ARC Industry Leadership Forum, 2025: ExxonMobil runs Open Process Automation (OPA) system in a large-scale Lighthouse Project, with a 1000 I/O and 100 controllers at a resin finishing plant in Baton Rouge, providing reliable interoperability, without glitches.
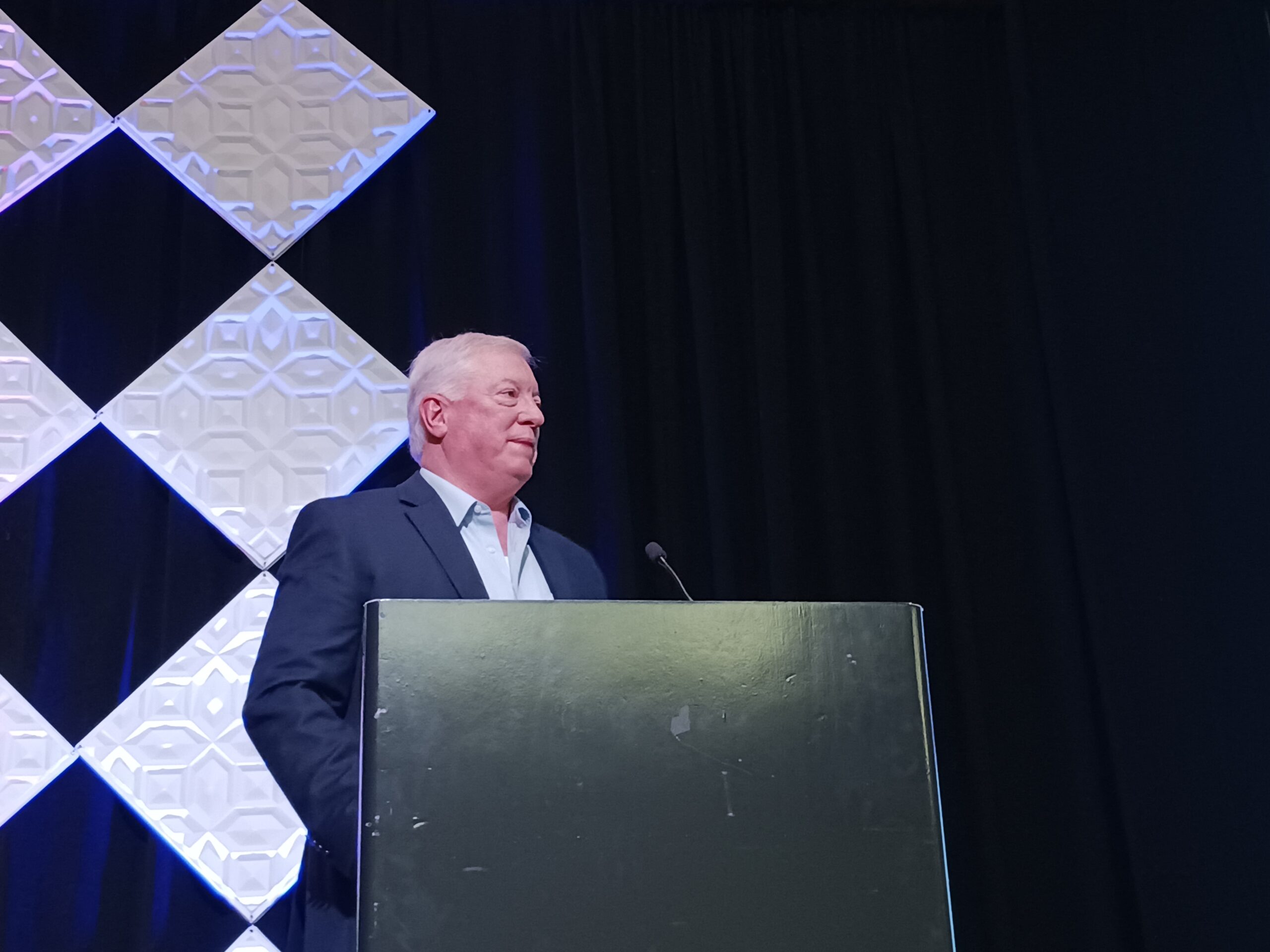
ExxonMobil OPA-S Lighthouse Project insights
- Open Process Automation (OPA) ExxonMobil Lighthouse Project, 100 controller, 1000 I/O project, architecture, migration, startup and benefits were described at the ARC Industry Leadership Forum.
- OPA ExxonMobil Lighthouse Project participants discuss architecture, and compare to migrating a distributed control system (DCS).
- Additional OPA information, timelines and artificial intelligence (AI) integration was discussed.
A new ground-up process control system is operating with more than 100 controllers and 1000 input/output (I/O) points at the ExxonMobil Resins Finishing Plant in Baton Rouge, Louisiana, using the Open Process Automation Standard (O-PAS), as described at the 2025 ARC Industry Leadership Forum by ARC Advisory Group. The open architecture, standards-based system and its hardware and software components are “replaceable, interchangeable and interoperable,” said David DeBari, R&D team leader, ExxonMobil (Figure 1), followed by substantial spontaneous audience applause. Ideas for the effort emerged 16 years ago, and the first OPA prototype and test bed was five years ago (Figure 2).
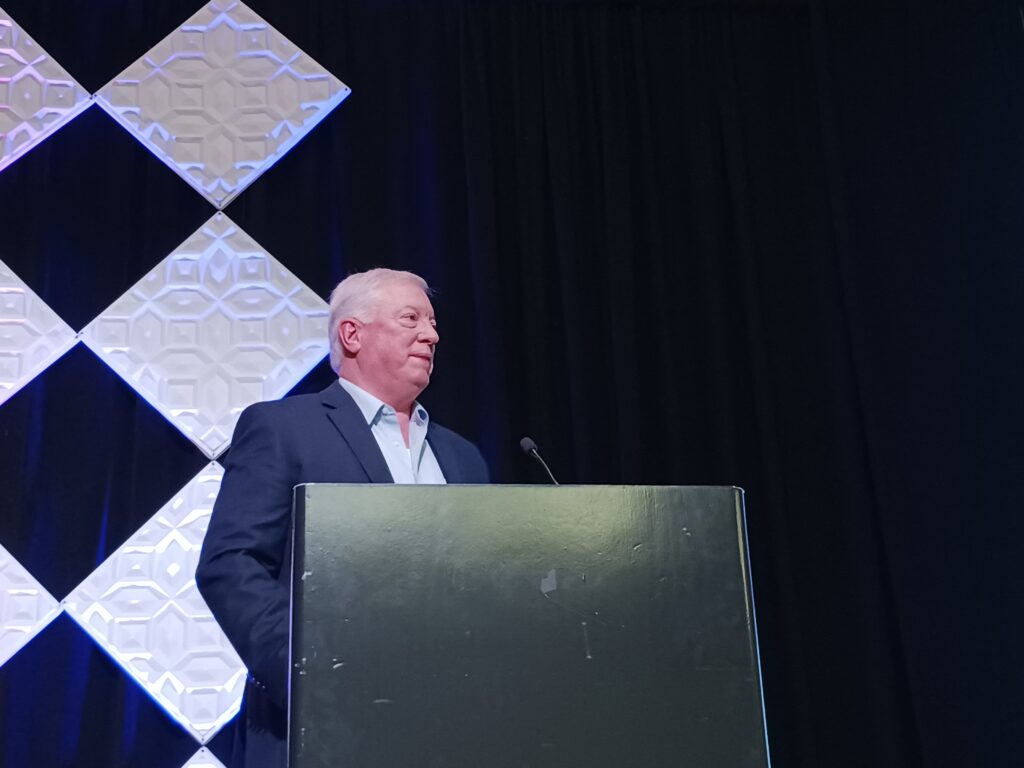
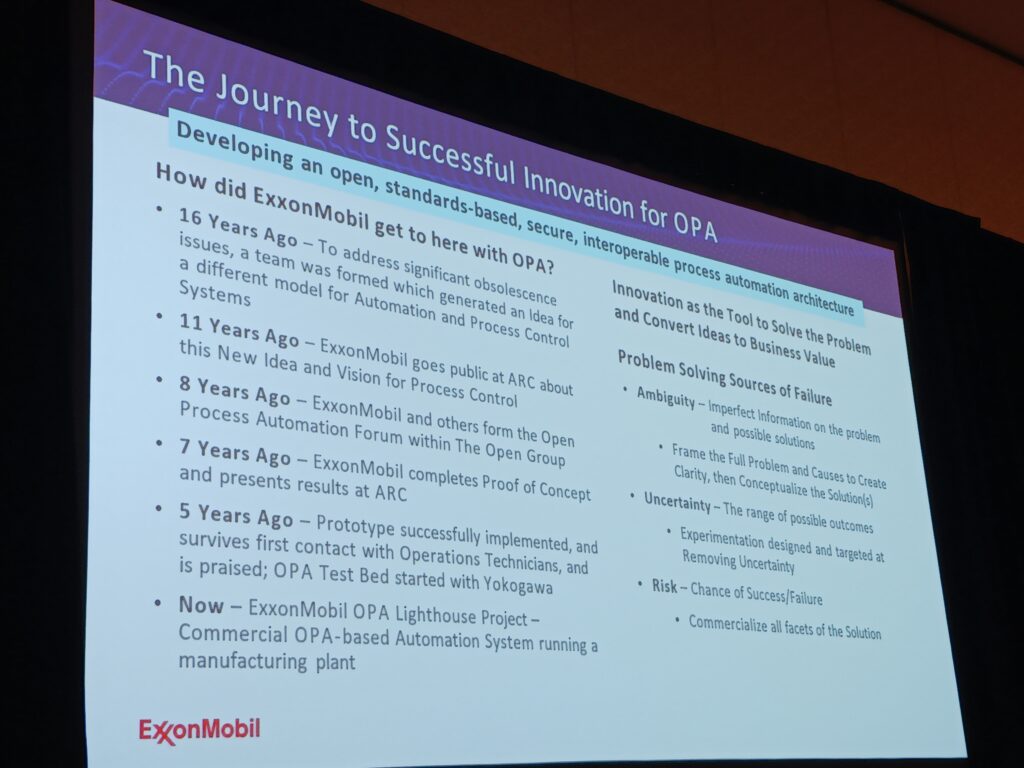
OPA ExxonMobil Lighthouse Project, architecture
