For better understanding of what’s possible in advanced process control (APC), learn what APC 2.0 is and why it is important. Explore APC agility and importance of APC technology mastery for control-loop optimization. This starts an APC 2.0 series.
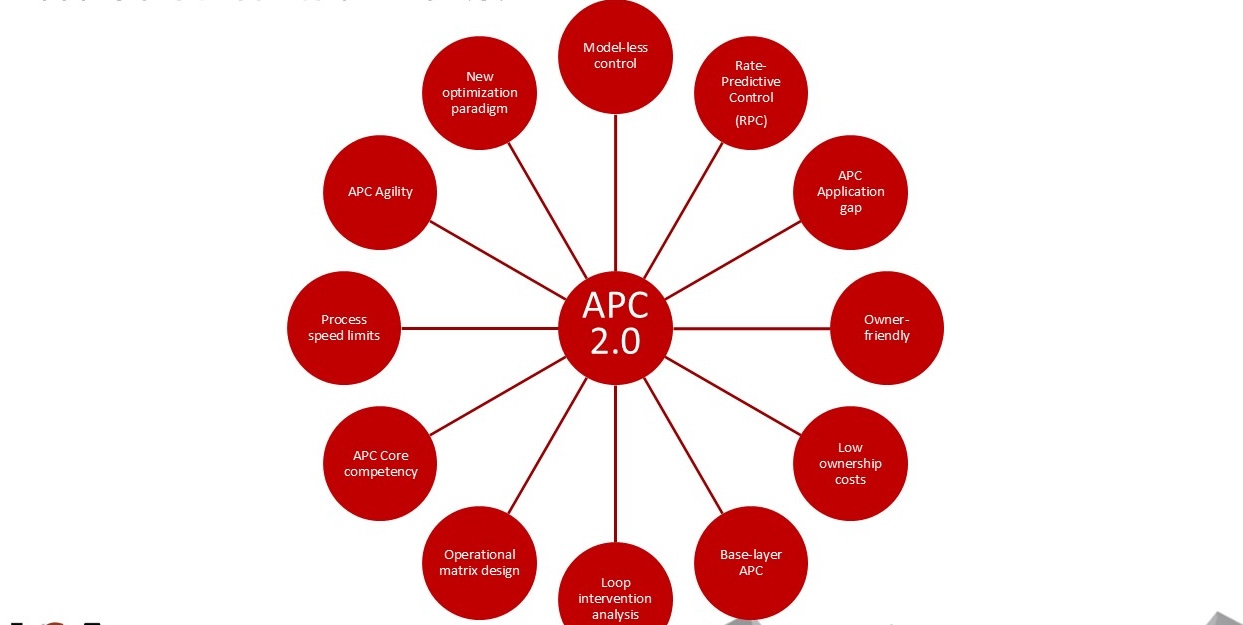
The idea behind “APC 2.0” is that the conventional advanced process control (APC) paradigm of the last 40-plus years, which could be called “APC 1.0,” is due for an overhaul. Most people would probably agree with this, but they may not yet know the specifics of APC 2.0 – what it includes, what’s different, how it solves past challenges, how it helps move APC forward again and why it is important.
An updated APC paradigm is especially important because one of the lessons learned during the APC 1.0 era – possibly the most important and basic lesson – is that multivariable control and optimization is not a specialized or optional capability. Rather, multivariable control and optimization is a fundamental aspect of nearly every industrial process operation. Without APC technology, multivariable control and optimization is carried out manually (or open-loop) by operating teams. With APC, it is automated (or closed-loop). Either way, with or without the aid of APC technology, operating teams must master multivariable control and optimization to become effective, safe and reliable top-tier operators.
Importance of multivariable constraint control, optimization
If you observe any industrial process operation, you will see multivariable control and optimization in action. It takes the form of console operators making setpoint and output changes; field operators making equipment adjustments; process engineers pushing to maximize optimization potential; and myriad communications and ancillary activities. All these activities have the common aim of multivariable constraint control and optimization, that is, keeping the process in a safe and reliable condition while maximizing the capture of optimization potential.
APC can help automate multivariable control, optimization
Obviously, to the extent multivariable control and optimization can be automated by the use of APC technology, it provides an advantage. Many processes, including large complex processes where APC has traditionally been applied, and relatively small processes where APC has traditionally been overlooked – sometimes called the application gap – will find themselves handicapped when it comes to achieving their modern automation and optimization goals, if they do not find the time and vision to master APC technology.
If multivariable control is an inherent part of every process operation, and every operating site must master it to the extent possible, then it follows that APC technology must become a more agile and owner-friendly technology. This is a lesson from APC 1.0 – a technology is only as effective as it is reliable, cost effective, and as its tools are easy to use. To thrive in a process operation environment, any technology (or any equipment) must be affordable, flexible and reliable.
