and continuous process operations can also run on a common platform.
Consider the following advantages that make a DCS, such as Rockwell Automation’s PlantPAx, well-suited for a coordinated way to collect, contextualize and distribute data across the enterprise in industries such as oil and gas, chemical processing, power generation and more.
The advantages of DCS in data collection
There are some distinct advantages to using a DCS in data collection across a unified platform.
Scalable and integrated design
Designed to handle large-scale processes with many control loops and devices, a DCS is inherently scalable, making it easier to expand and integrate additional components without significant system redesign. It integrates control, monitoring and data acquisition into a unified platform, providing a seamless interface for managing complex processes. This integration simplifies system architecture and reduces the need for multiple disparate systems.
Centralized control
Providing a centralized control platform, a DCS helps operators monitor and control the process from one interface. It synchronizes all parts of the process and ensures they operate consistently, crucial for processes that require tight coordination and timing. This centralization enhances situational awareness as workers can access real-time data, which makes it easier to manage alarms and respond to large and complex processing needs.
Advanced process control capabilities
The DCS supports advanced control algorithms and strategies, such as model predictive control, adaptive control and multivariable control. These capabilities are essential for optimizing complex processes and improving efficiency. In addition, a DCS is equipped with tools for process optimization, allowing for real-time adjustments based on process conditions and performance metrics. These features lead to improved quality control and resource utilization.
Reliability and redundancy
With built-in redundancy for critical components like controllers, power supplies and communication networks, the DCS delivers high system availability and reliability, minimizing downtime and production losses. It’s also designed to handle faults gracefully, with features like automatic failover and fault-tolerant communication, making it more resilient to failures.
Simplified maintenance
The centralized nature of a DCS simplifies maintenance activities. Providing comprehensive diagnostic tools and real-time monitoring, a DCS helps identify and troubleshoot issues.
Lifecycle management
Typically, the DCS comes with extensive support for system lifecycle management, including regular updates, upgrades and long-term support to ensure the system remains up-to-date and functional over its lifespan.
Enhanced HMI, visualization and customizable dashboards
The DCS provides sophisticated human-machine interface (HMI) tools that offer detailed process visualization, trend analysis and alarm management. These tools enhance operator effectiveness and decision-making. Operators can create customizable dashboards to monitor key performance indicators and process variables, providing increased insight into process performance and enabling proactive data management.
Comprehensive data management
The DCS often includes integrated data historians for long-term data storage and analysis. This feature facilitates detailed process analysis, reporting and regulatory compliance. It also provides easy access to real-time and historical process data, enabling thorough analysis and continuous improvement efforts.
Data collection’s pivotal role in various systems
Accessing data collected and historized from various systems, such as a DCS, PLCs and SCADA, on a unified platform adds value and improves operational efficiencies across the enterprise. Making this data available to the right people is key for manufacturing processes.
In maintenance management, for example, real-time monitoring and historical data analysis enables predictive maintenance strategies, reducing downtime and extending equipment lifespan (see Figure 1). It also helps identify and mitigate potential hazards for a safer work environment.

Continuous data collection helps manufacturers achieve consistent product quality control by enabling real-time adjustments and thorough post-production analysis. Logistics benefit from improved efficiency through optimized process flow and better inventory management, driven by precise operational data.
While today’s real-time data is accessible across many disparate platforms via the use of interfaces and connectors, a unified platform makes the data collection, analysis and visualization processes easier, and decision-making is enhanced. Manufacturing leaders can use this detailed, accurate data to make informed decisions that drive operational excellence and strategic growth. Overall, integrating real-time system data into critical areas fosters a resilient and agile culture of continuous improvement and operational efficiency.
Brian Bolton is a senior process engineer at Rockwell Automation. Edited by Sheri Kasprzak, managing editor, Automation & Controls, WTWH Media, [email protected].