In addition to interoperability, O-PAS separates hardware and software, so, like information technology (IT) systems, incremental upgrades can be made over time on the fly, rather than often only during a large-scale distributed control system (DCS) upgrade every 20 to 30 years. Last year, those involved cited a 52% OPA hardware and software savings compared to traditional DCS.
The architecture for the ExxonMobil Lighthouse Project resin plant (Figure 3) has a control room operator console, advanced computing platform (infrastructure services, historian, advanced control and optimization, engineering tools, IEX 61499 runtime application and server for the human-machine interface [HMI]), multiple distributed control nodes (DCN) compute resources with IEC 61499 runtime applications all connected to an OPA connectivity framework. A DCN with a local I/O device connects to the OPA connectivity framework and marshaling to field devices. Other network I/O connect to the OPA connectivity framework and to marshaling and field devices also. In the process area, instead of connecting through marshaling, a DCN local I/O device and network I/O each connect to field devices through junction boxes.
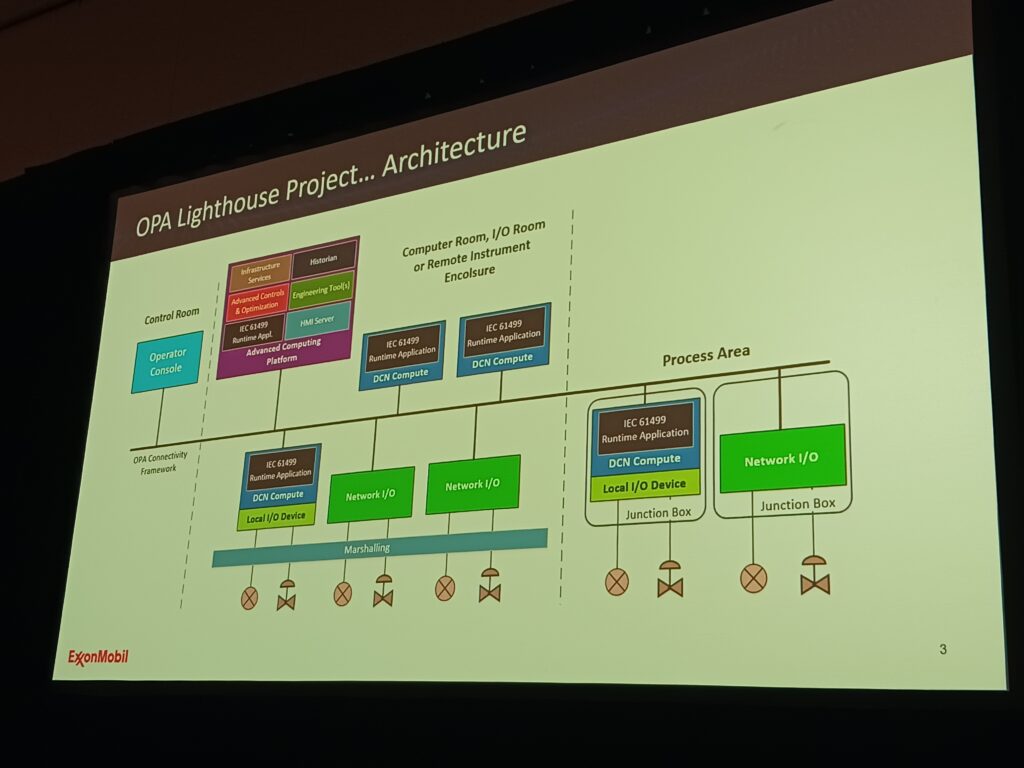
Enabling Open Process Automation technologies include deployment of virtualized controllers for DCS and programmable logic controller (PLC) automation systems. Harry Forbes, research director, ARC Advisory Group (Figure 4), discussed 2024 open automation survey results, showing about half of respondents expect to widely deploy virtualized PLC and DCS controllers by 2030. Forbes praised the OPA efforts and called on more end users to require Open Process Automation in requests for proposals (RFPs).