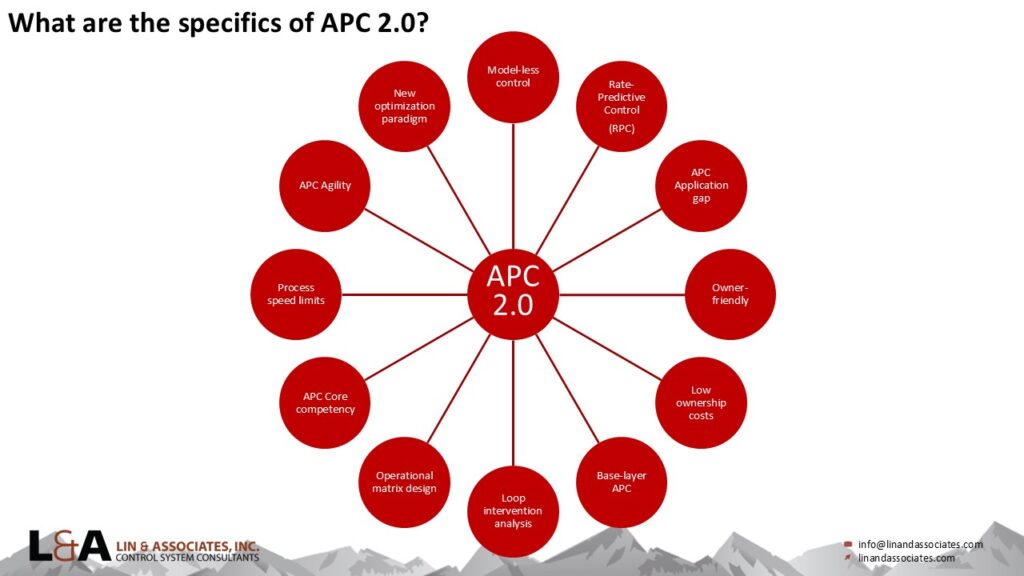
What’s involved in APC 2.0 and why
APC 2.0 incorporates many changes and lessons-learned that serve this end. APC agility means (among other things) costs that fall within normal operating budgets, so that it doesn’t break the bank or have to wait for funding; it means time frames that allow new opportunities to be captured and problems to be solved as they arise within a reasonable operational time frame – not a year or two down the road; it means APC work that can be included within projects, not as separate follow-on projects, without becoming critical path items; it means applications that are set-and-forget and do not require continuous support – or that fall apart without continuous support; and it means technology that can be effectively owned and operated by on-site control personnel without dependence on off-site specialists.
In APC 2.0, these characteristics of agility come about from a combination of lessons learned and new ideas that are sometimes novel and sometimes just common sense from process control and process operation points of view. The figure illustrates many of the main aspects of APC 2.0 that will be discussed in upcoming installments of this series.
In the APC 2.0 era, the central focus of APC will become closing multivariable loops, just like the focus of base-layer control has always been closing single loops. It’s fundamentally the same. If console operators have to intervene frequently to adjust outputs or setpoints – perhaps so frequently that they are sometimes overwhelmed – then something is missing. It could be a problematic single loop or – quite often – the root cause will be found to be a missing multivariable loop, so that the operator is actually serving as a manual multivariable controller, a job that could be automated via APC to close the related multivariable loops. Closing loops brings the universal automation benefits of more timeliness and consistency, fewer alarms and trips and greater optimization.
Are you intervening too often with control loops?
In APC 2.0, this fundamental aspect of operation – how often console operators have to intervene in control loops – is readily measured and managed using loop intervention analysis and the loop intervention metric. The loop intervention metric is also called the bad actor loop metric, because it is similar to the bad actor alarm metric from alarm management. If operators have to intervene too often, it needs to be addressed to assure safe and effective operation. In many or most cases, as the series intends to explain, an automated multivariable controller, that is APC, is the appropriate solution.
What’s in a name? APC, MPC, MIMO and other terms to know
Probably the easiest and most common way to talk about advanced process control is to call it “APC” and by that to mean “multivariable control and optimization.” Many other terms have been used, such as MPC (model-predictive control), MIMO (multiple-input-multiple-output), and MLC (multi-loop control). But APC is the most commonly used term.
Within APC, the terms manipulated variable (MV) and controlled variable (CV) are almost universally used, even if they can be counterintuitive at first. MVs are the control system “handles” that are directly manipulated by APC. Usually they are single-loop controller setpoints or outputs. CVs are the control system dependent variables that are indirectly controlled, by virtue of the MVs, such as various temperatures, pressures or stream qualities.
APC is shorthand for multivariable constraint control and optimization. In APC, MVs are manipulated within limits to keep CVs within limits (to the extent possible). This is multivariable constraint control. Secondarily, after constraint control, MVs are further manipulated to bring MVs and CVs to their most optimal values (to the extent possible). This is optimization.
Allan Kern is principal APC Consultant with Lin & Associates Inc. Edited by Mark T. Hoske, editor-in-chief, Control Engineering, WTWH Media, [email protected].
CONSIDER THIS
Are you attending to control loops too often in your processes? Perhaps you need APC 2.0.
ONLINE
For more insights from Allan Kern, see: