The world is filled with missing feedback loops that could improve performance if those loops were closed. Learn how your automation knowledge can help others.
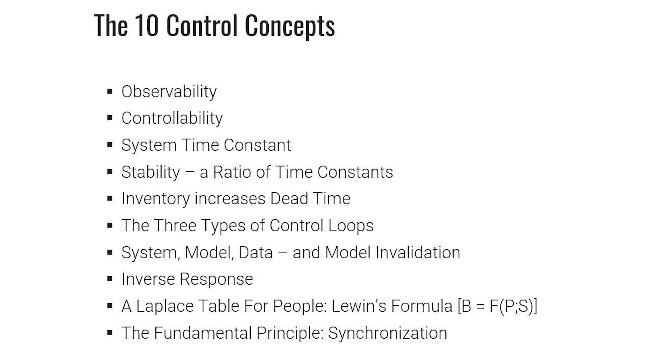
Learning Objectives
- Adoption of Industry 4.0 architectures is easier by applying control concepts.
- Learn to observe, orient, decide and act.
- Visibility, observability and feedback help improve organizations.
Closing feedback loops can improve performance outside of traditional control systems, when applied to other areas of operations, organizations, and supply chains, suggested Dr. John F. Carrier, Senior Lecturer, System Dynamics Group, MIT Sloan School of Management. Dr. Carrier’s presentation, “Applying Control Concepts to the Adoption of Industry 4.0,” was among 17 professional development hour sessions in the CFE Media and Technology spring Virtual Training Week, March 29 to April 2. The presentations are available for viewing on demand.
Carrier used examples to show how controls and automation expertise can help the world, which is filled with open feedback loops that could improve performance if the loops were closed. Deadtime can hinder progress. Technology advances have decreased the cost of controls, resulting in less than $100 for a control loop with sensors and a stack platform for the Industrial Internet of Things (IIoT).
Control concepts help other applications
Carrier said many automation concepts can help in other applications. These include observability, controllability, system time constant, stability, inventory of dead time, model data, model invalidation, inverse response, and synchronization.
Sensors and appropriate logic devices help to detect the state of the system prior to the consequence. For example, when the stopping distance of a bicycle exceeds the visual distance of bicycle light, events that normally would be avoided, now come into play, ultimately resulting in tragic consequences.
Loss of observability can create industrial accidents, Carrier said. Quickly understandable human-machine interfaces (HMIs) connected to control systems can extend control engineer knowledge to the people who work in the plant, he suggested. Loss of controllability can be prevented with effective remote monitoring, predictive maintenance, machine learning, digital twins and education.
Time constants extended to the organization level can be explained by a Jack Welch quote: If the rate of change on the outside exceeds the rate of change on the insides, the end [of your system or organization] is near.
Observe, orient, decide and act
Col. John Boyd’s concept of observe, orient, decide and act (O-O-D-A) can be applied to a broad range of applications, Carrier said. Korean war fighter jets from the U.S. performed better because the pilots had better visibility, showing better visibility mattered more than better performance attributes such as speed, thrust and turning radius. Investing in technologies to improve observation, visibility or transparency can produce rapid positive results.
About the orient step, Henry Ford said: “Whether you think you can, or you think you can’t — you’re right.”
To change a system, an organization has to change its mental models – the way the people in the organization think. Better to change the action (by providing new data or work habits) and how the work is done, then the models change as a result. That works better than explaining the need for change, Carrier said.
Technology provides better observation by getting data where it’s needed for rapid analysis.
Carrier noted that Dirk Didascalou, vice president IoT, Amazon, said the IoT is about knowing where everything is, all the time.
As for stability, consider the system’s control response time. If a customer places order and gets a delivery deadline that isn’t kept, other system disruptions are created. To improve system stability, deliver before the deadline. By improving preparation, then execution more often is on time, making deliveries on time and saving larger amounts of time later.
Other controls advice for companies
Other advice from Carrier’s presentation includes the following.
- Too much work in process slows companies’ response times (Little’s Law).
- Rework and special requests from management slow entire systems and distort the system’s time constant.
- As models represent processes or systems, keep in mind data is the difference between model and the process. Negative feedback loops is why we collect data to produce value for organizations.
- Controllers are based on a model. The better the model, the better performance with lower risk.
- Regarding preparation, agility and iteration: Everyone needs good preparation, but agility also is needed. You cannot plan forever. Learn from iteration.
- Just replacing old elements with new elements won’t create much positive change. Carrier cited Kurt Lewin, Founder, MIT Center for Group Dynamics, 1945-47: If you want to understand a system, try to change it.
- Control systems adapt to implement sustainable change. Prepare, run and observe defects and adapt. • Control systems improves with feedback for fewer defects and improved operations.
- When a system needs more time, it first borrows, then steals from the system.
- Industry 4.0 allows organizations to incorporate adaptive control concepts. It will be easier if those doing so understand control system design principles.
Visibility, observability, feedback
In the question-and-answer session of the presentation, Carrier offered more advice.
Q: How can operations help increase visibility in other areas of an organization?
A: Carrier suggested showing video clips of what’s going wrong to management, to make visible what’s hiding. Asking those involve to record videos of where they need help is useful. Let them own it.
Q: Among control concepts discussed, can you pick a few that should be applied more often in manufacturing settings and aren’t?
A: Observability. Get to the factory floor or the back office and find missing feedback loops. Correcting issues downstream, correct errors but won’t fix what caused errors. Address root causes to avoid institutionalizing errors and paying suppliers to correct what could be fixed.
Q: What controls technologies are helping manufacturers affect change than in the past?
A: Use feedback loops to check key parameters at regular intervals.
Think again if you consider control concepts only for automation; accelerate your organization’s implementations of Industry 4.0 and Industrial Internet of Things architectures.
Mark T. Hoske is content manager, Control Engineering, CFE Media and Technology, [email protected].
KEYWORDS: Control concepts, Industry 4.0
CONSIDER THIS
What value can you bring to your organization by helping to apply control concepts?