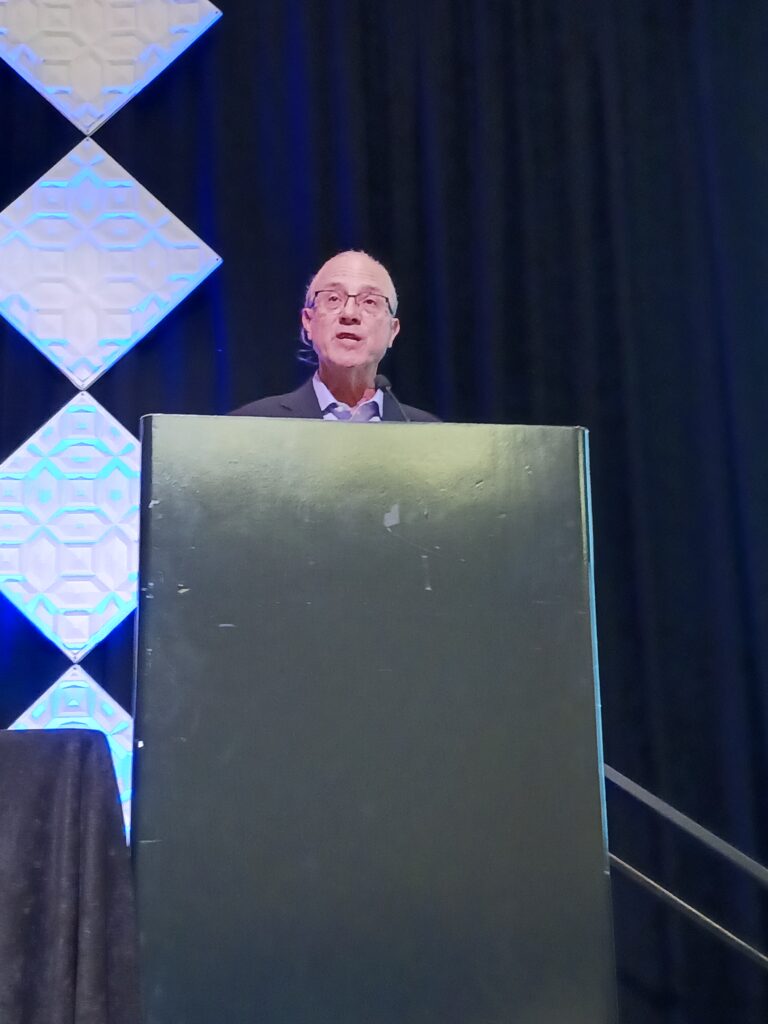
OPA ExxonMobil Lighthouse Project, architecture
The Lighthouse Project clears the way for more commercial installations of O-PAS, DeBari said, who called it a group effort beyond ExxonMobil because of involvement from Open Process Automation Forum (OPAF; more than 100 members, part of The Open Group), including Shell, DuPont, Yokogawa and Supcon, among others.
The implementation timeline and results (Figure 5) was rigorous, but not perfect, DeBari said.
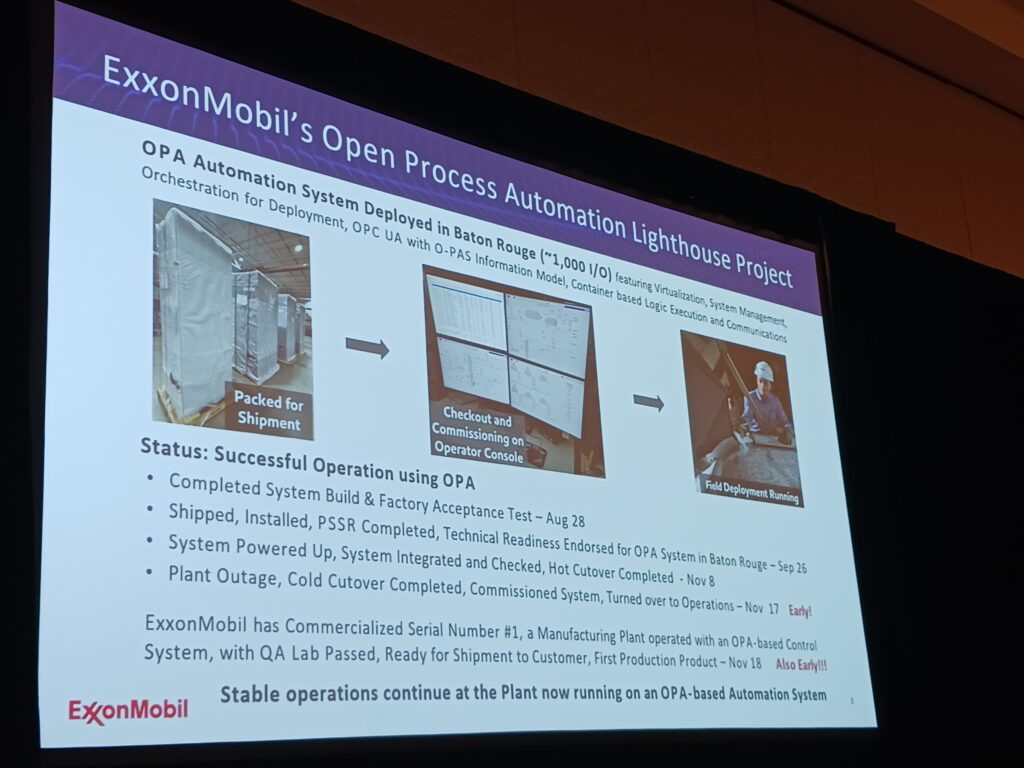
- Aug. 28, 2024: During an extensive factory acceptance test, it took operators all of six minutes to find the first mistake.
- Sept. 26: Changes were made, and the system was shipped and installed.
- Nov. 8: It was powered up and checked, and hot cutover was Nov. 8.
- Nov. 17, early: During a scheduled plant outage, the O-PAS system was commissioned and turned over to operation.
- Nov. 18, early: First sold production.
- Feb. 12, 2025: Stable operation has continued since, and operators are happy: (Toriano) Tito Jackson, ExxonMobil, operator (Figure 6) using OPA in Baton Rouge, was confident enough to leave the plant and get out of town after years of being close by in case a DCS on-site needed help.
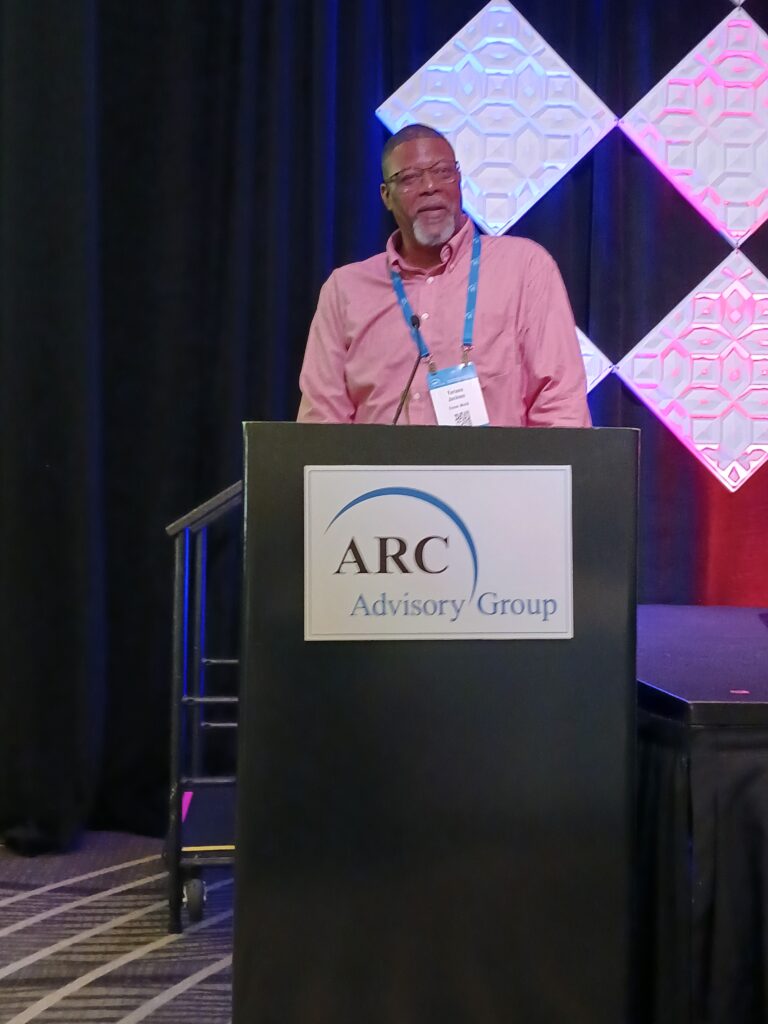
OPA differences compared to migrating a DCS
Dave Hedge, ExxonMobil technology and engineering, (Figure 7) who’s worked through 21 process control system conversions, said the project phases using O-PAS v2.1 include preparation, engineering and manufacturing operations experiences (Figure 8). The plant returned to typical process improvements and operations changes via automation system modifications like normal. Hedge said the difference between migrating a traditional DCS system compared to migrating to OPA is like the difference between using pencil and paper and a tablet computer.
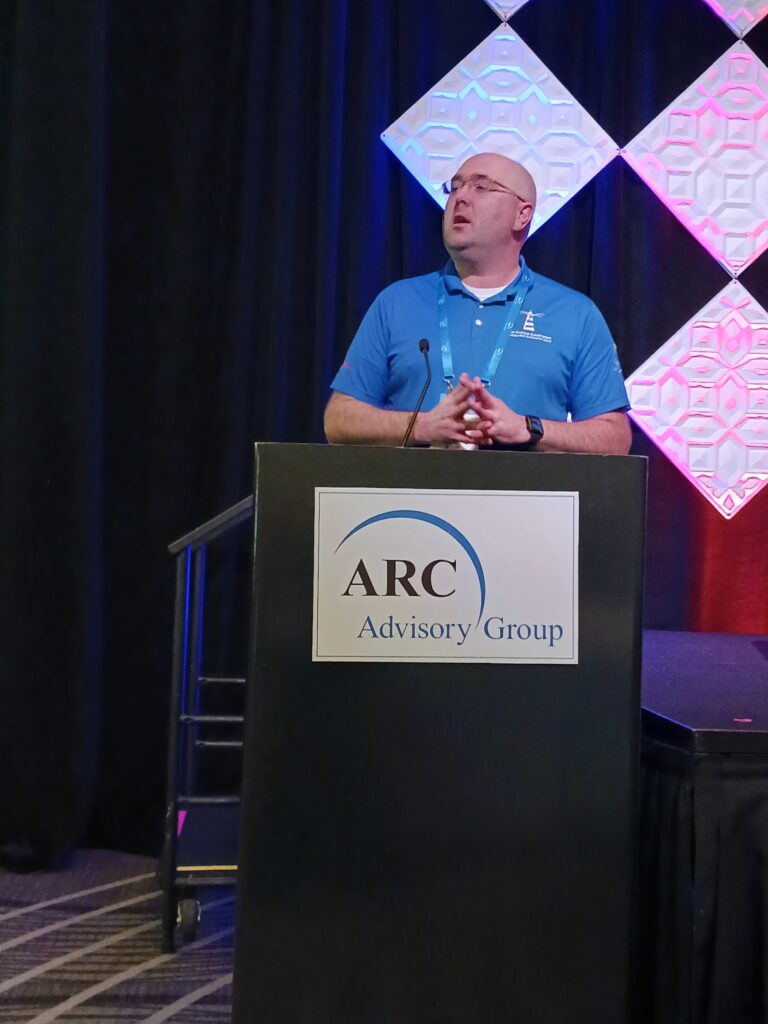
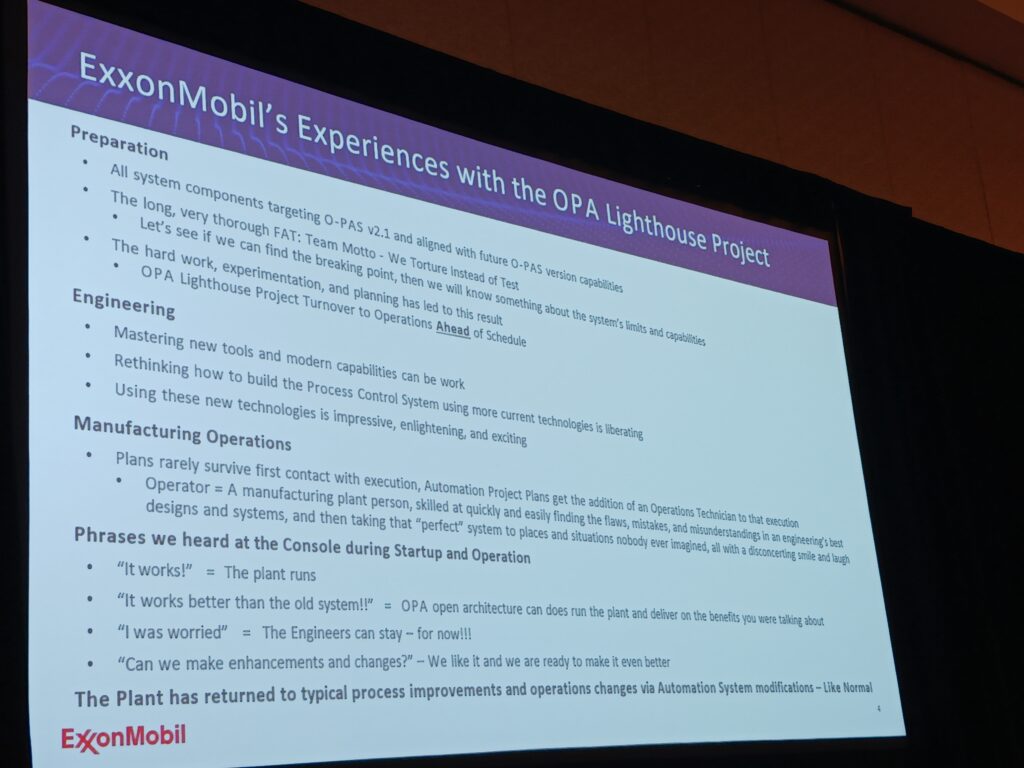
Hedge said operators have asked to make enhancements and changes to the system. They show each other tricks. Also, he said, not a piece of the prior DCS is left. Often DCS transitions are so involved that parts of the old system (I/O, for instance) are left in place for replacement another time. Or the prior system may be left on-site in case the new one wouldn’t operate as needed.
Other OPA transition benefits include:
- Skill building for internal and ecosystem capability
- Cybersecurity – IEC/ISA 62442, role-based access control (RBAC)
- Automating the automation system
- OPC UA for control communications
- Advanced computing platform, an operational technology (OT) data center, small to extra-large, with good, better and best, containerized software.
- IT technology in the OT space – Linux, mesh networks, firewall rules, virtual local area networks (VLANS), and more.
- Ability to install and run controller in less than 20 minutes.
- Plug-and-play reality.
Next OPA project for ExxonMobil
Kelly Li, ExxonMobil, commercial lead (Figure 9), with the company for 19 years, said ExxonMobil is working on more commercial deployments of open, secure and standard-based systems. The company is seeking to use commercially available products for the OPA vision. She expects PLC and supervisory control and data acquisition (SCADA) projects next.
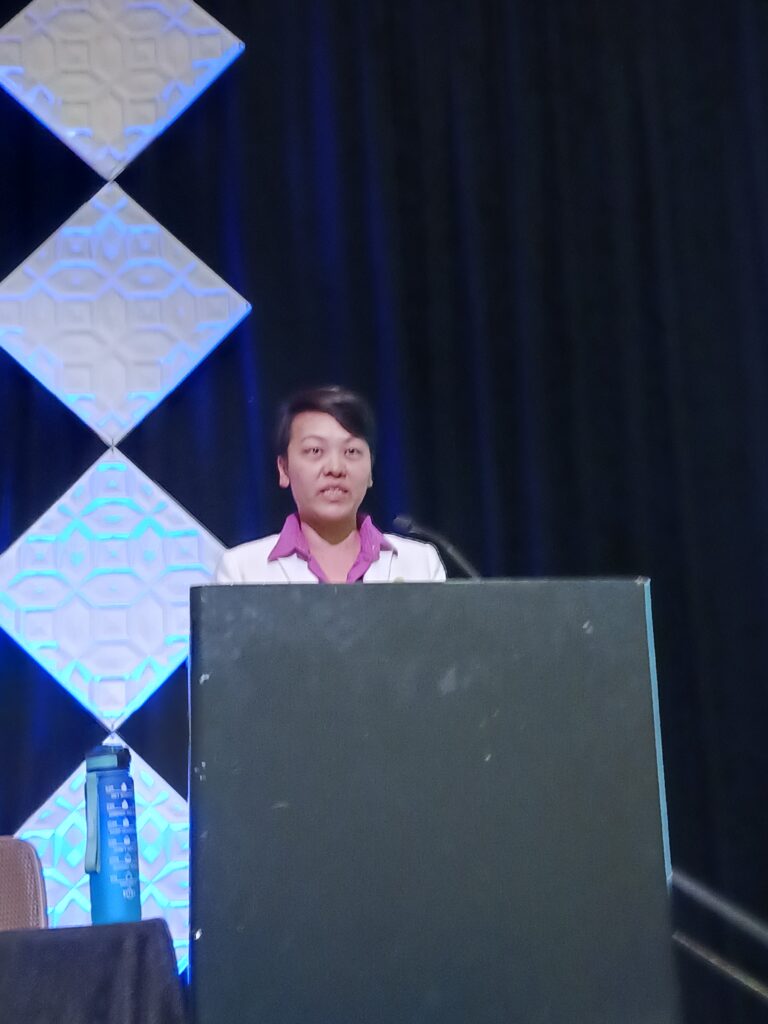
Those involved are collaborating with end users and system integrators in ecosystem development (beyond energy). The effort supports standards from OPA Forum and also UniversalAutomation.org, PICMG, NAMUR and International Association of Oil & Gas Producers (IOGP).
Li said a Feb. 10 OPA ExxonMobil article tells more.
The open, secure and standards-based efforts continue with a vision for a scale-up plan and OPA ecosystem. Open Process Automation is a mature ecosystem (Figure 10) that supports OPA deployments with interoperable options, intrinsic cybersecurity, scalability, portability and transferability, Li said. This year will expand multiple steppingstone projects, with opportunity for more SCADA/DCS implementations, she continued.
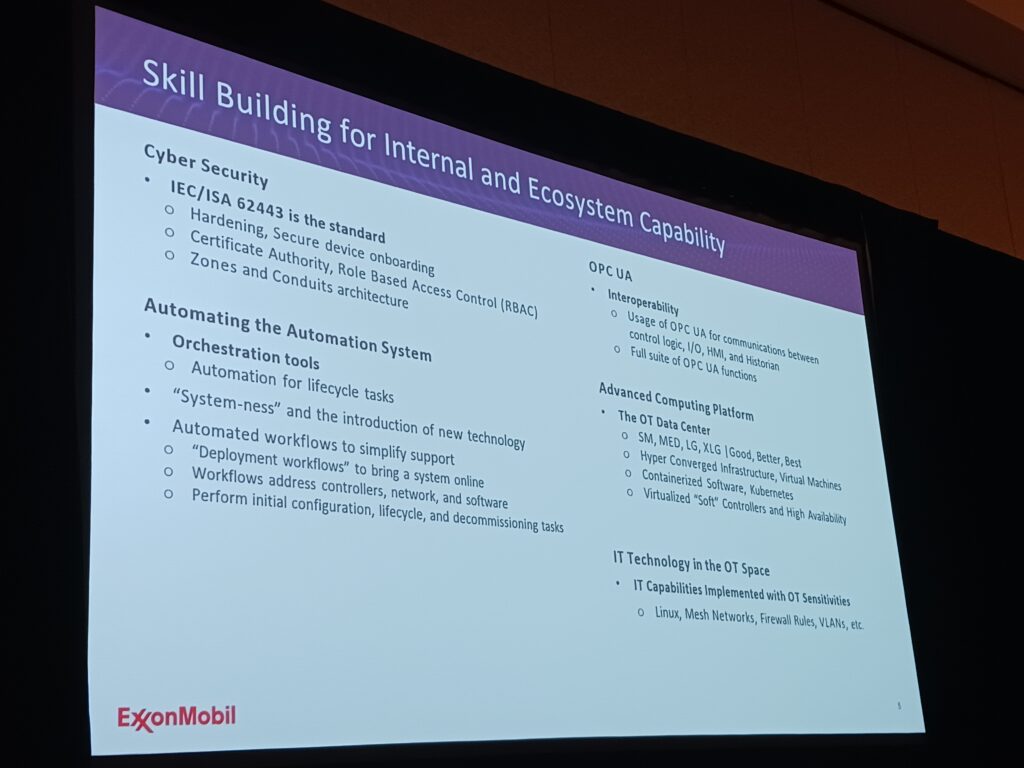
The OPA project midstream terminal PLC-type project, request for proposal (RFP) resulted in multiple proposals for commercially available solutions.
Later this year in a chemical business, engineering, procurement and construction (EPC) begins with a medium-sized DCS greenfield implementation; an RFP is expected later this year.
OPAF launched the O-PAS certification program for v2.1, useful for automation vendors, components suppliers and system integrators to create more commercially available offerings and solutions using the open-standards based, secure interoperable standards.
Li added: “I’m excited to see the future impacts. I call on other end users, suppliers and system integrators to move into the future to realize the benefits of lower TCO for deployment in field. We need more deployments.”
OPA Forum roadmap
Jacco Opmeer, Shell, (Figure 11) representing the OPA Forum, outlined other 2024 major achievements in a roadmap. O-PAS V2.1 is working in a large commercial installation. Connectivity provides glue between distributed control nodes (DCN) and the advanced computing platform (Figure 12).
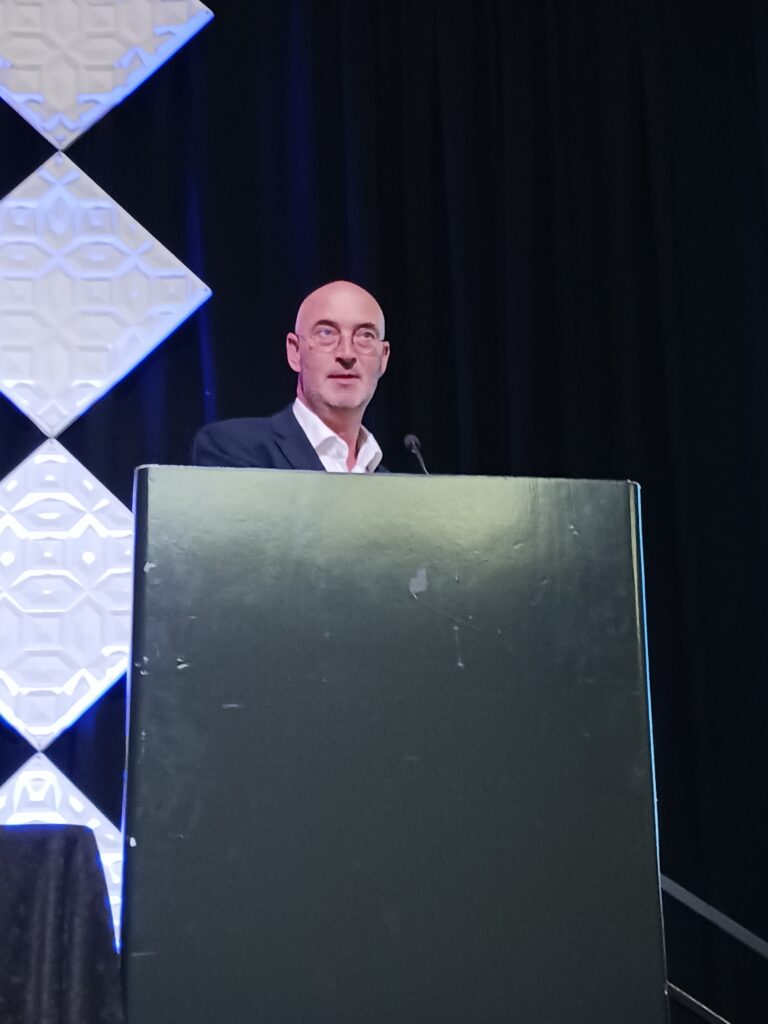
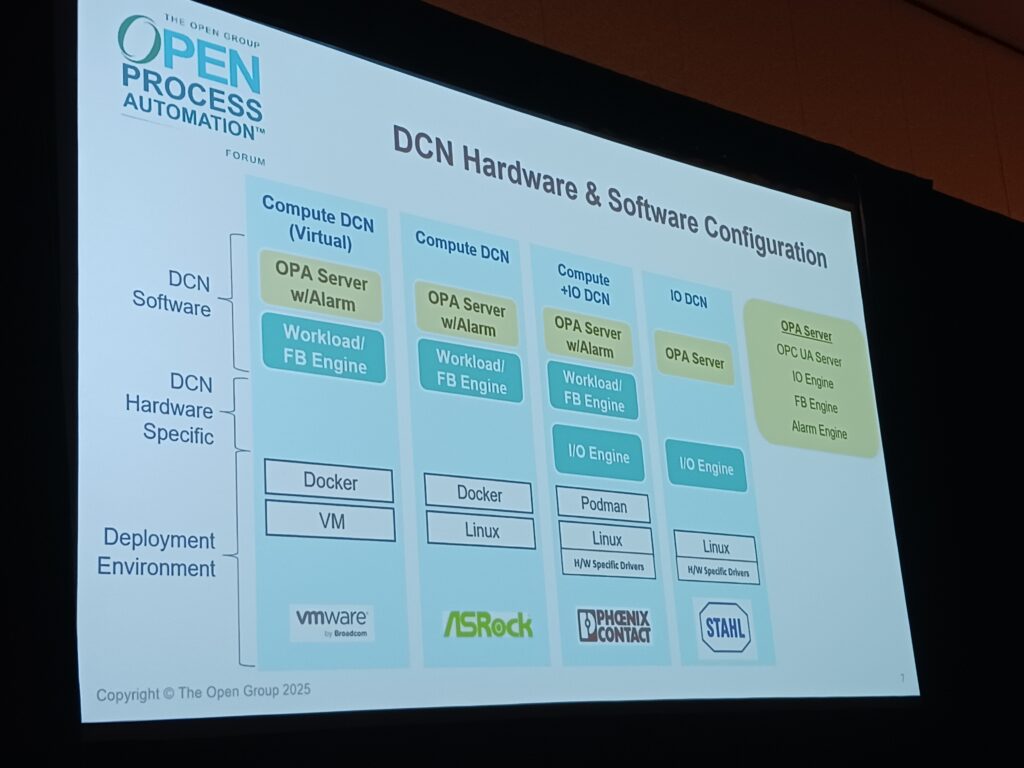
Among 100 OPAF members are most major automation hardware and software suppliers, most major process automation system suppliers, many large end users and system integrators, Opmeer said.
O-PAS Certification has launched; next is verification lab recognition for physical platform certification and network capabilities. The idea for the standard is that automation should be plug and play, like USB, Opmeer said.
The O-PAS interoperability event in the Shell offices in Amsterdam, was a plug fest with a week of interoperability testing among vendor products prototypes and proof-of-concept applications.
Semantic versioning includes content to be added incrementally to O-PAS when ready; incremental updates will be in edition 2, V2.1, Opmeer said, such as:
- Security, OPC FX
- Architecture and hardware updates
- AutomationML portability
- Orchestration – management of O-PAS components.
How end-users benefit from the ExxonMobil Lighthouse Project
Dave Emerson, Yokogawa, and co-chair of enterprise architecture of the OPA-S working group (Figure 13), said end-users from around the world have been interested in Lighthouse Project benefits because of many commonalities at their facilities, including:
- Brownfield obsolescence, end of life issues, obtaining new technology value.
- Greenfield: New facilities and new processes need new architectures. Many seek ways to feed artificial intelligence (AI) applications with more content. Applications can create new value with O-PAS to get attention quicker.
- Lowest total cost of ownership (TCO): There’s lot of interest in gaining value over longer time scales.
- Interoperability, interchangeability, modularity and flexibility are key drivers for rethinking process automation applications.
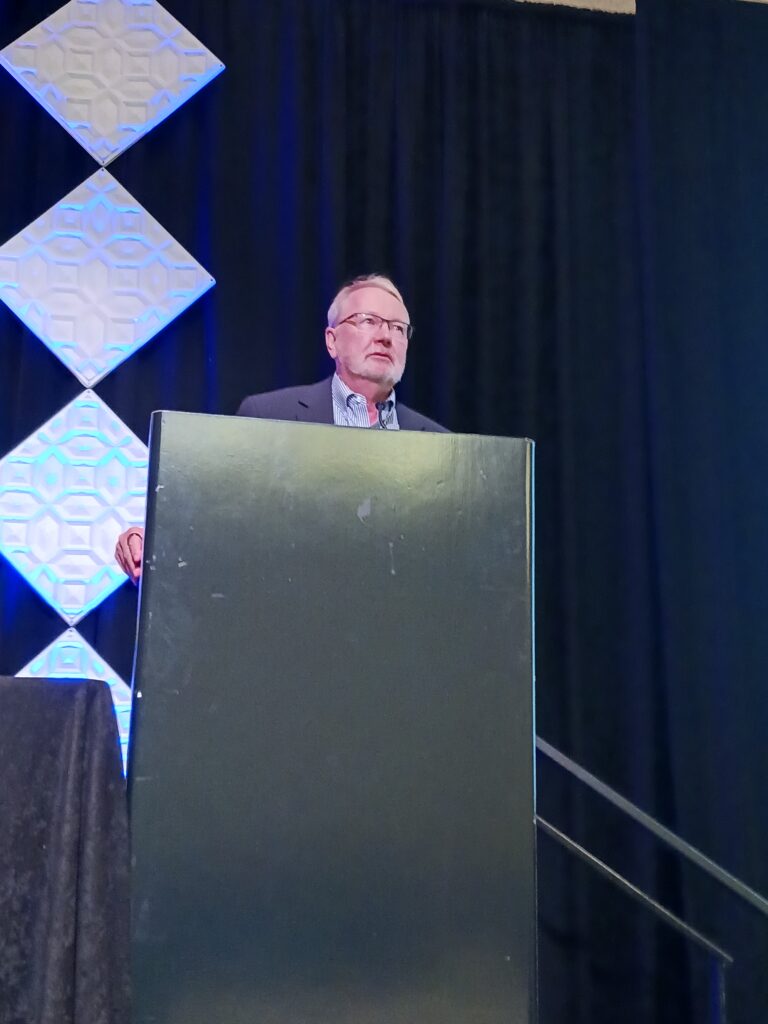
OPA System components explanation, hardware, software examples
Process automation hardware is important, Emerson said, but hardware is a place to deploy software to, explaining how an Open Process Automation system works (Figure 14). OPA provides ability to move and orchestrate where to move software and when. OPA has two categories of software functionality, where the processes and applications run and how to manage HMI for operators.
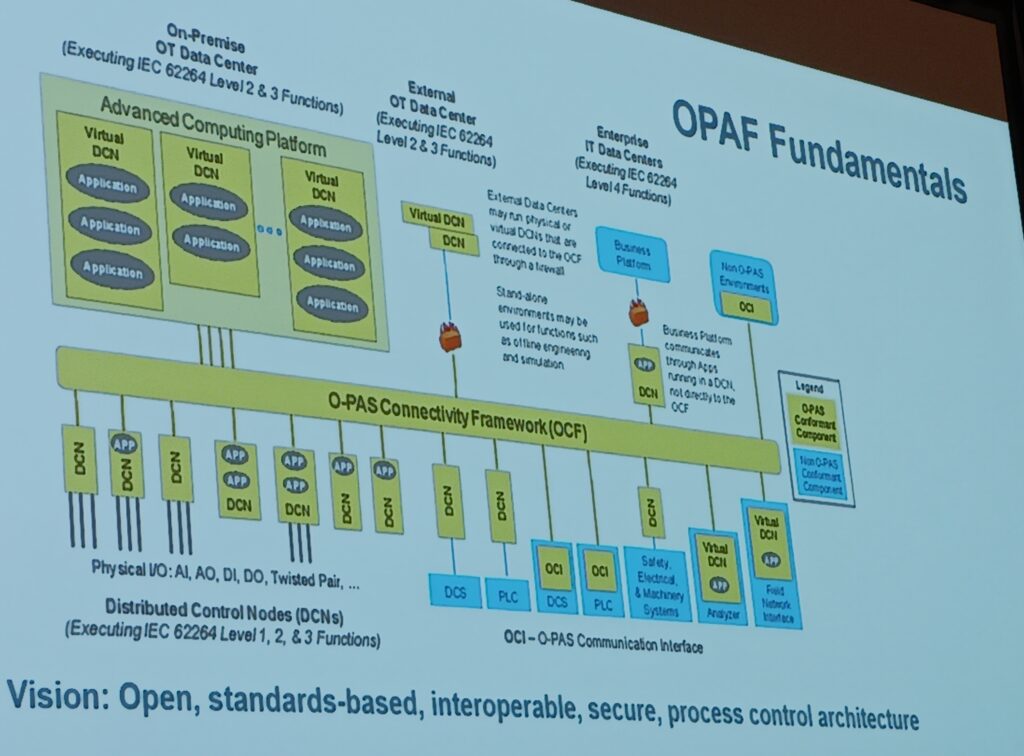
While components are interoperable like in the IT world, the installed system looks like a familiar DCS for the OT world, Emerson explained: It’s what’s operators are used to. Historization capability provides quality data to historians to collect more efficiently and move data around faster as needed without a full system upgrade. You don’t have to rip out everything to upgrade to more open capabilities, he said. At least 50 OPA-compliant packages have been installed at one customer in connect and build system. Virtualization and containerization help manage controller workloads. Cybersecurity management is built in, and onboarding is easier. Distributed control nodes put capabilities where needed. It opens up the question: What will software do for me?
At the ARC Leadership Forum, in the Yokogawa booth, Yokogawa web-based software (CI Server HMI) showed a Phoenix Contact Control Plus DCN, an R. Stahl I/O DCN and an ASRock Control DCN operating on one screen.
In addition, two OPA hardware configurations with different plug-and-play components were shown, one at the Collaborative Systems Integration (CSI) booth (with a COPA500 Controller, Phoenix Contact for power and I/O, an ASRock controller, Supermicro HMI and a Cisco gateway, Figure 15) and another system at the Wood booth using R. Stahl I/O.
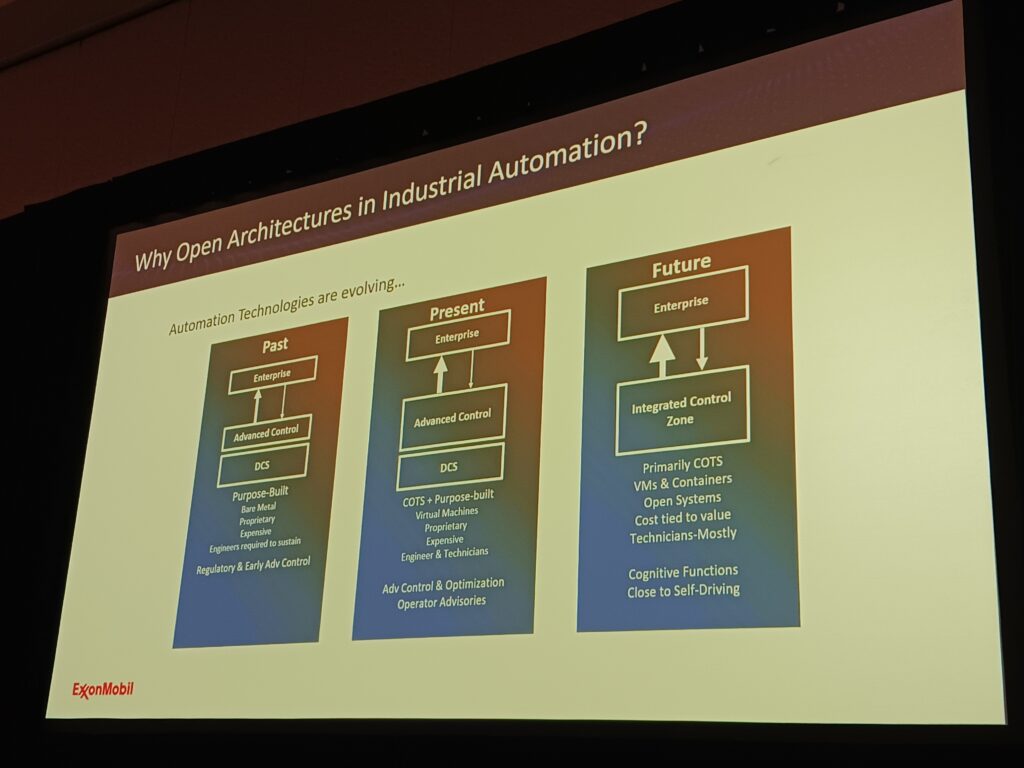
Process control experts discuss OPA benefits, opportunities
Asked about the size of the implementation, DeBari said the ExxonMobil Lighthouse Project resin plant is a commercial installation with 1000 I/O and 100 controllers, a project focused on Open Process Automation systems, not for all surrounding devices and systems, which he called “urban renewal.”
Li said the next ExxonMobil project using OPA has 200 I/O.
Asked about OPA progress, DeBari said the Lighthouse Project marks the end of the OPA R&D stages, as many commercially available products are available. “Now every project can decide if will use OPA.”
Regarding training and support, DeBari said ExxonMobil group its people to the Woodland Texas facility before and during the factory acceptance test to progress. Keeping the same HMI screens helped reduce training time to a week. The system has more cybersecurity than any other system, and has a contract with a system integrator for software and hardware support, instead of with a DCS vendor. While the system and operators need some support, common skills are used; special operator knowledge was not required.
Michael Hotaling, ExxonMobil, innovation and strategy digital manager, leading the digital twin working group, said it’s important to envision a world where automation users stop buying dumb equipment and demand open and agnostic equipment. When do we stop buying things that do not communicate with open standards? So much has been an afterthought.
Hedge said automation is necessarily changing from closed to open architectures in industrial automation, as he outlined the past, present and future evolution of process automation toward open architectures (Figure 16). “Stop saying no. Say yes.”

Using the OPA Lighthouse Project software-defined architecture as an example, when a new widget comes out with better capabilities, it’s possible to change system as it sits in the facility today.
More operator perspective about Open Process Automation
Jackson provided additional operator experiences with the new system, paraphrased below.
- I supported three DCSs in Baton Rouge for 14.5 years, and thought, “Wow. Something new.” It seemed like a lot to support, at first. I was skeptical. When I learned more about it, I wondered why IT technology was stepping into my OT area. Working with it, I started to enjoy it. It works. It’s running. And now I see endless possibilities.
- I love to get back into IT learning.
- It has a small footprint.
- Saw the finish line sooner than with a DCS transition.
- I don’t have to be there physically. I took my first vacation in two years.
- This is a big toy store for me.
- It’s nice not to have phone calls throughout the day.
- It’s new technology and people, an exciting journey. I know artificial intelligence (AI) is coming, and I’m enjoying it.
- While I don’t like change, I’ll stick with this.
- I hope more users will adopt OPA. It’s really cool. I could run 100 DCNs on the platform. You have to reimagine what you can do.
Hedge said those involved have to be good at the fundamentals; that’s the same. Standards make it easier. Among lessons relearned (Figure 17), we were reminded that innovation is a journey. Some want to participate and others do not. Software upgrades can be done at a component and system levels, online and offline.
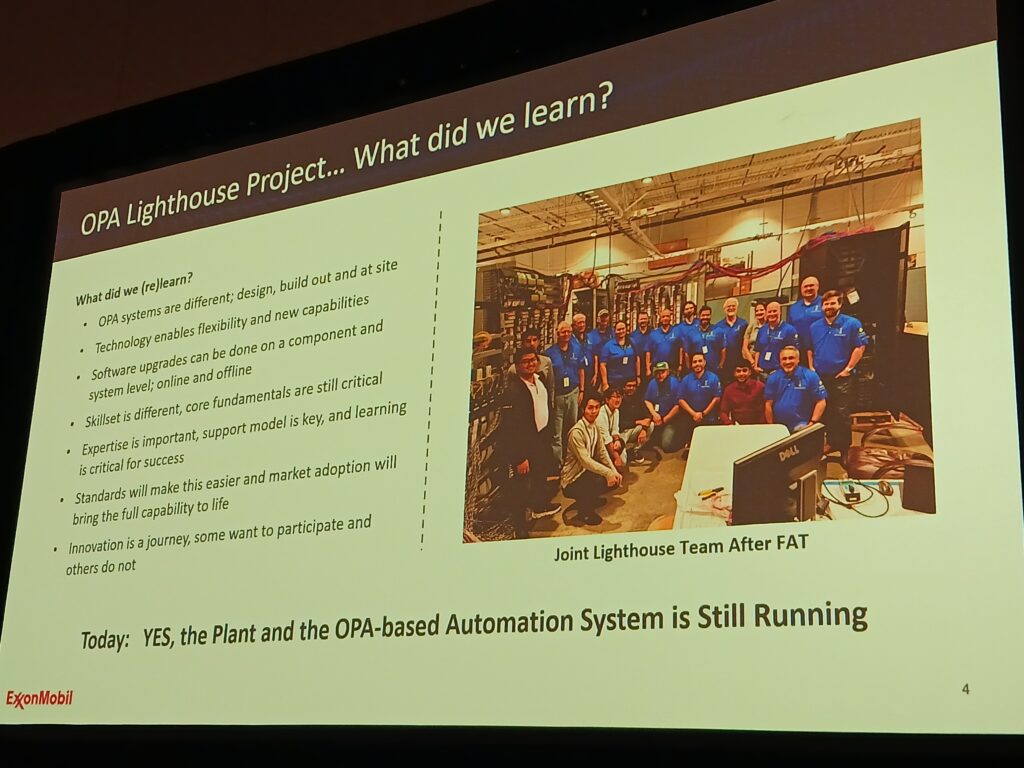
Applying artificial intelligence to Open Process Automation
Addressing what’s needed to make systems more autonomous with AI use, Mark Hammer, global account manager, Yokogawa, said a rich data model, with consistent integration and common data sets will help rather than data conversions and gateways used for data in many of today’s systems.
Don Bartusiak, president, Collaborative Systems Integration, said sensors and their application need to be reliable with correct sampling. You cannot paper over instrumentation with AI math. Proper training is needed, also.
Hedge said compute power is needed for networking, data communications and “for fancy things in future efforts.”
Are younger operators needed for OPA and AI implementations?
Jackson acknowledged that everyone’s different. If I see it a few times, I pick it up. It’s not hard. With my experience, I can fix things without calling for help.
Hedge said virtualization was a hot topic in colleges during the decade ending in 2010. hot topic. Today’s universities are very cloud-centric.
Addressing if AI could be applied to a problematic temperature control loop tuning challenge, Bartusiak said AI isn’t going to replace control anytime soon. There will be a mix of technologies. AI might help if an application has sticky valves that cannot be fixed right away; reinforcement learning may help in the meantime. Open platforms will enable companies to innovate faster than they could have previously.
Comparing traditional DCS migration to OPA upgrades, Bartusiak said one creates a massive disruption and the other is as easy as replacing a laptop has become. “You can incrementally upgrade. It’s much less costly and less disruptive than looking backward.”
A more capable, more upgradeable system, applied to a small modular power plant, for instance, might be capable of autonomous operations, in perhaps 10 years, said Timothy Triplett, control consultant, Texas A&M University.
Bartusiak said for routine operations, plants can be autonomous, but manual attention is required to handle a small number of infrequent circumstances that arise. It’s like autopilot on airplanes; computers cannot handle low-frequency events; well-trained pilots take over.
OPA is how to avoid the pain and expense of DCS migrations
Whit McConnell, chief engineer, automation and process control, ExxonMobil, said the OPA effort results from explaining to management the costs and time required to modernize a fleet of DCSs. “There were really big numbers, producing facial expressions we didn’t want to see. They asked us to rethink the problem. OPA prevents the DCS upgrade scenario every 15 to 20 years.
Obsolescence is a way of life in our industry, with operating systems still around since the late 1970s, 1980s and 1990s. In the meantime, can retrofits and upgrades be more open? Yes.
Vien Nguyen, principal software architect, Yokogawa, told Control Engineering that an OPA system is never done, always improving and providing additional benefits.
Mark T. Hoske, editor-in-chief, Control Engineering, WTWH Media, [email protected].
CONSIDER THIS
Are you requiring Open Process Automation in your next request for proposal?
ONLINE
See a Control Engineering 2024 series about open automation starting with: